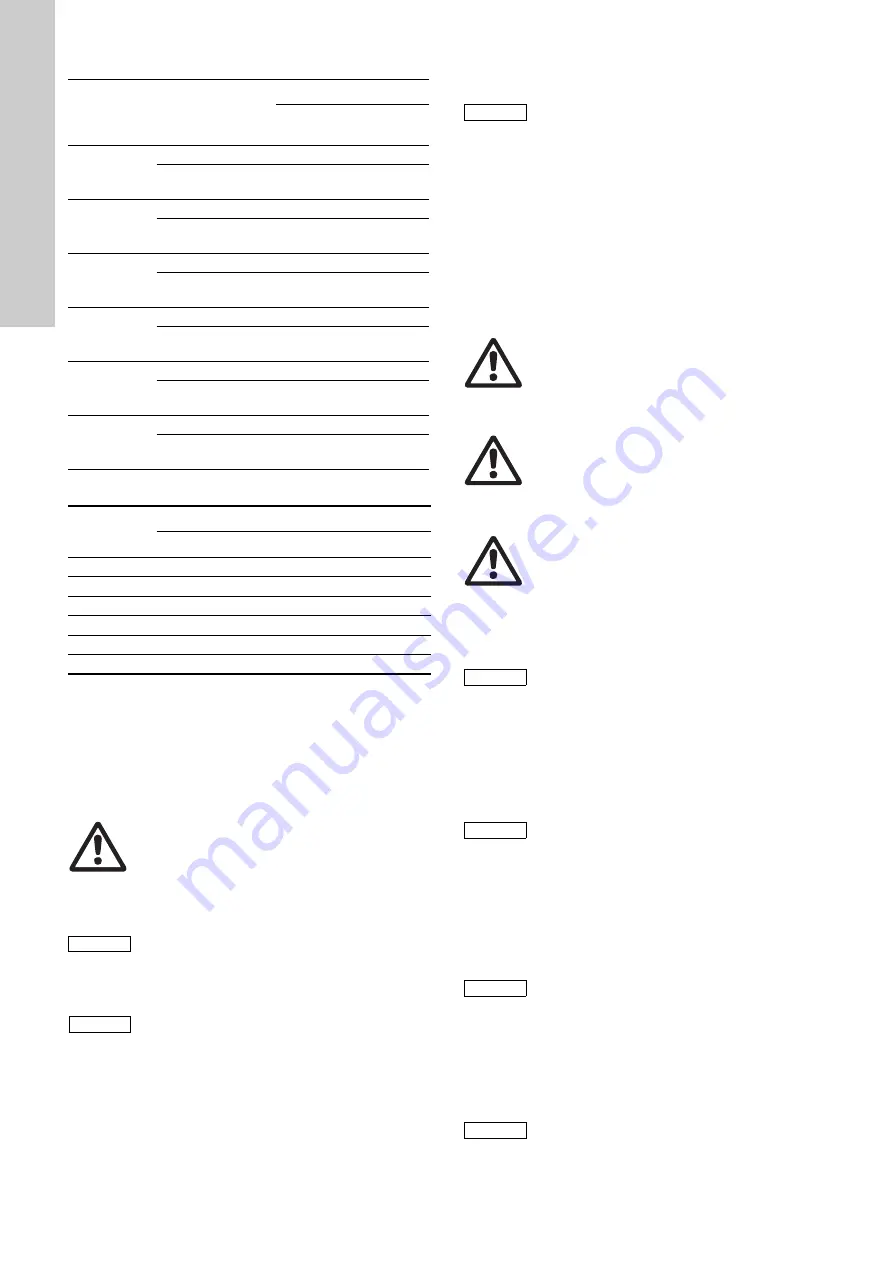
English (GB)
18
5.3 Weight
5.4 Stroke volume
5.5 Materials
Pump housing material
• Pump housing: Al 226.
AR control unit enclosure
• Upper part of enclosure: PPO blend
• Lower part of enclosure: aluminium.
5.6 Data of contact pressure gauge for diaphragm
leakage detection (optional)
The contact pressure gauge has a reed switch with electrically
isolated contact output, maximum switching power 10 W for DC
current or 10 VA for AC current. The maximum switching voltage
is 75 V for DC current or 50 V for AC current, maximum switching
current 0.5 A.
The switching function is set up as an NC contact, i.e. if the
diaphragm breaks, the current circuit is interrupted.
The pressure gauge has a 2-metre cable.
6. Installation
6.1 General information on installation
6.2 Installation location
6.2.1 Space required for operation and maintenance
Maintenance work on the dosing head and the valves must be
carried out regularly.
• Provide sufficient space for removing the dosing head and the
valves.
6.2.2 Permissible ambient influences
See section
3.9 Ambient and operating conditions
6.2.3 Mounting surface
The pump must be mounted on a flat surface.
6.3 Mounting
• Mount the pump on a console or pump foundation using four
screws.
Pump type
Dosing head
material
Weight [kg]
Single
pump
Double
pump
DMH 251
PVC, PP, PVDF
11
13
Stainless steel
1.4571, 2.4610
13
17
DMH 252
PVC, PP, PVDF
11
13
Stainless steel
1.4571, 2.4610
13
17
DMH 253
PVC, PP, PVDF
12
17
Stainless steel
1.4571, 2.4610
14
21
DMH 254
PVC, PP, PVDF
27
32
Stainless steel
1.4571, 2.4610
32
42
DMH 255
PVC, PP, PVDF
55
63
Stainless steel
1.4571, 2.4610
65
83
DMH 257
PVC, PP, PVDF
56
88
Stainless steel
1.4571, 2.4610
68
112
Pump type
Stroke volume [cm
3
]
4 bar
10 bar
16 bar
25 bar
DMH 251
-
3.5
3.1
2.9
DMH 252
-
6.4
6.3
-
DMH 253
-
11.3
-
-
DMH 254
-
31.6
30
-
DMH 255
-
60
-
-
DMH 257
171
131
-
-
Warning
Observe the chemical manufacturer's safety
instructions when handling chemicals!
Make sure that the pump is suitable for the actual
dosing medium!
Caution
The resistance of the parts that come into contact
with the media depends on the media, media
temperature and operating pressure. Ensure that
parts in contact with the media are chemically
resistant to the dosing medium under operating
conditions!
Note
Further information on resistance with regard to the
media, media temperature and operating pressure is
available on request.
Note
Following data is not valid for contact pressure
gauges in explosion-proof version.
Warning
Observe the specifications for the installation
location and range of applications described in
section
.
Warning
Faults, incorrect operation or faults on the pump or
system can, for example, lead to excessive or
insufficient dosing, or the permissible pressure may
be exceeded. Consequential faults or damage must
be evaluated by the operator and appropriate
precautions must be taken to avoid them!
Warning
Risk of hot surfaces!
Pumps with AC motors may become hot.
Allow a minimum space of 100 mm to the fan cover!
Note
A positive pressure difference of at least 2 bar is
required between the suction valve and the
discharge valve in order for the dosing pump to
operate correctly.
If the total counter-pressure (at the dosing point) and
geodetic height difference between the suction valve
and the dosing point is less than 2 bar (20 m WC), a
pressure-loading valve must be installed immediately
before the dosing point.
Note
The pump must be installed in a position where it is
easily accessible during operation and maintenance
work.
Note
The installation site must be under cover!
Do not install outdoors!
Note
The flow must run in the opposite direction to gravity!