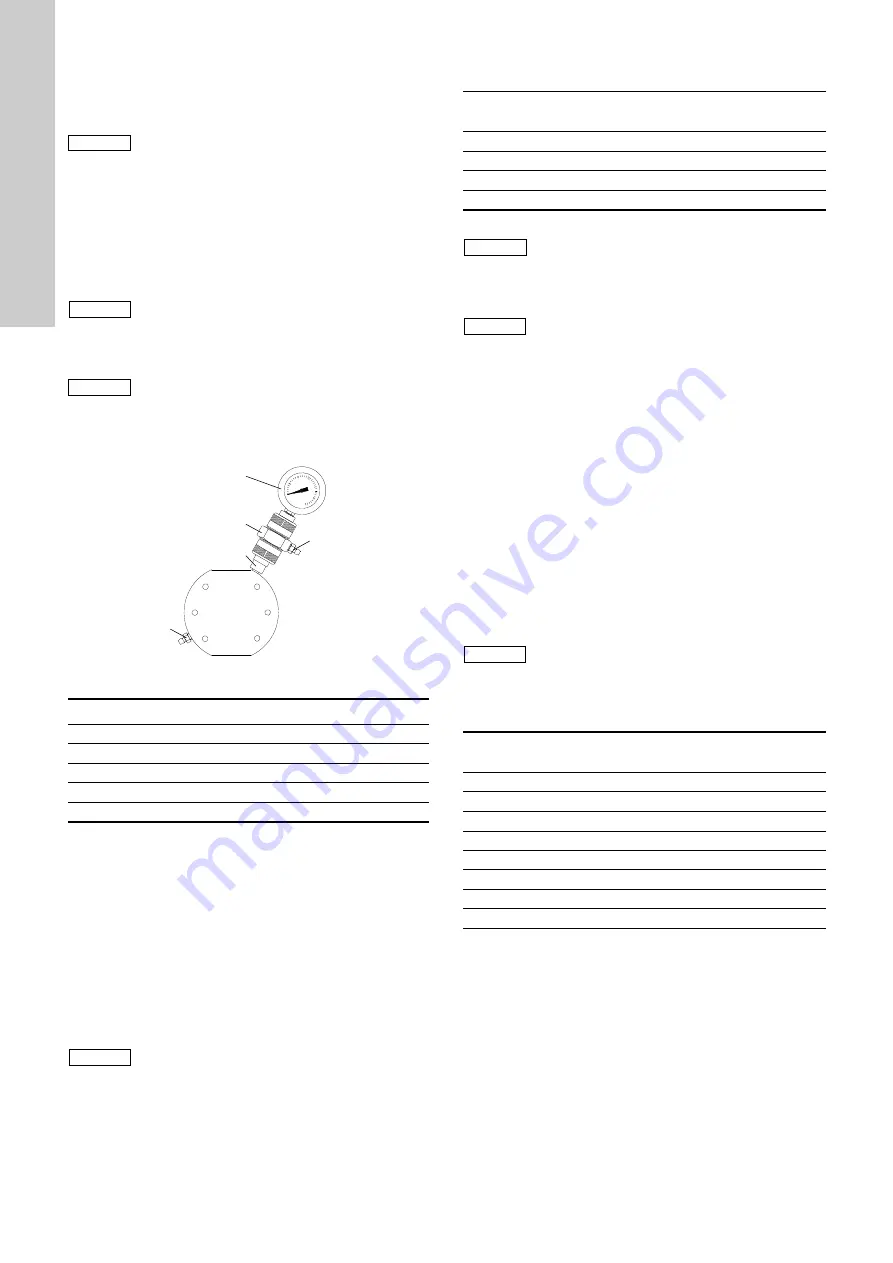
English (GB)
32
10.7.3 Fitting the dosing head
• Fit the dosing head and cross-tighten the dosing head screws
using a torque wrench.
10.7.4 Filling the double diaphragm with separating agent
Pump with double diaphragm: After the diaphragm has been
replaced, refill the separating agent between the diaphragms.
Fig. 41
Dosing head with double diaphragm
1. Set the stroke-length adjustment knob of the pump to 0 %.
2. Open the filling screw (1u) and deaeration screw (2u) by one
turn.
3. Connect the filling hose to the nipple of the filling screw (1u)
and, using the dosing syringe, inject the correct amount of
paraffin oil that is specified in the table below.
4. Close the filling screw (1u), but leave the deaeration screw
(2u) open.
5. Start the pump with a system counter-pressure and
stroke-length setting of 40 %.
6. Only close the deaeration screw (2u) when the separating
agent stops flowing (after 5 to 10 minutes).
Quantity of paraffin oil required for dosing pumps with a
double diaphragm (per dosing head)
10.7.5 Filling with gear oil
1. Check that the locking screw (B) is tightened.
2. Slacken and remove the oil-filling screw (F).
3. Set the stroke-length adjustment knob (L) to "0".
4. Slowly add the hydraulic oil through the oil-filling opening (F)
until the oil reaches the mark on the oil dipstick.
5. Wait 30 minutes.
6. Let the pump run for approx. 5 minutes with a stroke-length
setting of 0 %.
7. Let the pump run for approx. 10 minutes with a stroke-length
setting of 40 %.
10.7.6 Checking the oil level
1. Switch off the pump, check the oil level and add oil, if
necessary.
2. Refit the oil-filling screw (F).
Torques
Caution
The paraffin oil between the diaphragms (Q) is
connected via the clamping sleeves (6q) to the
contact pressure gauge (S) in order to fill and
activate the diaphragm leakage detection. The oil is
able to pass between the diaphragms through the
slits in the clamping sleeves and the slits in the
intermediate disk.
The clamping sleeves (6q) must therefore be
installed in such a way that the slits in the clamping
sleeve face the slits in the intermediate disk (3q).
See fig.
.
Note
See section
for subsequent
start-up!
Caution
After a diaphragm has broken, the ball non-return
valve must be cleaned before the diaphragm is filled
with separating agent. Only clean the ball non-return
valve after a diaphragm breakage!
TM
03 64
67 450
6
Pos.
Components
S
Contact pressure gauge
T
Ball non-return valve
U
Connection piece
1u
Filling screw
2u
Deaeration screw
Note
After a few operating hours, especially if the pressure
of the pressure gauge is increasing, deaerate the
double diaphragm again.
T
U
2u
S
1u
Pump type
Filling quantity
[ml]
DMH 251-253
4
DMH 254
6
DMH 255
8
DMH 257
10
Note
For product numbers of double-diaphragm filling
components, see "Service kit catalogue" on
www.grundfos.com
Caution
Risk of leaking oil and damage caused by oil loss!
For each oil change, a new flat gasket (1b) must be
fitted!
Caution
After initial start-up and after each time the
diaphragm is changed, tighten the dosing head
screws.
After approximately 6-10 operating hours or two
days, cross-tighten the dosing head screws using a
torque wrench.
Pump type
Torque
[Nm]
DMH 251, 10 bar
8-10
DMH 251, 16 bar
10-12
DMH 251, 25 bar
13-15
DMH 252
8-10
DMH 253
10-12
DMH 254
50-54
DMH 255
50-54
DMH 257
50-54