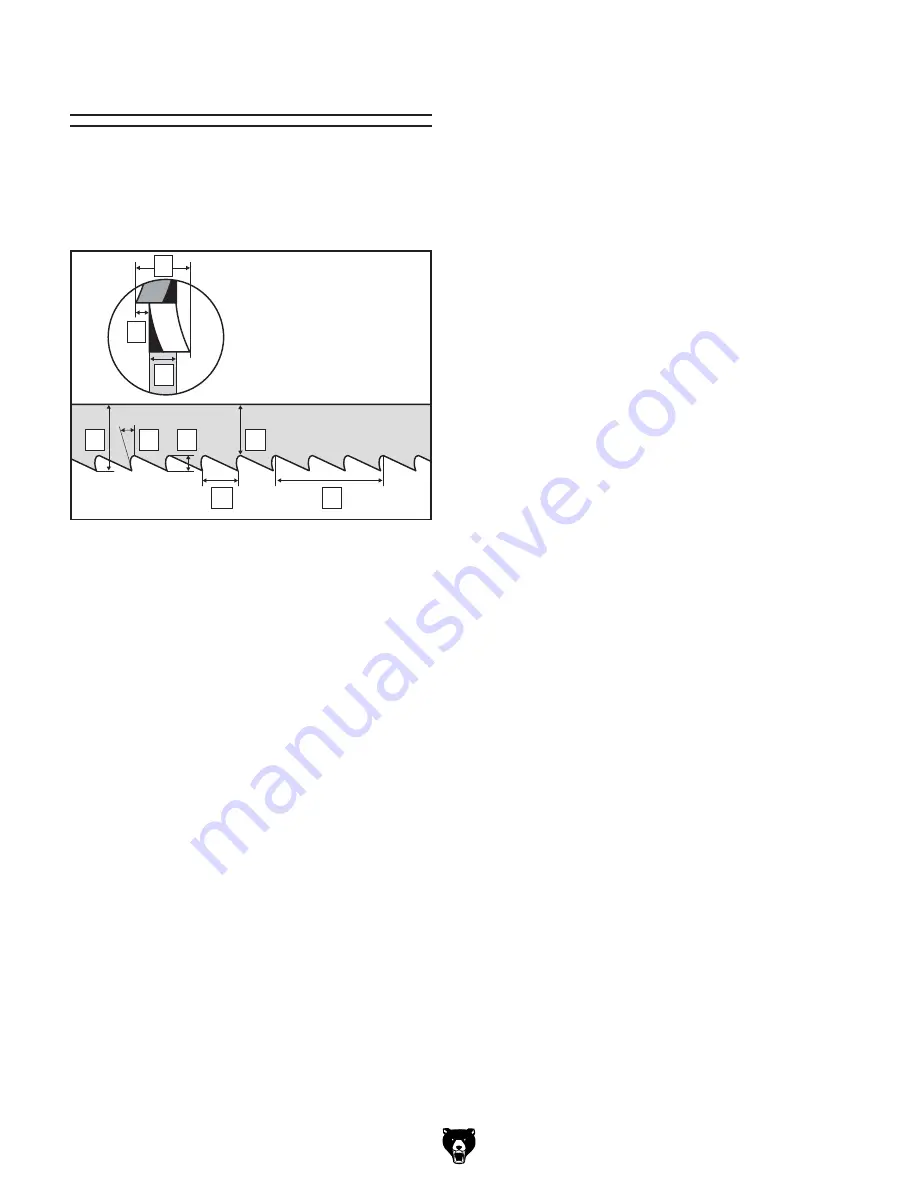
Model G0561 (Mfd. Since 01/08)
-25-
Blade Terminology
Selecting the right blade for the cut requires a
knowledge of various blade characteristics.
Blade Terminology
A. Kerf: Amount of material removed by blade
during cutting.
B. Tooth Set: Amount each tooth is bent left or
right from blade.
C. Gauge:
Thickness of blade.
D. Blade Width: Widest point of blade mea-
sured from tip of the tooth to back edge of the
blade.
E. Tooth Rake: Angle of tooth from a line per-
pendicular to length of blade.
F. Gullet Depth: Distance from tooth tip to bot-
tom of curved area (gullet).
G. Tooth Pitch: Distance between tooth tips.
H. Blade Back: Distance between bottom of
gullet and back edge of blade.
I. TPI:
Number of teeth per inch measured
from gullet to gullet.
Figure 30. Bandsaw blade terminology.
G
B
C
D
E
F
H
I
A
Summary of Contents for G0561
Page 60: ......