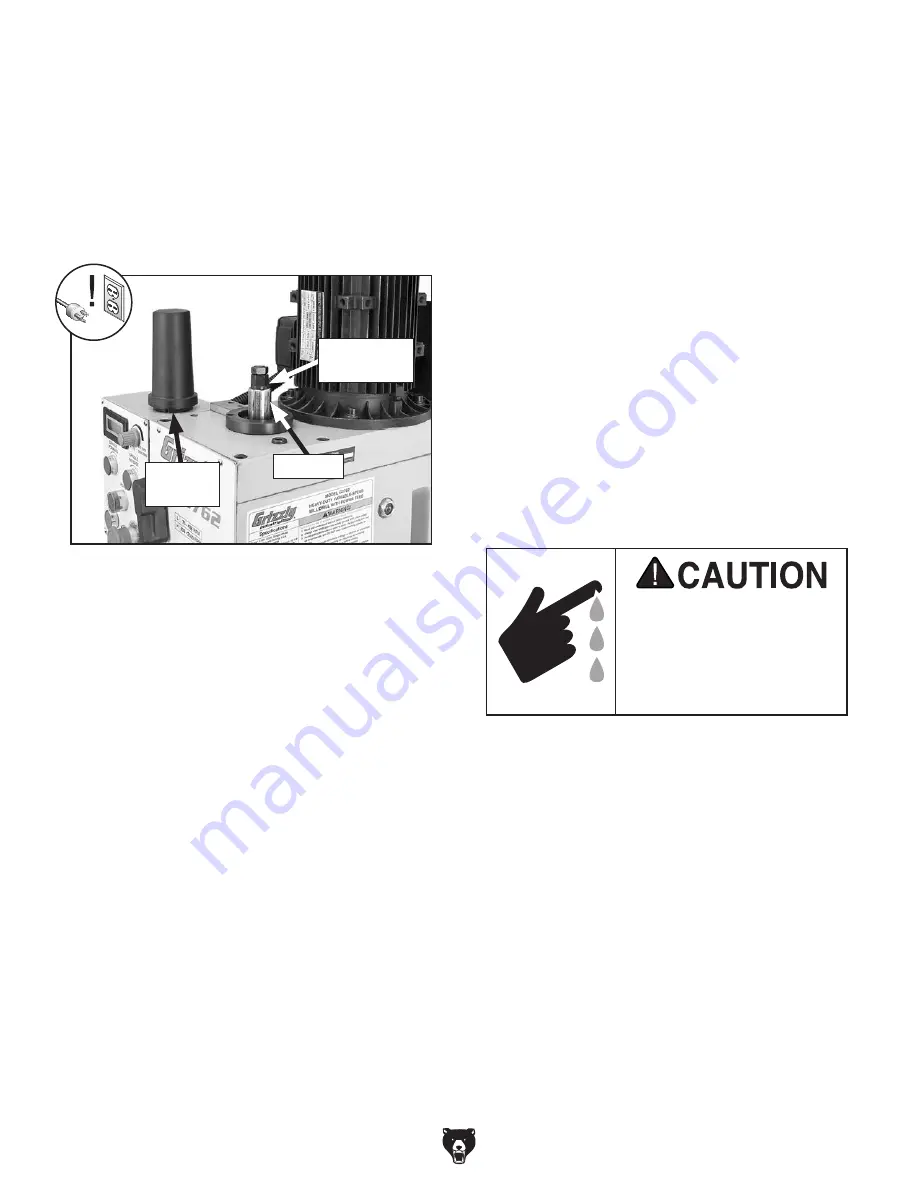
-28-
Model G0762 (Mfd. Since 5/14)
Cutting tools are sharp and
can easily cause laceration
injuries. Always protect
your hands with leather
gloves or shop rags when
handling cutting tools.
Installing Tooling
Tools Needed
Qty
Wrench 19mm ................................................... 1
To install tooling:
1. DISCONNECT MACHINE FROM POWER!
2. Remove drawbar cap, as shown in Figure 31.
3. Position tool alignment slot (see Figure 30
on previous page) with pin inside spindle,
then insert tooling into spindle until it contacts
drawbar.
Note: Height of drawbar inside spindle can
be changed by rotating adjustment nut (see
Figure 31).
4. Working from the top, thread drawbar by
hand into tooling until it is snug, then use
wrench to tighten it.
Note: Do not overtighten drawbar.
Overtightening makes tool removal difficult
and will damage arbor and threads.
5. Re-install drawbar cap.
Removing Tooling
Tools Needed
Qty
Wrench 19mm ................................................... 1
Brass Head or Dead Blow Hammer .................. 1
To remove tooling:
1. DISCONNECT MACHINE FROM POWER!
2. Remove drawbar cap.
3. Unthread drawbar from tooling one full rota-
tion.
Note: Do not fully unthread tooling from
drawbar or the drawbar and tool threads
could be damaged in the next step.
4. Tap top of drawbar with hammer to unseat
taper.
5. Hold onto tooling with one hand and fully
unthread drawbar to remove tooling.
Figure 31. Drawbar components.
Drawbar
Cap
Drawbar
Adjustment
Nut
Summary of Contents for G0762
Page 45: ...Model G0762 Mfd Since 5 14 43 Figure 51 Electrical cabinet...
Page 60: ......