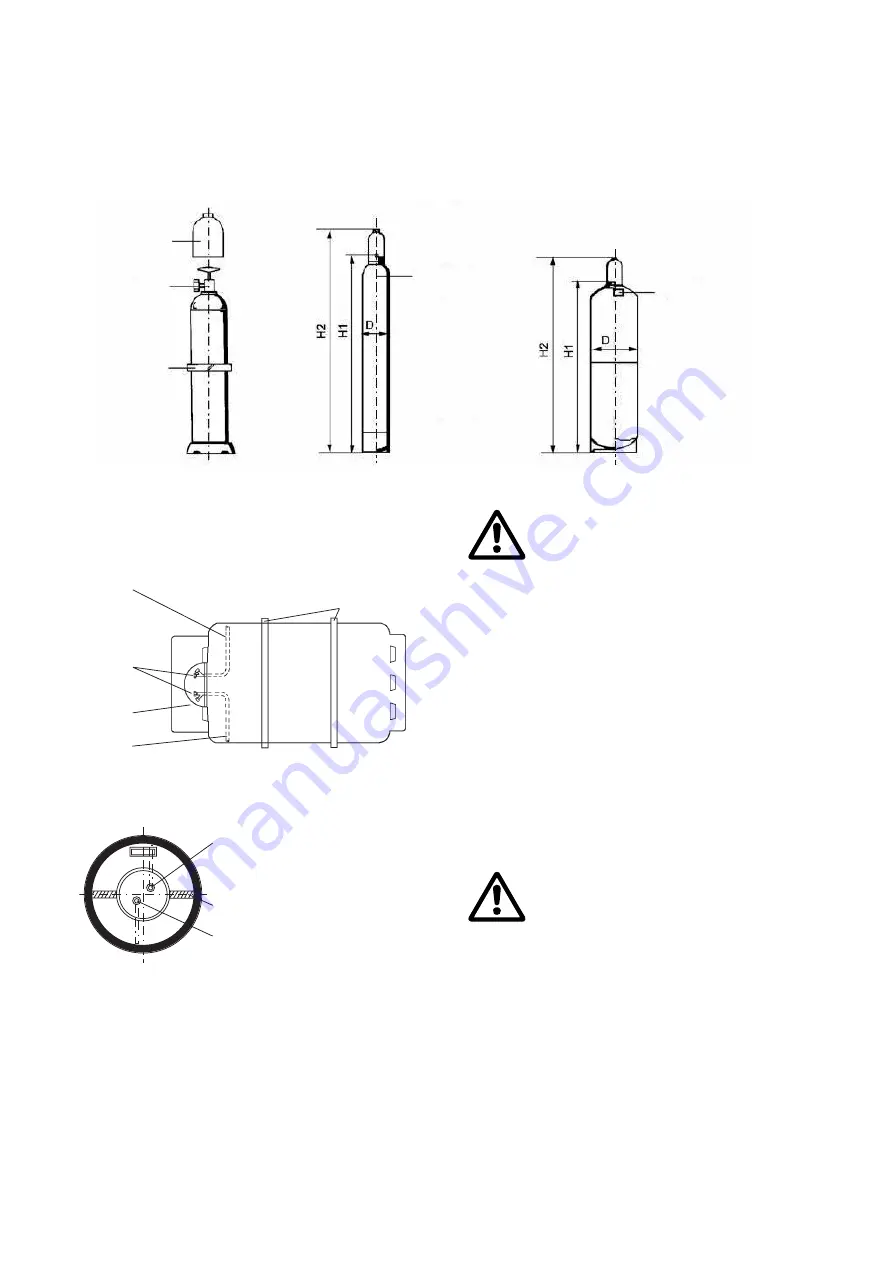
7
2.2.6 Pressure vessels and mountings
Chlorine is being offered in two container designs:
•
Steel cylinders containing 50 kg or 65 kg, equipped with one
valve for
– the withdrawal of gaseous chlorine from the upright
standing cylinder
Variant of chlorine cylinder
Fig. 3
Variant of chlorine cylinder
•
Steel drums containing 500 kg or 1000 kg, equipped with
– one valve for the withdrawal of gaseous chlorine
– one valve for the withdrawal of liquid chlorine
Fig. 4
Chlorine drum
Fig. 5
Valve position of chlorine drum
Due to safety precautions, chlorine containers are only filled up to
95 % of their capacity.
•
Kind of gas, weight, owner, producing date and date of the
last testing have to be noted clearly on the container. Chlorine
containers are marked by grey colour.
•
No changes or repair by the user!
•
Never open container valves by force. Stuck valve spindels
can be loosened by wrapping a shred with warm water
around the valve.
– Never use an open flame!
– Never use wrench lengthening!
– Return containers with stuck valves to the manufacturer.
•
Observer safety precautions and the manuals of the
manufacturer!
2.2.7 Chlorine extraction
Before the extraction
•
The chlorine containers must be stored at least for 8 hours in
the container room so that the content can adapt the ambient
temperature.
•
Turn chlorine drums on the support until the dip pipe and the
riser pipe are placed vertically (observe the markings on the
drum).
•
Check tightness.
Connection
•
Protect containers from turning over or rolling away!
•
Dry the piping and the withdrawal system with dry nitrogen or
dry air.
•
No foreign matter must get into the plant.
•
Mount new gaskets to the connection line.
•
Connect the container.
•
Slowly open the container valve.
T
M
04
06
9
3
09
0
8
Protecting cap
Valve
Holding clip
Valve thread acc.
to DIN 477
Labelled by
stamping
Weldless chlorine
cylinder
Aluminium
label
Welded chlorine
cylinder
TM
04
06
94
09
08
TM
04
0
695
09
08
Tyre of roller
Riser pipe (for the withdrawal of gaseous chlorine)
Protecting cap
Valves
dip pipe
(for the withdrawal of liquid chlorine)
Valve for gaseous chlorine
Colour
Valve for liquid chlorine
Warning
Observe safety precautions for chlorine
containers
Warning
Chlorine containers must never have a higher
temperature than other parts of the plant. Danger
of liquefaction and possible chlorine break-out!