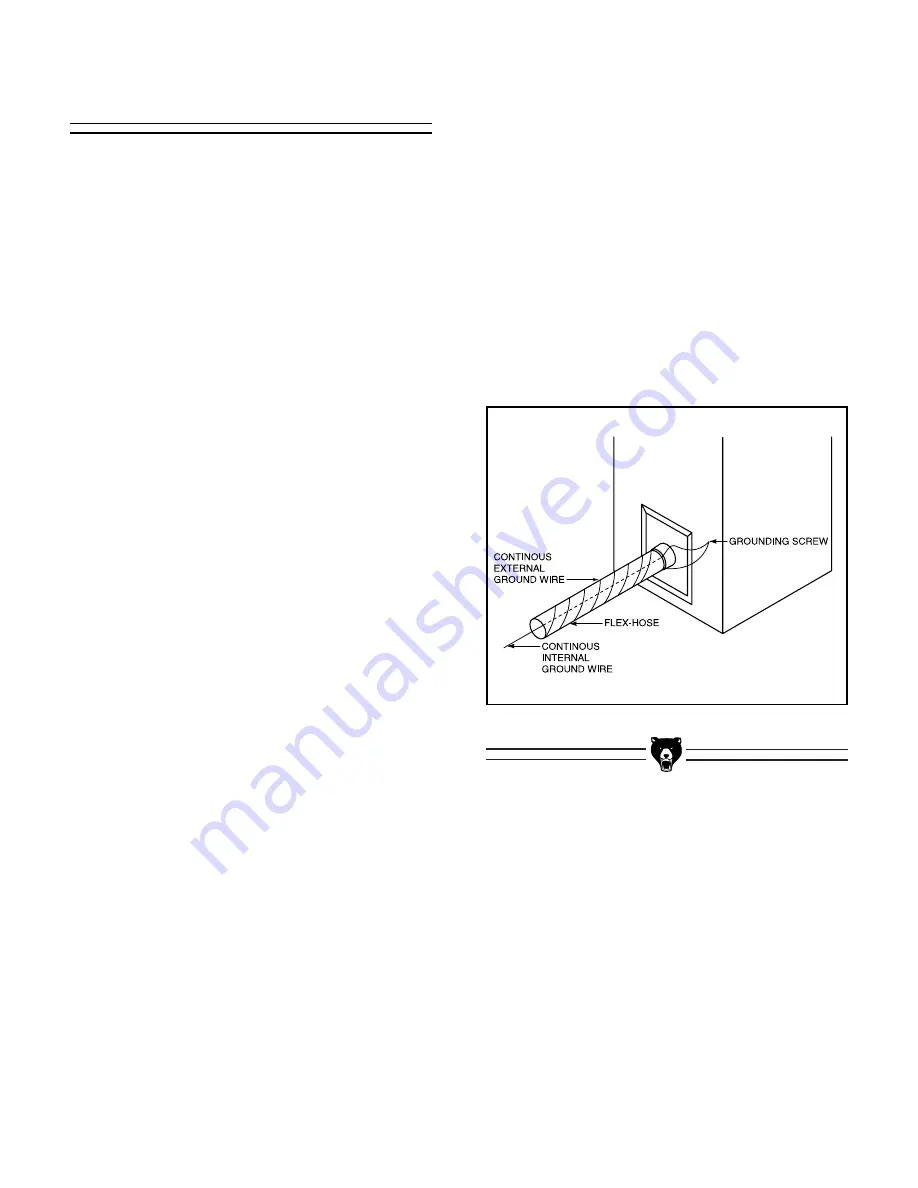
-16-
G1028/G1029 Dust Collector
System Grounding
Since plastic hose is abundant, relatively inex-
pensive, easily assembled, and airtight, it is a
very popular material for conveying dust from
woodworking machines to the dust collector. We
recommend using flexible hose (flex-hose) to
connect the woodworking machine to the dust
collector. However, plastic piping, including plas-
tic flex-hose, is an insulator, and dust particles
moving against the walls of the pipe create a sta-
tic electrical charge build-up. This charge will
build until it discharges to ground. If a grounding
medium is not available to prevent static electrical
charge build-up, the electrical discharge will arc,
similar to lightning. This electrical discharge may
cause an explosion and subsequent fire inside
the system.
To protect against static electrical charge build-
up inside a non-conducting duct, a bare copper
wire should be placed inside the duct along its
length and grounded to the dust collector. Please
ensure that the dust collector is continuously
grounded through the electrical circuit to the elec-
tric service panel.
If you connect the dust collector to more than one
machine by way of a non-conducting branching
duct system and blast gates, the system must still
be grounded as mentioned above. We recom-
mend inserting a continuous bare copper ground-
ing wire inside the entire duct system and attach-
ing the wire to each grounded woodworking
machine and dust collector.
Be sure that you extend the bare copper wire
down all branches of the system. Do not forget to
connect the wires to each other when two branch-
es meet at a Y or T connection. Use wire nuts.
Ensure that the entire system is grounded. If
using blast gates to direct air flow, the grounding
wire must be jumped around the blast gate with-
out interruption to the grounding system.
We also recommend wrapping the outside of all
plastic ducts with bare copper wire to ground the
outside of the system against static electricity
build-up. Wire connections at Y’s and T’s should
be made with wire nuts.
Attach the bare ground wire to each stationary
woodworking machine and the dust collector
frame with a ground screw. Ensure that each
machine is continuously grounded to the ground-
ing terminal in your electric service panel.
Figure 13.