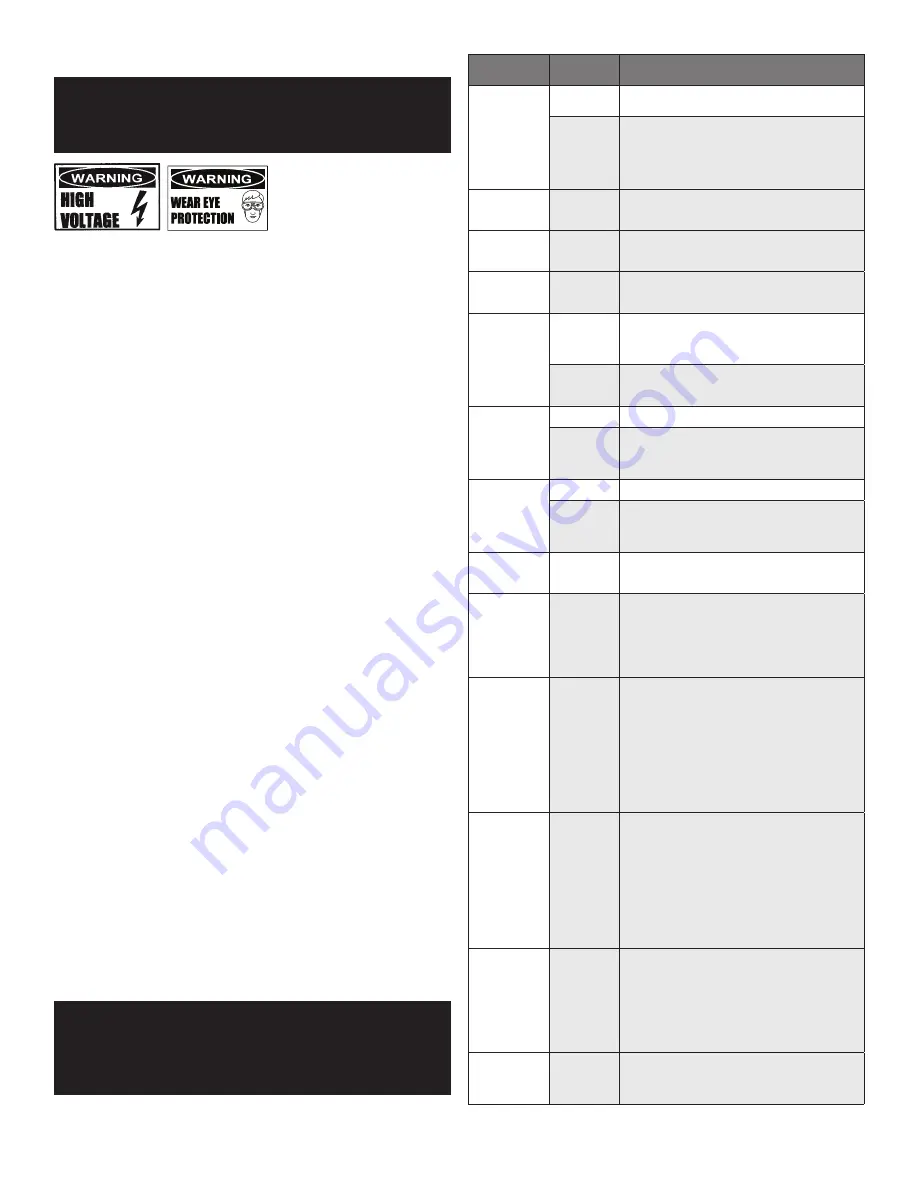
8
OM-BPM-15/30/40G(C,A) (CE) INTERNATIONAL
MAINTENANCE
WARNING: ELECTRIC POWER ALWAYS SHOULD BE SHUT OFF BEFORE WORK IS DONE
ON INTERNAL COMPONENTS.
WARNING: DISCONNECT ELECTRICAL POWER FROM THE UNIT BEFORE ATTEMPTING
TO GREASE THE TRUNNION BEARINGS.
Your braising pan is designed to require minimum maintenance, but certain parts
may need replacement after prolonged use. After installation, no user adjustment
should be necessary. If a service need arises, only authorized personnel should
perform the work.
Service personnel should check the unit at least once a year. This periodic
maintenance should include inspecting electrical wires and connections, cleaning
the inside of the control console, and possible adjustment of the pilot light. (Units
with standing pilot ignition only) At least twice a year, grease the two trunnion
bearings and worm gear.
We recommend the use of number two grade LGI lithium grease. Add grease
through the zerk fittings on the gear hosing until grease flows out of the bearings
around trunnion shaft. Also, add grease in the gear to cover arc that is in contact
with the worm gear. Clean up excess grease.
A Service Log is provided with the warranty information at the back of this manual.
Each time service is performed on your equipment, enter the date on which
the work was done, what was done, and who did it. Keep the manual with the
equipment for quick and easy reference.
SAFETY PRECAUTIONS
A stop-cock will be fitted in the gas pipe supplying the appliance. The user must
be familiar with its location and operation, and able to turn it off in an emergency.
If there is a smell of gas, immediately turn off the gas, ventilate the area, and call
the gas supplier.
NEVER USE NAKED FLAME TO SEARCH FOR GAS LEAKS.
REPLACEMENT PARTS
To order parts, contact your Authorized Service Agent. Supply the model
designation, serial number, part description, part number, quantity, and when
applicable, voltage and phase.
CONTACT US
If you have questions pertaining to the content in this manual, contact Unified
Brands at 888-994-7636.
TROUBLESHOOTING
This unit is designed to operate smoothly and efficiently if properly maintained.
However, the following is a list of checks to make in the event of a problem.
Wiring diagrams are found at the end of this manual. When in doubt, turn unit
off and call for service at 888-994-7636. If an item on the check list is marked
with (*), it means that the work should be done by a Authorized Service Agent.
WARNING: ELECTRICAL POWER MUST BE SHUT OFF BEFORE WORK IS DONE ON INTERNAL
COMPONENTS. USE OF ANY REPLACEMENT PARTS OTHER THAN THOSE
SUPPLIED BY THE MANUFACTURER OR THEIR AUTHORIZED DISTRIBUTOR
CAN CAUSE INJURY TO THE OPERATOR AND DAMAGE TO THE EQUIPMENT
AND WILL VOID ALL WARRANTIES. SERVICE PERFORMED BY OTHER THAN
FACTORY-AUTHORIZED PERSONNEL WILL VOID ALL WARRANTIES.
SYMPTOM
WHO
WHAT TO CHECK (X indicates work that should only be
performed by a qualified service representative)
Display not lit
(Advanced only)
User
a.
That power supply is on.
Authorized
Service Rep
Only
b. Fuses, accessible by removing caps on the side of the
control box.
c. For loose or broken wires or damaged RTD probe. X
d. Temperature controller functioning, by listening for a click
when the switch opens or closes and verifying LEDs on back
of board. X
PROB in display
(Advanced only)
Authorized
Service Rep
Only
a. For loose or broken wires or damaged/failed RTD probe. X
b. PCB board malfunction/failure
HI in display
(Advanced only)
Authorized
Service Rep
Only
a. For loose or broken wires or damaged/failed RTD probe. X
b. PCB board malfunction/failure
Pan is hard to tilt
Authorized
Service Rep
Only
a. Gears or foreign materials, lubrication, and alignment. X
b. Broken tilt or worm gears. X
Burners will not
light
User
a. That the main gas supply valve is open (handle is in line with
the gas pipe)
b. Gas supply to the braising pan is at specified pressure.
c. That the pan body is horizontal.
Authorized
Service Rep
Only
d. Temperature controller operation. The contacts should click
when the dial is rotated to settings above and below the
temperature of the pan. X
Pan continues
to heat
after it reaches
desired
temperature
User
a. Temperature controller dial setting and display.
Authorized
Service Rep
Only
b. Temperature controller calibration and offsets. X
c. Temperature controller operation. The thermostat should
click when the dial is rotated to settings above and below
the temperature of the pan. X
Pan stops heating
before reaching
desired
temperature
User
a. Temperature controller dial setting and display.
Authorized
Service Rep
Only
b. Temperature controller calibration and offsets. X
c. Temperature controller operation. The contacts should click
when the dial is rotated to settings above and below the
temperature of the pan. X
Pan heats
unevenly
User
a. That the pan body is horizontal.
b. That the pan is preheated properly in accordance with the
instructions in the Operation section of this manual.
System does not
produce a spark
Authorized
Service Rep
Only
a. Controller and ensure that it is energized X
b. AC voltage between terminals on secondary side of
transformer. If it is not 24 Volt, replace the transformer X
c. That the high tension cable is in good condition. If cracked or
brittle, replace.
X
d. Pilot electric ceramic for crack or break. X
e. Pilot spark gap. Regap. X
Spark is present
but the pilot will
not light
Authorized
Service Rep
Only
a. That the pilot valve is securely connected to terminals. X
b. For 24 VAC at terminals PV and to ground.
If
24V is not present, replace the ignition control module. X
c. That gas pressure is at least 3.5” W.C.(8.7millibars). X
d. For gas at the pilot. If it is not flowing:
(1) Check the pilot gas line for kinks and obstructions. X
(2) Clean orifice, if necessary. X
(3) Check solenoid operation pilot valve on gas valve.
Repair or replace as necessary. X
e. That the pilot spark gap is located in the pilot gas stream. If
not, adjust or replace the pilot burner. X
f. For drafts. Shield the pilot burner, if necessary. X
Pilot lights, but
main burner will
not come on and
spark does not
stay on
Authorized
Service Rep
Only
a. Check controller to see that it is closed at temperature
setting higher than that of the current pan temperature.
X
b. For 24 V between terminals MV and to ground.
If
24V is not present, replace the ignition control module.
X
c. That gas pressure is at least 3.5” W.C.(8.7millibars). X
d.
Electrical connections of the main valve to terminals, to
assure that they are securely attached. Check solenoid
operation for main valve on gas valve. Repair or replace
as necessary. X
e. That secondary thermostat switch is closed.X
Pilot lights, but
main burner will
not come on, the
spark stays on
Authorized
Service Rep
Only
a. Check for improper grounding.
If necessary,
repair with high temperature wire. X
b. Pilot burner ceramic insulator for cracks. X
c. That high tension cable is not grounded out. If it is,
correct the ground-out condition or the pilot burner. X
d. For proper gas pressure. X
e. Clean pilot assembly, or replace if necessary. X
f. Tighten all mechanical and electrical connections. X
g. Replace ignition control module.
X
Main burner
comes on but will
not stay on.
Authorized
Service Rep
Only
a. Check burner ground for bad wire or connection.
Replace if necessary with high temperature wire. X
b. Check for low gas supply pressure. If necessary, replace
ignition control module. X