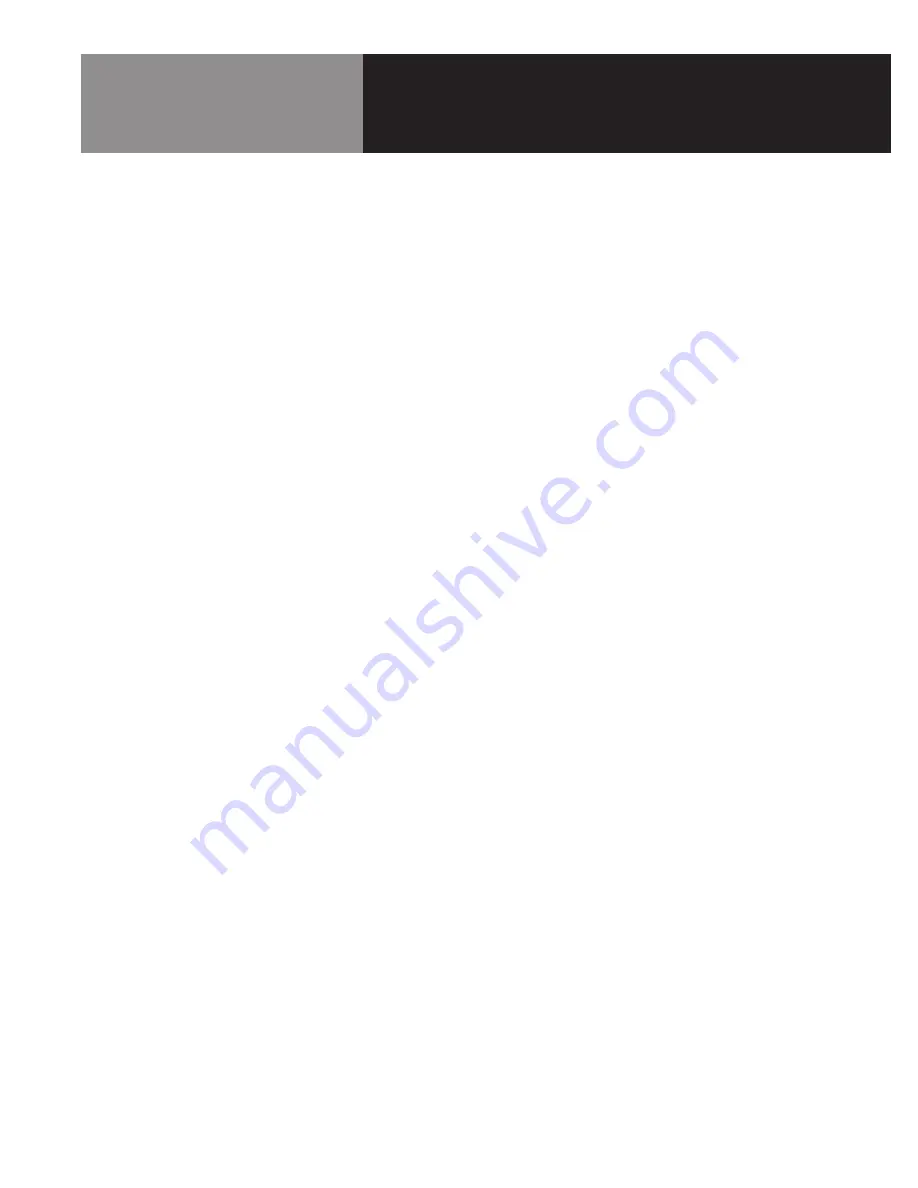
OM-AH/1 9
11. Installation must conform with local codes, or in the absence of local codes, with
the National Fuel Gas Code, ANSI Z 223.1-1988 (or latest edition). The unit should
be installed in an adequately ventilated room with a provision for adequate air
supply. The best ventilation will utilize a vent hood and exhaust fan with no direct
connection between the vent duct and the flue. Do NOT obstruct the flue or vent
duct after installation.
In Canada, the installation must conform to the CAN/CGA B149 Installation Codes
for Gas Burning Appliances and Equipment and/or local codes.
12. Adequate space for proper service and operation is required. No NOT block any
air intake spacings to the combustion chamber or obstruct the air flow by piling or
stacking anything near the kettle.
13. After the kettle has been connected to the gas supply, all gas line joints must be
checked for leaks. DO NOT USE A FLAME TO CHECK FOR LEAKS. A thick soap
solution or other suitable leak detector should be employed.
14. For a unit on casters, complete connection to the gas supply with connectors that
comply with the standard for connectors for moveable gas appliances, ANSI Z21.69
- latest edition. Restrain movement of the unit by attaching a cable or chain to the
eyelet (provided at the back of the frame) and anchoring the cable or chain to the
wall or floor. Make the length and location of the cable such that the unit cannot
pull on the gas connection while the cable is connected.
15. The appliance and its individual shutoff valve must be disconnected from the gas
supply piping system during any pressure testing of that system at test pressures
in excess of 1/2 PSIG (3.48 kPa). The appliance must be isolated from the gas
supply piping system by closing its individual manual shutoff valve during any
pressure testing of the gas supply piping system at test pressures equal to or less
than 1/2 PSIG (3.48 kPa).
16. Check the following points to confirm that your kettle has been installed properly.
Any mechanical, electrical, or gas type change must be approved by the Food
Service Engineering Department.
a.
Enough room between the kettle and nearby objects for cleaning and service.
b.
Minimum clearance of 6 inches from sides and 6 inches from draft diverter.
c.
Unit vented to a hood or chimney (not attached to a vent).
d.
Kettle level.
e.
Correct amount of water in the jacket.
f.
Pressure relief safety valve outlet pointed down.
g.
Connected with a waterproof, 115 volt, 15 AMP supply of electric power in
accordance with electrical codes.
h.
Gas lines cleaned before connection.
i.
Gas connected with 3/4 inch pipe or equivalent.
j.
Gas line joints checked for leaks.
k.
No obstruction to air supply or venting.
Installation