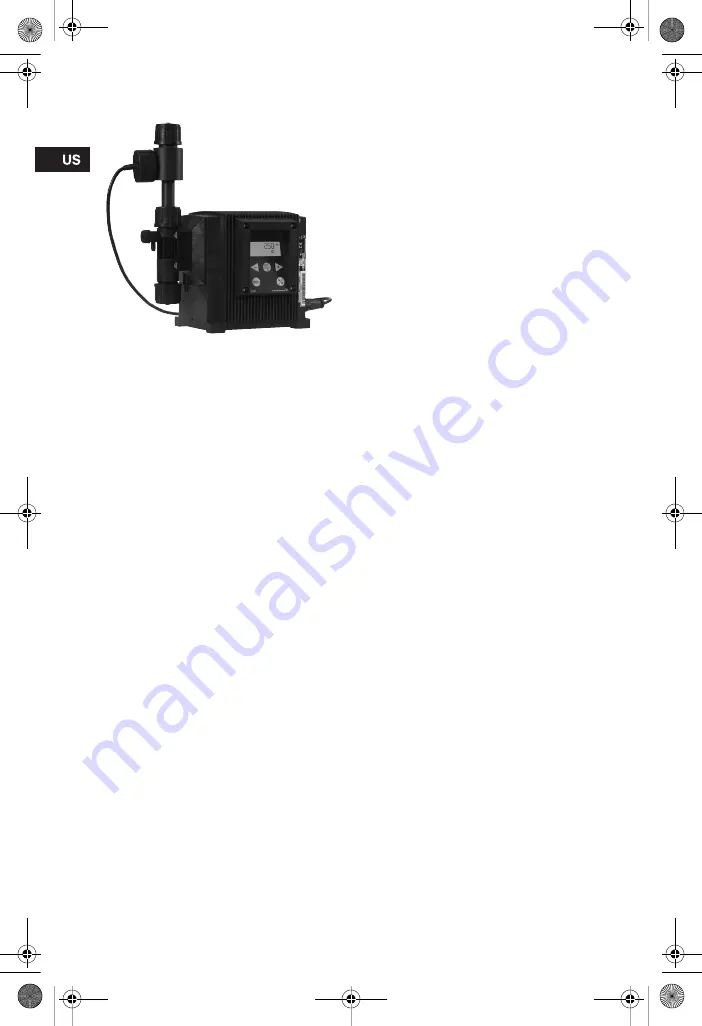
22
4.22 Dosing monitoring
Fig. 23
Dosing monitor mounted on pump
discharge side
The dosing monitor is designed to monitor the dosing
of liquids which may cause gas accumulation in the
dosing head, thus stopping the dosing process even
if the pump is still operating.
During the dosing process, the dosing monitor gives
pulse signals to the monitor input so that the pump
can compare performed dosing strokes (from internal
stroke sensor) with externally measured physical
strokes (from the dosing monitor). If an external dos-
ing stroke is not measured as a result of the internal
dosing stroke, this is considered a fault that may
have been provoked by empty tank or gas in the dos-
ing head.
DME 2 to 48:
The dosing monitor should be con-
nected to the level input. This input must be config-
ured for dosing monitoring. Consequently, it cannot
be used as a level input.
Once the input has been set to dosing monitoring
and a dosing monitor has been connected and set,
the dosing monitoring function will be active.
Definitions
Correct dosing stroke:
A pulse from the dosing
monitor corresponds to the internal stroke signal
within acceptable time.
Incorrect dosing stroke:
There is no pulse from the
dosing monitor corresponding to the internal stroke
signal within the acceptable time (the pump is not
pumping).
Logic
If a number of incorrect dosing strokes are per-
formed, the pump will continue operating, but it will
change over to alarm mode. The red indicator light
will be on and the alarm output, if any, will be acti-
vated (variant AR).
When a correct dosing stroke is detected, the red
indicator light is turned off and the alarm output, if
any, is deactivated.
Gr
A1
03
1
Grundfos.bk Page 22 Wednesday, May 21, 2008 11:21 AM