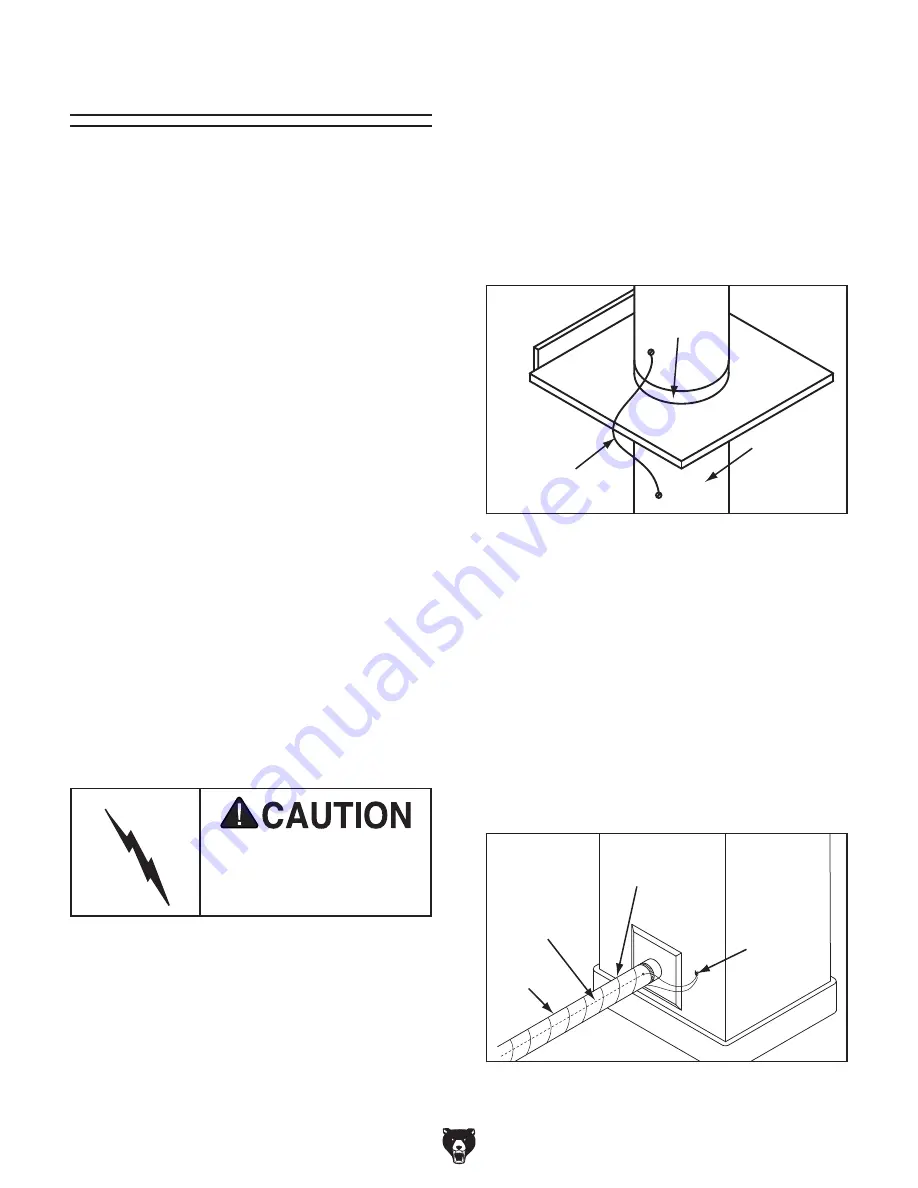
-30-
Model G0852 (Mfd. Since 12/18)
System Grounding
Since plastic hose is abundant, relatively inexpen-
sive, easily assembled and air tight, it is a very
popular material for conveying dust from wood-
working machines to the dust collector.
We recommend only using short lengths of flex-
ible hose (flex-hose) to connect the woodworking
machine to the dust collector. However, plastic
flex-hose and plastic duct are an insulator, and
dust particles moving against the walls of the
plastic duct create a static electrical buildup. This
charge will build until it discharges to a ground.
If a grounding medium is not available to prevent
static electrical buildup, the electrical charge will
arc to the nearest grounded source. This electri-
cal discharge may cause an explosion and subse-
quent fire inside the system.
To protect against static electrical buildup inside
a non-conducting duct, a bare copper wire should
be placed inside the duct along its length and
grounded to the dust collector. You must also
confirm that the dust collector is continuously
grounded through the electrical circuit to the elec-
tric service panel.
If you connect the dust collector to more than one
machine by way of a non-conducting branching
duct system and blast gates, the system must still
be grounded as mentioned above. We recom-
mend inserting a continuous bare copper ground
wire inside the entire duct system and attaching
the wire to each grounded woodworking machine
and dust collector.
Be sure that you extend the bare copper wire down
all branches of the system. Do not forget to con-
nect the wires to each other with wire nuts when
two branches meet at a “Y” or “T” connection.
Ensure that the entire system is grounded. If using
plastic blast gates to direct air flow, the ground-
ing wire must be jumped (see the figure below)
around the blast gate without interruption to the
grounding system.
We also recommend wrapping the outside of all
plastic ducts with bare copper wire to ground
the outside of the system against static electrical
buildup. Wire connections at Y’s and T’s should
be made with wire nuts.
Attach the bare ground wire to each stationary
woodworking machine and attach to the dust
collector frame with a ground screw as shown
in the figure
below. Ensure that each machine is
continuously grounded to the grounding terminal
in your electric service panel.
External
Ground Wire
Internal
Ground Wire
Flex
Hose
Ground
Screw
Figure 49. Flex-hose grounded to machine.
Plastic Blast
Gate
Copper
Ground Wire
Metal Duct
Figure 48. Ground jumper wire when using
plastic blast gates and metal duct.
Always guard against stat-
ic electrical build up by
grounding all dust collec-
tion lines.
Summary of Contents for G0852
Page 52: ......