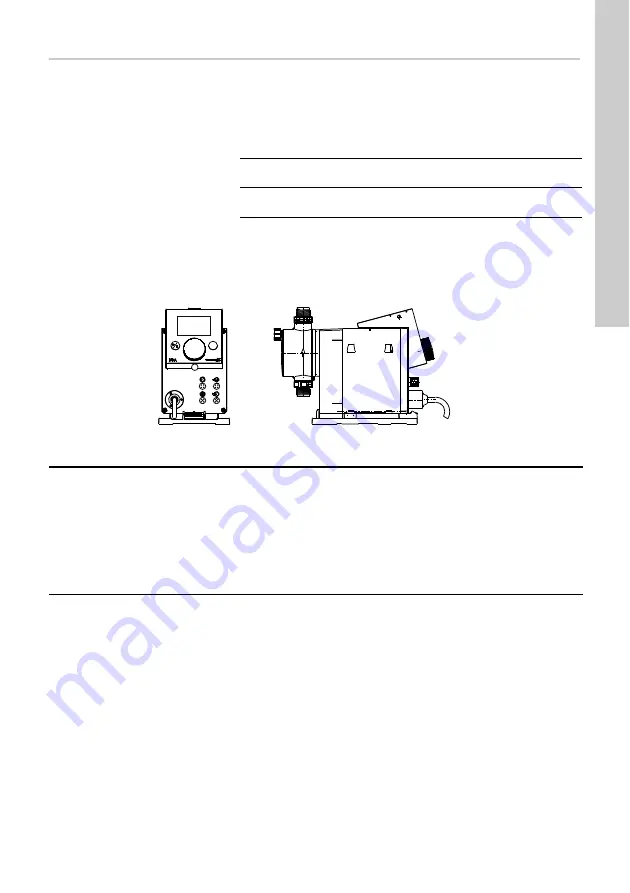
A
ppend
ix
39
Appendix
1
Safety declaration
Please copy, fill in and sign this sheet and attach it to the pump returned for service.
Fault description
Please make a circle around the damaged parts.
In the case of an electrical or functional fault, please mark the cabinet.
Please describe the error / cause of the error in brief.
We hereby declare that the pump has been cleaned and is completely free from chemical, biological and
radioactive substances.
_____________________________________
Date and signature
_____________________________________
Company stamp
Product type (nameplate)
Model number (nameplate)
Dosing medium
T
M
04
1
1
8
5 1
1
10
100%
Summary of Contents for SMART Digital DDA
Page 1: ...GRUNDFOS INSTRUCTIONS SMART Digital DDA Installation and operating instructions...
Page 40: ...40...
Page 41: ...41...