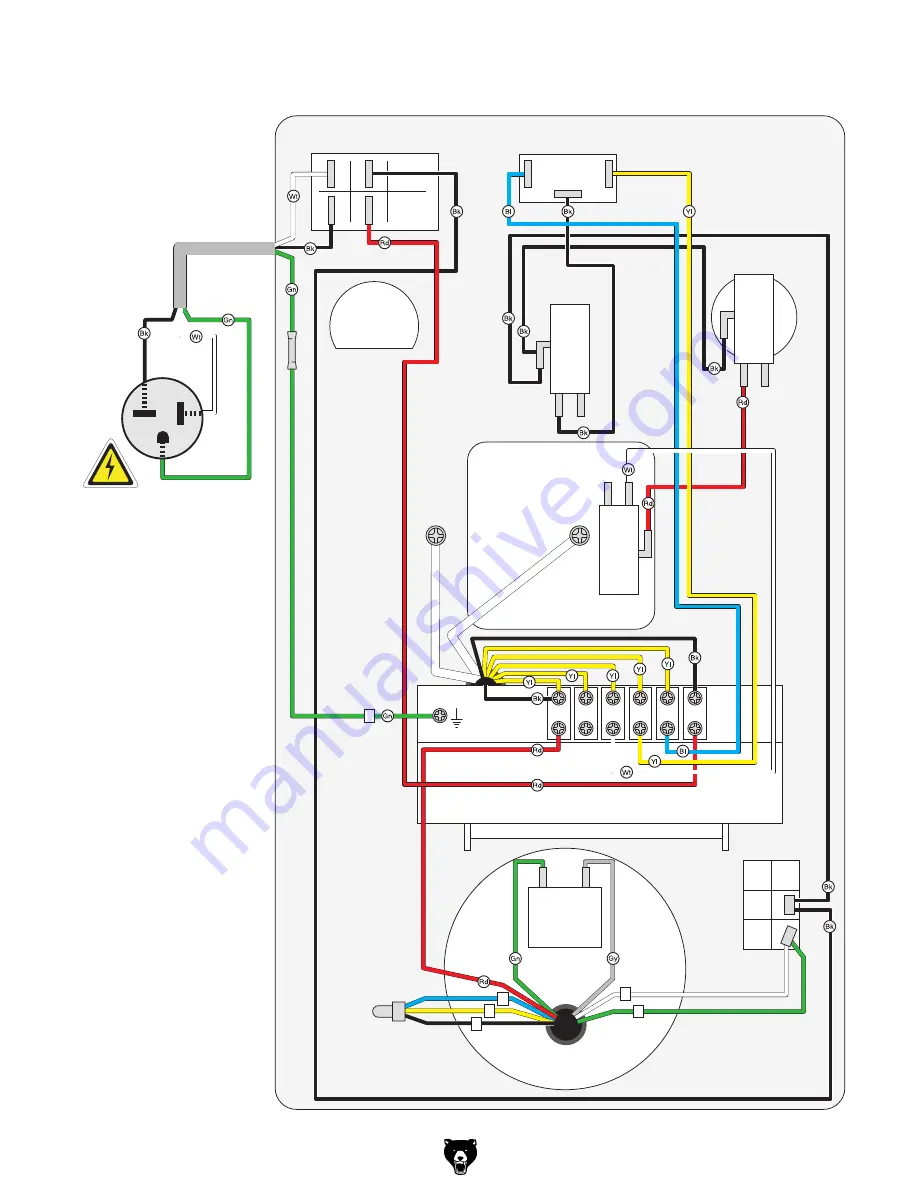
-14-
t10499/t10500 Blade Welder
T10500 Wiring Diagram
Clamp
Pressure
Cam
230VAC
NEMA 6-20 Plug/Receptacle
(As Recommended)
Transformer
A174-0023 4.2KVA 240V
1
2
3
4
5
6
Anneal
Button
Anneal
Strength Switch
Main
Power Switch
Welding
Button
Grinder ON/OFF
Switch
CS R1328F
ON
OFF
230V
Grinder
Motor
Ground
Ground
HY29G
20/15A 277V
Welding
Unit
Run
Capacitor
2M 250V
COM
NO NC
Defond
ENEC
T120/55
COM
NO NC
Defond
COM
NO
NC
Defond
E
5
4
6
3
2
Hot
Hot
G