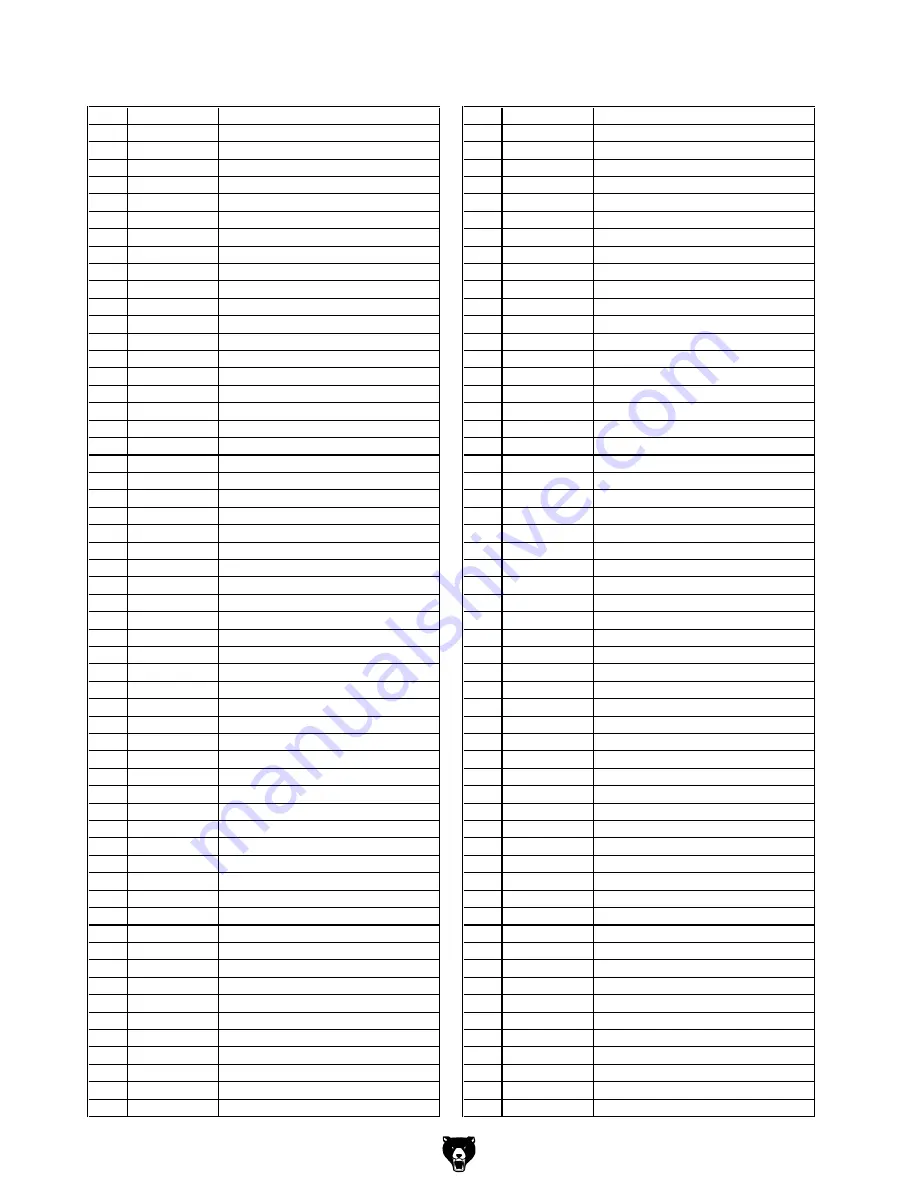
-40-
G0456 Variable Speed Wood Lathe
REF PART #
DESCRIPTION
REF PART #
DESCRIPTION
1
P0456001
BED
56
P0456056
HANDWHEEL HANDLE
2
P0456002
CABINET STAND
57
P0456057
TOOL REST BASE
3
PSB147M
CAP SCREW 7/16-14 X 1-1/2
58
P0456058
TOOL REST
4
PW06
FLAT WASHER 1/4
59
P0456059
LOCK HANDLE M8-1.25 X 15
5
PLW05
LOCK WASHER 7/16
60
P0456060
STEEL TUBE
6
PW04
FLAT WASHER 7/16
61
P0456061
KNOB 3/8"
7
PSB144M
CAP SCREW M6-1 X 25 LH
62
P0456062
TOOL REST LOCK SHAFT
8
PB36
HEX BOLT 7/16-14 X 3/4
63
PR47M
EXT RETAINING RING 13MM
9
P0456009
L-BRACKET
64
P0456064
HANDLE SHAFT
10
PLN03
LOCK NUT 5/16-18
65
P0456065
WINDOW PLATE 55.8 X 24.4 X 2
11
P0456011
DOOR
66
P0456066
CIRCUIT BOARD MAG SYSTEM
12
P0456012
STAND ACCESS HANDLE
66-1
P0456066-1
SPEED POTENTIOMETER
13
P0456013
RUBBER FOOT
66-2
P0456066-2
MAGNETIC RING
14
PS79
PHLP HD SCR 5/16-18 X 5/8
67
P0456067
TRANSFORMER/INDICATOR SYS
15
P0456015
PARTITION BOARD
68
P0456068
SPEED DIAL
16
PSB79M
CAP SCREW M5-.8 X 35
69
P0456069
PADDLE SWITCH W/KEY
17
P0456017
RIGHT STAND
70
PHTEK18
TAP SCREW #10 X 5/8
18
P0456018
HEAD STOCK
71
PHTEK30M
TAP SCREW M3 X 6
19
PB26M
HEX BOLT M8-1.25 X 30
72
P0456072
KEY 5 X 5 X 12
20
P0456020
BELT WHEEL COVER
73
PLW03
LOCK WASHER #10
21
P0456021
MOTOR MOUNT PLATE
74
P0456074
PLATE STICKER
22-1
P0456022-1
BRUSH
75
P0456075
DUST PORT
22-2
P0456022-2
BRUSH RETAINER
76
P0456076
LEFT SCALE
22-3
P0456022-3
BRUSH COVER
76A
P0456076A
RIGHT SCALE
22A
P0456022A
MOTOR W/HANDLE
77
PN02
HEX NUT 5/16"-18
23A
P0456023A
MOTOR STEP PULLEY
78
P0456078
LOCK HANDLE M6-1 X 12
24
PK10M
KEY 5 X 5 X 12
79
PB09
HEX BOLT 5/16-18 X 1/2
25
PSS03
SET SCREW 1/4-20 X 3/8
80
PW07
FLAT WASHER 5/16
26A
P0456026A
DRIVE STEP PULLEY
81
PW03M
FLAT WASHER 6MM
27
P0456027
SANDING DISC
82
P0456082
SPECIAL SCREW 5/16-18 X 5/8
28
P6005
BALL BEARING 6005
83
PS01
PHLP HD SCR 10-24 X 1/2
29
P0456029
SENSOR SUPPORTING FRAME
84
P0456084
TABLE
30
P0456030
CORD FIXER UC-0*3.2
85
P0456085
DISC SCALE
31
PS06M
PHLP HD SCR M5-.8 X 20
86
P0456086
COMPLETE MITER GAUGE
32
P0456032
SENSOR CORD
86-1
P0456086-1
HANDLE 1/4-20 X 7/8
33
PB87M
HEX BOLT M8-1.25 X 15
86-11 P0456086-11
ROLL PIN 3 X 5MM
34
P0456034
MAGNETIC FIXER
86-12 P0456086-12
SOLID PIN 8 X 20MM
35
P0456035
SPINDLE
86-2
P0456086-2
WASHER 1/4
36
P0456036
BACKING PLATE
86-3
P0456086-3
MITER GAUGE BODY
37
P0456037
HEX NUT 1-1/2"- 8
86-4
P0456086-4
MITER BAR
38
P0456038
SPUR REMOVAL NUT 1-1/2"-8
86-5
P0456086-5
HEX NUT 8-32
39
P0456039
SPUR CENTER
86-6
P0456086-6
PHLP HD SCREW 8-32 X 3/4
40
P0456040
TAILSTOCK BASE
86-7
P0456086-7
SET SCREW 1/4-20 X 1/4
41
P0456041
TAILSTOCK SPINDLE
86-8
P0456086-8
STOP
42
P0456042
SHORT HANDLE
86-9
P0456086-9
POINTER
43
P0456043
CAM SPINDLE
87
P0456087
FLAT WRENCH 1-13/16"
44
P0456044
QUILL
88
P0456088
SPINDLE LOCK PIN
45
P0456045
LIVE CENTER SHAFT
90
P0456090
BELT 200J
46
P6002
BALL BEARING 6002
91
PLW01
LOCK WASHER 5/16
47
P0456047
LIVE CENTER HEAD
92
P6006
BEARING 6006
48
P0456048
TAILSTOCK LOCK SHAFT
93
PB94M
HEX BOLT M5-.8 X 25
49
P0456049
FACEPLATE
94
P0456094
POINTER
50
PSB50M
CAP SCREW M5-.8 X 10
95
P0456095
UPPER SPACER
51
P0456051
LOCKING RING SHAFT
96
PN06M
HEX NUT M5-.8
52
PLN03
LOCK NUT 5/16-18
108
P0456108
FRONT COVER
53
PW07
FLAT WASHER 5/16
109
P0456109
KNOB
54
P0456054
SLIDING BLOCK
110
P0456110
REAR COVER
55
P0456055
HANDWHEEL
112
P0456112
TOOL REST EXTENSION
Parts List
Summary of Contents for G0456
Page 6: ...6 G0456 Wood Lathe Parts Breakdown Effective 10 2007...
Page 10: ......
Page 48: ...38 G0456 Variable Speed Wood Lathe Wiring Diagram...
Page 49: ...G0456 Variable Speed Wood Lathe 39 Parts Breakdown...
Page 53: ......
Page 54: ......
Page 55: ......
Page 56: ......