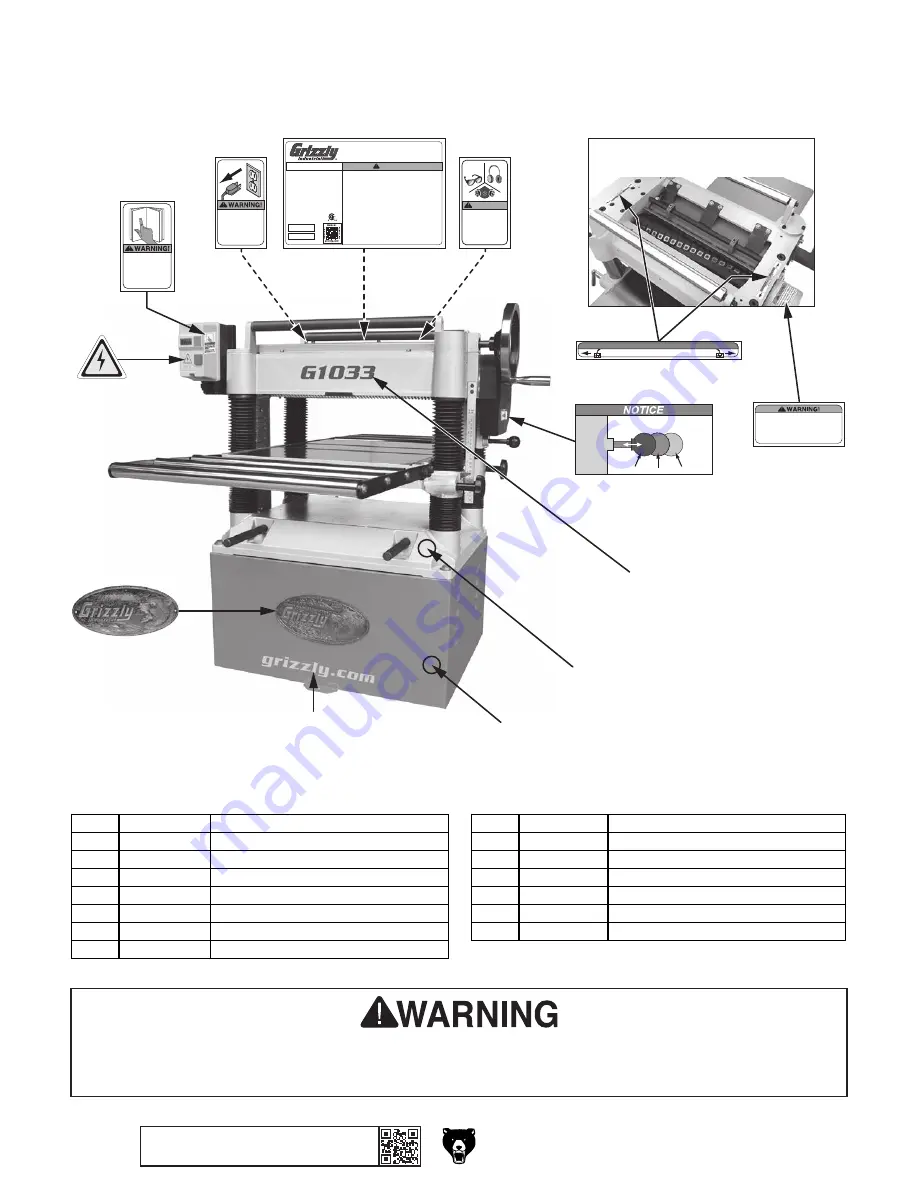
-62-
Model G1033/X/Z (Mfd. Since 02/19)
BUY PARTS ONLINE AT GRIZZLY.COM!
Scan QR code to visit our Parts Store.
G1033/G1033Z Labels & Cosmetics
Safety labels help reduce the risk of serious injury caused by machine hazards. If any label comes
off or becomes unreadable, the owner of this machine MUST replace it in the original location
before resuming operations. For replacements, contact (800) 523-4777 or www.grizzly.com.
grizzly.com
G1033
G1033Z
Only shift gearbox when
planer is running.
Neutral
28 FPM
16 FPM
709
703
700V3
704
705
701
702
706
707V2
708
711
712
710
WARNING!
EYE/EAR/LUNG
INJURY HAZARD!
Always wear safety
glasses, ear protection,
and respirator when
using this machine.
INJURY/SHOCK
HAZARD!
Disconnect power
before adjustments,
maintenance, or
service.
MODEL G1033
20" SPIRAL CUTTERHEAD PLANER
Motor: 3 HP, 230V, 1-Ph, 60 Hz
Full-Load Current Rating: 18A
Cutterhead: 4 Spirals, 52 Inserts
Cutterhead Speed: 5000 RPM
Feed Rates: 16 & 20 FPM
Maximum Depth of Cut: 1/8"
Minimum Stock Thickness: 3/16"
Minimum Stock Length: 6"
Maximum Cutting Width: 15"
Maximum Cutting Height: 6"
Weight: 520 lbs.
Specifications
WARNING!
Date
Mfd. for Grizzly in Taiwan
S/N
To reduce the risk of serious injury when using this machine:
1. Read and understand owner’s manual before operating.
2. Always wear approved safety glasses and respirator.
3. Disconnect power before doing any service on machine.
4. Only plug power cord into a grounded outlet.
5. Do not wear loose clothing, gloves, jewelry, or other
items that can get entangled.
6. Do not plane two boards of varying thickness at the same
time.
7. Never plane material smaller than 6" long or
3
/
16
" thick.
8. Keep fingers clear of pinch point between stock and
table.
9. Stand clear of board ends during cutting operation.
10. Inserts are sharp! Use extreme caution when servicing.
11. Never reach into cutting area while machine is running.
12. Do not expose to rain or use in wet locations.
13. Prevent unauthorized use by children or untrained users.
175370
To reduce risk of death
or serious injury, read
manual BEFORE using
machine.
To get a new manual, call
(800) 523-4777 or go to
www.grizzly.com.
Note: Similar model headstock
shown as example.
Add SAE 30 oil every 24 hours of operation.
NOTICE
INJURY HAZARD!
To reduce the risk of serious personal
injury, do not remove this cover while the
machine is running or connected to power.
Always disconnect power before servicing.
REF
PART #
DESCRIPTION
REF
PART #
DESCRIPTION
700V3 P1033700V3
MACHINE ID LABEL V3.02.19 (G1033)
707V2 P1033707V2
SHIFT GEARBOX NOTICE V2.02.19
700V3 P1033Z700V3 MACHINE ID LABEL V3.02.19 (G1033Z)
708
P1033708
MODEL NUMBER LABEL (G1033)
701
P1033701
READ MANUAL LABEL
708
P1033Z708
MODEL NUMBER LABEL (G1033Z)
702
P1033702
EYE/EAR/LUNG INJURY LABEL
709
P1033709
TOUCH-UP PAINT, GRIZZLY PUTTY
703
P1033703
ELECTRICITY LABEL
710
P1033710
TOUCH-UP PAINT, GRIZZLY GREEN
704
P1033704
BELT COVER WARNING LABEL
711
P1033711
GRIZZLY.COM LABEL
705
P1033705
DISCONNECT POWER LABEL
712
P1033712
GRIZZLY NAMEPLATE-LARGE
706
P1033706
ADD OIL NOTICE
Summary of Contents for G1033X
Page 76: ......