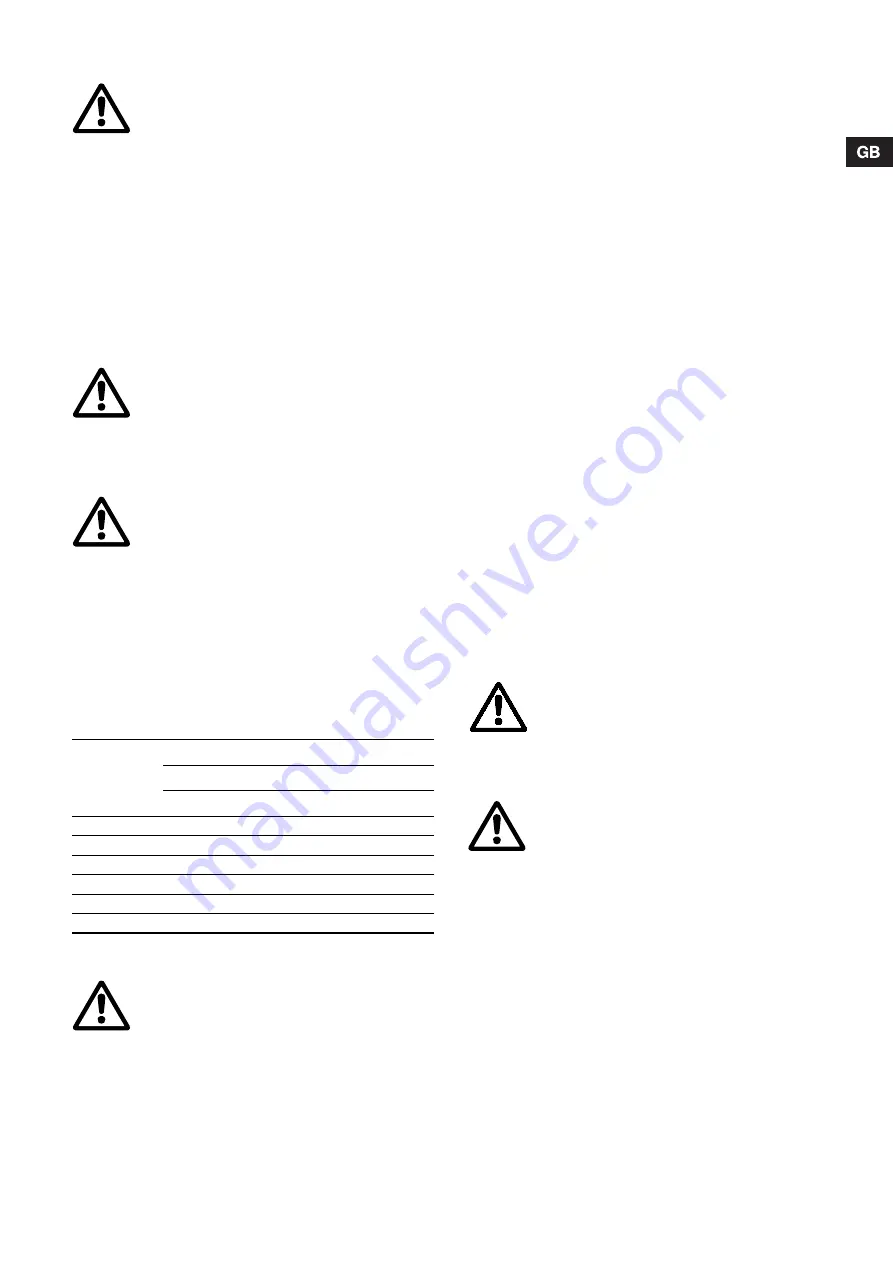
21
9.3 Checking the direction of rotation
The correct direction of rotation is shown by arrows on the pump
housing. Seen from the pump end, the direction of rotation must
be counter-clockwise. See fig. 16.
9.4 Start-up
Before starting the pump, completely open the isolating valve on
the suction side of the pump and leave the isolating valve on the
discharge side almost closed.
Start the pump.
Vent the pump during starting by loosening the air vent screw in
the pump head/cover until a steady stream of liquid runs out of
the vent hole.
When the pipework has been filled with liquid, slowly open the
isolating valve on the discharge side until it is completely open.
Check the overload by measuring the motor current consumption
and comparing the value with the nominal current stated on the
motor nameplate. In case of overload, throttle the valve on the
discharge side until the motor is no longer overloaded.
It is advisable always to measure the motor current consumption
during starting.
Note:
At the moment of start, the input current of the pump motor
is up to six times higher than the full-load current stated on the
motor nameplate.
9.5 Start/stop
10. Maintenance
10.1 Pump
The pump is maintenance-free.
If the pump is to be drained for a long period of inactivity, inject a
few drops of silicone oil on the shaft at the bearing bracket. This
will prevent the shaft seal faces from sticking.
10.2 Mechanical shaft seals
Mechanical shaft seals are maintenance-free, working almost
without any leakages. If any considerable and increasing seep-
age occurs, the mechanical shaft seal should be checked imme-
diately. If the sliding surfaces are damaged, the entire shaft seal
should be replaced. Mechanical shaft seals should be treated
with the greatest care.
10.3 Motor
Check the motor at regular intervals. It is important to keep the
motor clean in order to ensure adequate ventilation. If the pump
is installed in a dusty environment, the pump must he cleaned
and checked regularly.
10.4 Lubrication
Motor bearings
Motors up to and including frame size 160 have maintenance-
free, greased-for-life bearings.
Motors of frame sizes larger than 160 should be greased accord-
ing to the indications on the motor nameplate. Grease spills from
the motor may occur.
Grease specifications: See
.
10.4.1 Bearing grease
Lithium-based grease according to the following specifications
must be used:
•
NLGI class 2 or 3.
•
Viscosity of basic oil: 70 to 150 cSt at +40°C.
•
Temperature range: –30°C to +140°C during continuous oper-
ation.
11. Periods of inactivity and frost protection
Pumps which are not being used during periods of frost should be
drained to avoid damage.
Drain the pump by removing the drain plug. See fig. 16.
Do not tighten the priming plug and replace the drain plug until
the pump is to be used again.
12. Service
If Grundfos is requested to service the pump, Grundfos must be
contacted with details about the pumped liquid, etc. before the
pump is returned for service. Otherwise Grundfos can refuse to
accept the pump for service.
Possible costs of returning the pump are paid by the customer.
12.1 Service kits
Service kits for NB, NBG, see
www.Grundfos.com
(WebCAPS),
WinCAPS or Service Kit Catalogue.
The pump must be filled with liquid when checking
the direction of rotation.
Pay attention to the orientation of the vent hole to
ensure that the escaping water does not cause per-
sonal injury or damage to the motor or other compo-
nents.
In hot-water installations, special attention should be
paid to the risk of personal injury caused by scalding
hot water.
If the motor is fitted with a motor with an output
selected on the basis of a specific maximum flow
rate, the motor may be overloaded if the differential
pressure is lower than anticipated.
Frame size
Maximum number of starts/hour
Number of poles
2
4
6
56 - 71
100
250
350
80 - 100
60
140
160
112 - 132
30
60
80
160 - 180
15
30
50
200 - 225
8
15
30
250 - 315
4
8
12
Before starting work on the pump, switch off the sup-
ply voltage. It must be ensured that it cannot be acci-
dentally switched on.
Pay attention to the escaping liquid which may cause
personal injury or damage to the motor or other com-
ponents.
In hot-water installations, special attention should be
paid to the risk of personal injury caused by scalding
hot water.
If a pump has been used for a liquid which is injuri-
ous to health or toxic, the pump will be classified as
contaminated.
Summary of Contents for NB Series
Page 1: ...NB NBG GRUNDFOS INSTRUCTIONS Installation and operating instructions ...
Page 6: ...6 ...
Page 48: ...484 ...
Page 49: ...485 ...
Page 50: ...486 ...