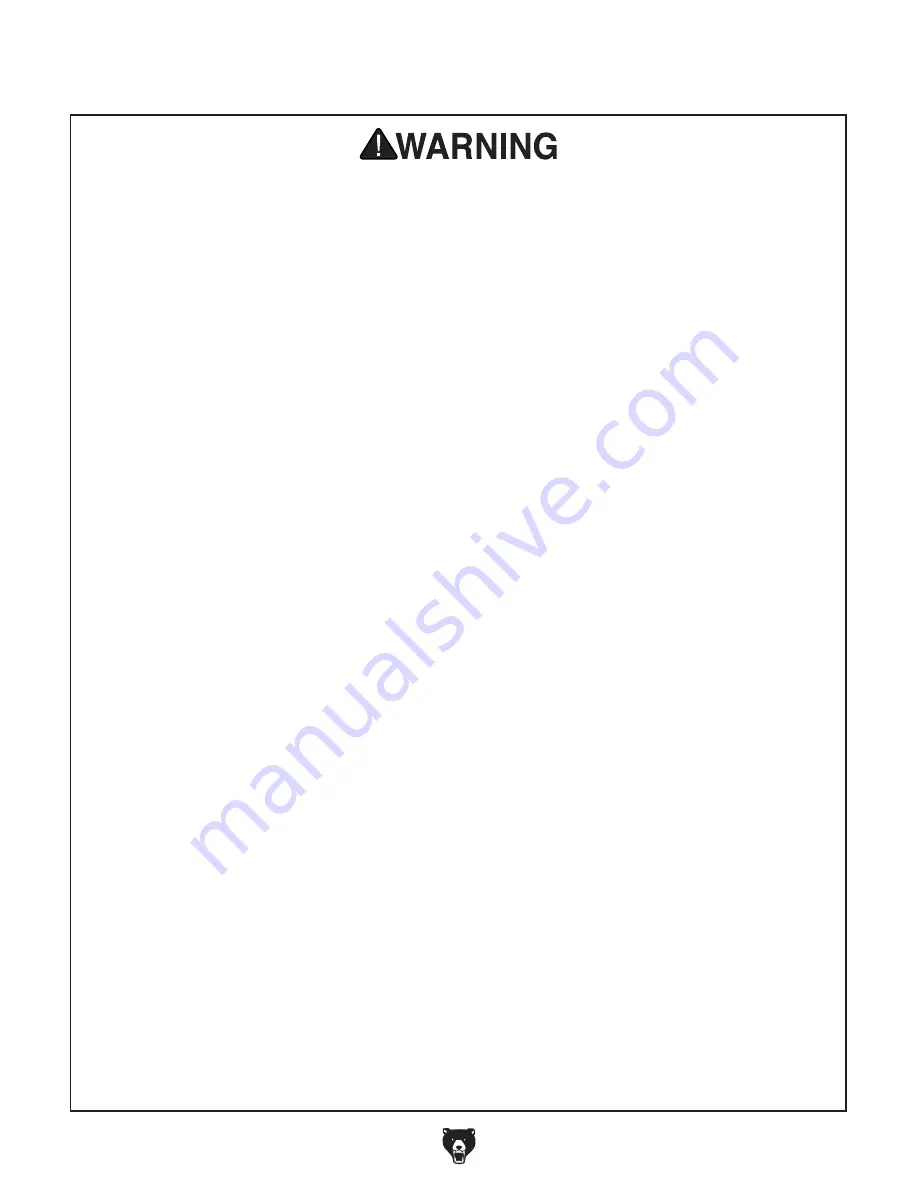
-10-
Model T32335 (Mfd. Since 11/20)
Additional Safety for Air Compressors
Serious impact injury or death can occur from bursting tank, attachment tool, distribution
line, or hose. Contact with hot compressor parts can result in burns. Operating this tool in an
environment without proper ventilation or near combustible materials can lead to explosions
or fires. Eyes and other soft tissues can be easily injured by air streams and debris projected
by compressed air or attachment tools. To reduce the risk of these hazards, operator and
bystanders MUST completely heed hazards and warnings below.
DAILY MAINTENANCE. Test safety relief valve
daily to dislodge any blockages and confirm it is
working correctly. Drain moisture from tank daily to
prevent internal corrosion that could weaken tank.
DISTRIBUTION LINES. Use only stainless steel,
copper, or aluminum for air delivery/distribution
lines. NEVER use PVC because it cannot with-
stand the pressure, heat, condensation, and oils of
compressed air and may shatter, creating danger-
ous shrapnel.
VENTILATION. Only operate in well-ventilated
environment that is less than 100
°
F and keep com-
pressor at least 18 inches from nearest wall. DO
NOT obstruct airflow to air filters and ventilation
openings. Regularly check and change air filters to
avoid buildup of impurities and reduce risk of fire.
COMBUSTION. Compressor motor, pressure
switch, and some pneumatic attachment tools
often produce sparks. Only operate compressor
in area free of combustible materials to prevent
fires and explosions. When spraying, locate air
compressor at least 20 feet from spray area, do
not smoke, and do not spray flammable mate-
rial in confined area near flame/compressor. Turn
compressor
OFF when unattended. Motor could
overheat and create fire hazard.
HOT PARTS. Discharge line and other compres-
sor pump parts heat up during operation. Do not
touch these parts during or immediately following
operation to prevent burns.
MOVING AND SERVICING. Disconnect power,
allow compressor to cool, bleed air from system,
and disconnect attachment tools and hoses before
moving or servicing to prevent impact injuries, soft
tissue injuries, and burns.
TANK INTEGRITY. Inspect tank, attachment
tools, pump, air lines, and valves for rust, damage,
weakness, leaks, looseness, or excessive wear
and repair/replace damaged components before
operating. Replace a damaged tank immediately.
DO NOT attempt to weld on, modify, or repair tank.
Modifying tank can affect tank integrity and cause
tank to burst.
ATTACHMENT TOOLS. Always wear ANSI-
approved eye protection and any additional per-
sonal protective equipment required by attach-
ment tools. Pneumatic tools can propel objects
and debris at high speeds or even explode. Never
use damaged tools—they are even more likely to
rupture. DO NOT exceed pressure ratings of tools
or attachments as lines and seals may burst. Use
proper air hose for tool and confirm air hose is
long enough to reach work area without stretching.
Do not carry attachment tool with hand on trigger
to reduce risk of accidental firing. Always relieve
outlet air line and hose before attaching/removing
tools. Disconnect hose or tool from compressor
when not in use.
MODIFICATIONS. DO NOT adjust or remove
safety relief valve, pressure switch, or otherwise
modify machine. Do not install shut-off valve
between compressor pump and tank. Check, safe-
ty, and pressure valves are adjusted at factory for
correct tolerances and abilities of compressor and
are designed to keep tank and other components
from bursting.
INTENDED USE. DO NOT use compressed air
as breathable air supply and DO NOT aim com-
pressed air or air tools at body parts or people.
Compressed air can injure or propel debris into
eyes or other soft tissues. Do not use compres-
sor to inflate low-pressure objects that are likely to
burst (like children’s toys).
Summary of Contents for QUIET Series
Page 40: ......