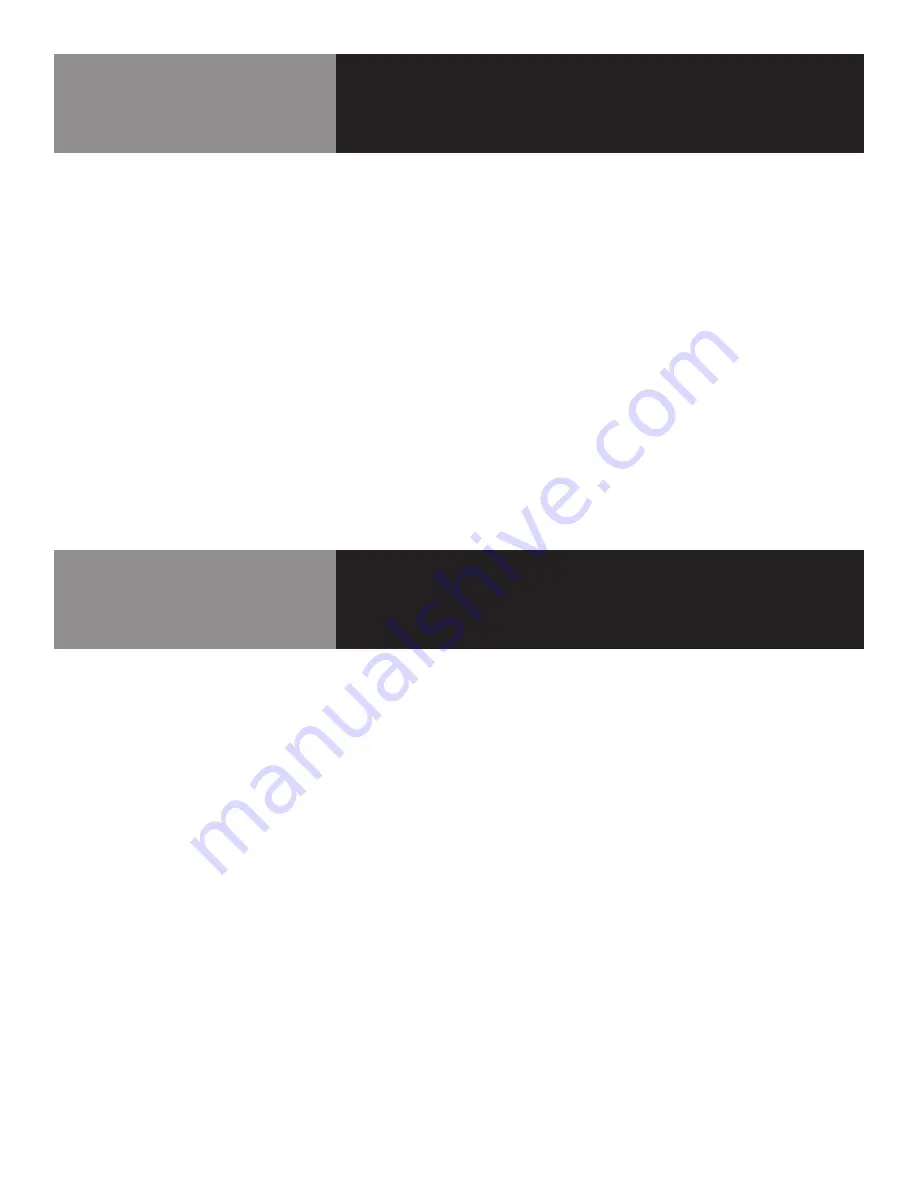
OM-TDH/TDHC 13
Sequence of Operation
The following “action-reaction” outline is provided to help understand how the kettle works.
1.
When the power switch is turned on, it starts the spark igniter and opens the automatic valve for the pilot burner. The spark
ignites a pilot flame, which heats the sensor. The sensor then sends a signal to turn off the spark. The flame thereafter acts as
a standing pilot until the power is turned off.
2.
If the pilot flame is not sensed within 90 seconds after spark begins, a timer shuts down the entire operation. To attempt a
second trial for ignition, turn off the power switch. Check the gas supply valves and wait five minutes before trying again
by switching power on. If you cannot establish a pilot flame in four tries, close all valves, turn off the power, and contact an
authorized Service Agency.
3.
When the operator sets a temperature on the controller, it causes the automatic valve to admit gas to the main burner, where
it is ignited by the pilot flame. When the kettle reaches the set temperature, the relay switch opens. This stops the signal to
the gas control valve and shuts off gas to the main burner. The pilot flame remains lit. When the kettle cools below the set
temperature, the relay switch closes and starts another cycle. On and off cycling continues and maintains the kettle at the
desired temperature. This action is indicated by the Heat indicator light.
The kettle has the following safety features in addition to the 90-second ignition timer:
1.
Low water cutoff relay that will shut off gas supplies to all burners until the jacket water level is corrected.
2.
High limit pressure switch, set to open at about 43 PSI and to shut down the burners until jacket pressure is decreased.
3.
Pop safety valve, which will release steam if jacket pressure exceeds 50 PSI.
4.
Tilt switch, which shuts off all burners when the kettle is tilted.
5.
Gas pressure regulator built into the gas control valve.
Operation
2)
Load basket on a level, stable work surface.
3)
Lift the loaded basket with both hands. Get help from
another person if the basket is too heavy for safe handling.
Then slowly lower product into kettle.
4)
When removing basket with cooked product, lift basket
straight up, ensuring bottom of basket clears the rim and
pouring lip of the kettle. Wear protective oven mitts and
protective apron.
5)
Allow hot water to fully drain from product, before moving
basket away from the kettle. Do not rest kettle basket on
kettle rim or pouring lip. If basket is too heavy for individual
to lift and safely move, get help from another person.
Remove product immediately from basket into another
container, being sure to avoid contact with hot product and
hot basket or place basket with food on stable, flat surface,
setting it inside a solid steamer or bake pan, to catch any
remaining hot water draining from product.
Summary of Contents for TDB 48A
Page 31: ...OM TDH TDHC 31 Wiring Diagram For Classic Control Models ...
Page 32: ...32 OM TDH TDHC Wiring Diagram For Advanced Control Models ...
Page 34: ...34 OM TDH TDHC ...
Page 35: ...OM TDH TDHC 35 ...
Page 36: ...36 OM TDH TDHC ...