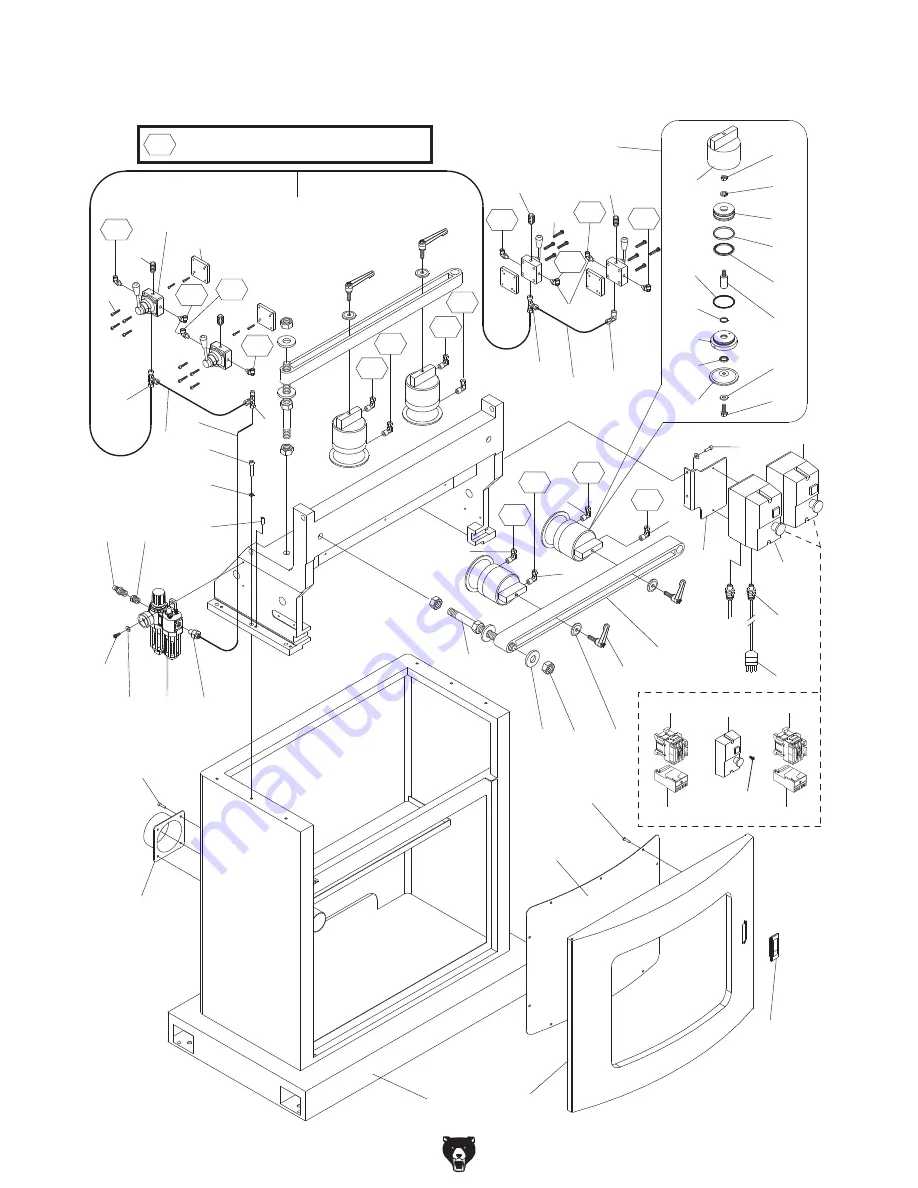
-44-
Model G0611X (Mfd. 07/15)
218
216
215
217
214
211
210 209
223
206
301
302
303
207
208
222
227
243
244
245
247
246
242
236
238
237
240
241
239
235
205
205
201V2
414
232
211
234
230
229
228
231
221
219
220
224 225
226
213
1/4
3/8
3/8
1/8
1/8
1/8
1/8
1/8
1/8
212
309
205
304
232
232
232
232
310
305
306
309
310
311
311
312
312
308
307
305
306
307
308
= AIR TUBE CONNECTION POINT
230-2
230-1
230-3
230-4
230A-2
230A-1
230A
110V
220V
234A
414
415
416
232
415
415
232
Body & Pneumatic
Summary of Contents for G0611X
Page 52: ......