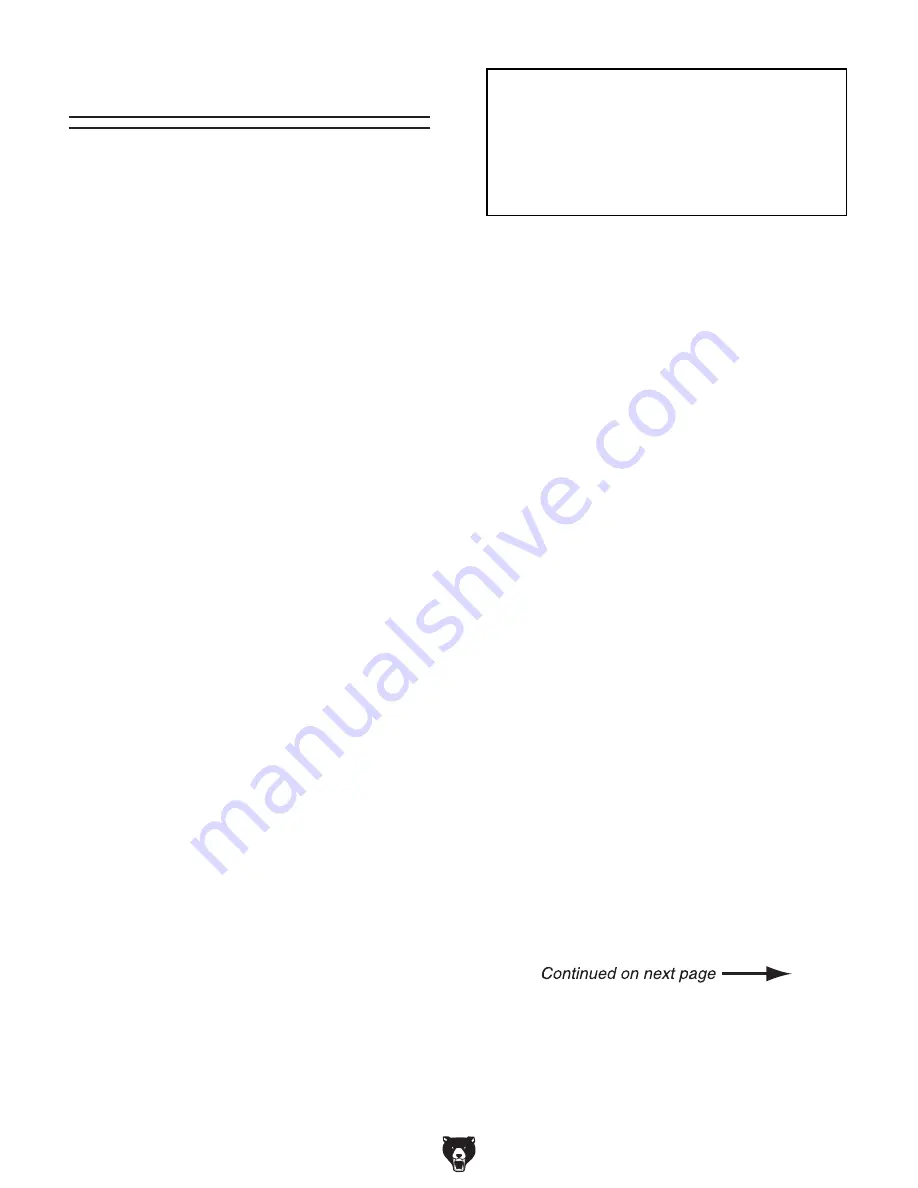
-26-
Model G0707 (Mfd. Since 01/21)
Blasting Media
Media Cost vs. Productivity
It is often assumed that by using low-cost media,
such as basic builder's sand or play sand, the
worker can enjoy increased productivity costs
because sand is so cheap. However, since sand
is a "Dull Media," the blasting tip size must be
increased and higher air pressure and more CFM
are required to increase the blast velocity to over-
come the dull media problem. This compensation
usually results in longer compressor duty cycles
that can overheat some units.
Compressor maintenance cycles, power con-
sumption, and water separator service intervals
may increase. Additionally, general sand can
cause increased down-time from clogging tips,
hoses, and valves, and generally create a hazard-
ous, silica-laden environment.
With the correct research, excellent productivity
can be achieved using sharp media with a smaller
tip and less air pressure than with dull media at a
higher pressure.
Maximizing Media Life
Screen the used media with a series of wire mesh
screens to refine it to one consistent size. When
using the blasting cabinet, experiment with using
the least amount of media as possible. The result
of using less media is that you will have less mate-
rial to screen or discard and more fresh media for
mixed projects. Store media in a dry place.
Grizzly Blasting Media Part
Numbers
G6535: 15 lbs. Aluminum Oxide 220 Grit.
G6536: 15 lbs. Aluminum Oxide 120 Grit.
G6537: 15 lbs. Aluminum Oxide 60 Grit.
G6538: 15 lbs. Glass Bead 50-Micron Grit.
Some of the common blasting media types are
listed below with the MOH scale hardness value.
All media have benefits and drawbacks, such as
the quality of surface finish, media life, toxicity,
and the precautions that must be taken to prevent
environmental damage or personal injury to your
respiratory system. However, all media presents
a health risk. Never use media that contains free
silica.
Aluminum Oxide (8.5-9)
For surface finishing, aluminum oxide is one of
the most common and widely used media. Having
an angular shape, it is considered an extremely
sharp, has extended blasting times, and is highly
recyclable.
Silicon Carbide (9-9.5)
This blast media is considered to be the hardest
available. The crystal structure is sharp, cutting
is fast and aggressive. This media is often use to
engrave and etch glass and stone. Shorter blast-
ing periods also result from this hard and sharp
media. Silicon carbide has no free silica and it can
be recycled many times.
Sand Type Media (6-7)
This media is easy to find and gives an average
finish that is acceptable for many projects. Sand
has a good recycling life and is economical.
However, the cutting ability at lower air pressure
and CFM can be poor—with a higher hazard of
silicosis and machine clogging. Many sand-type
media contain free silica and present a health
hazard for silicosis.
Summary of Contents for G0707
Page 15: ...Model G0707 Mfd Since 01 21 13 5mm Hardware Recognition Chart...
Page 46: ......
Page 48: ......