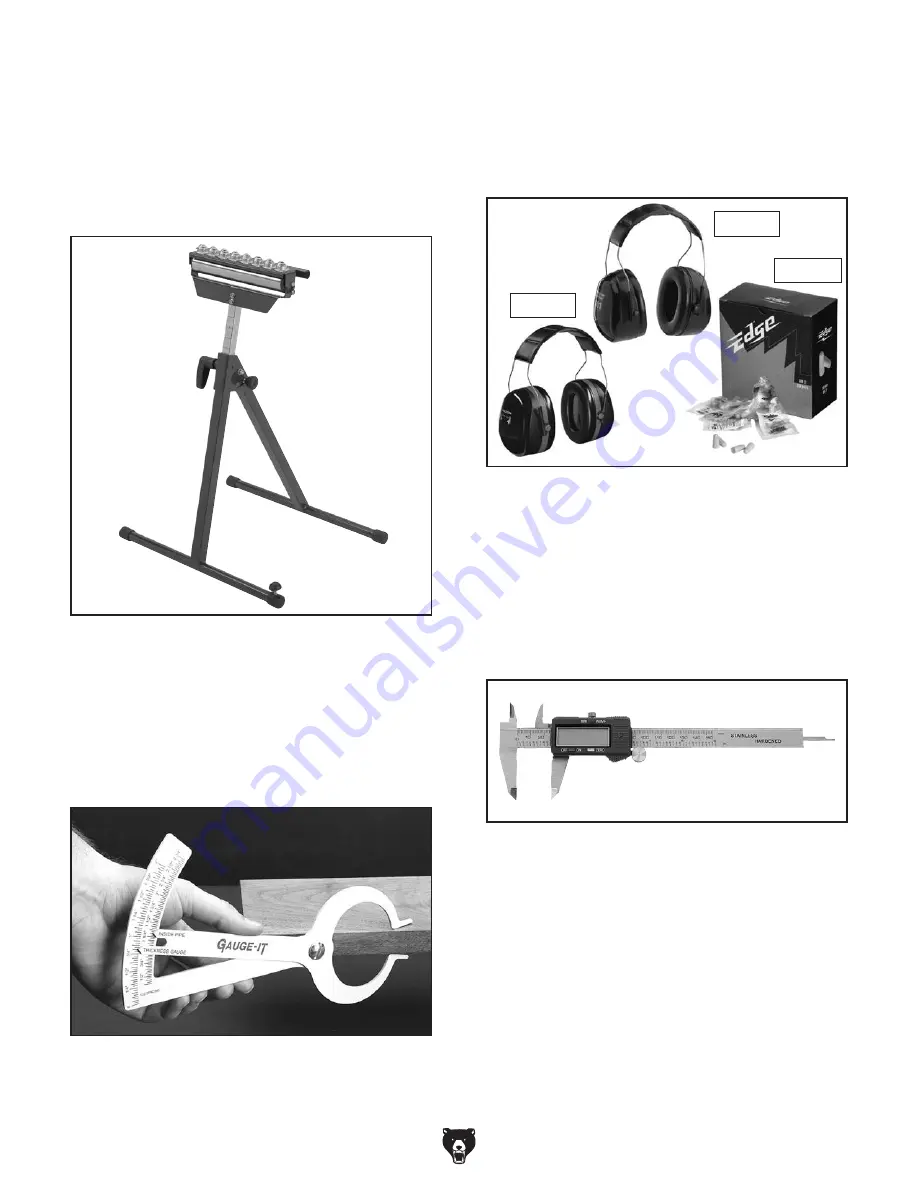
-32-
G0453W/ZW–G0454W/ZW (Mfd. Since 05/16)
H4978—Deluxe Earmuffs - 27dB
H4979—Twin Cup Hearing Protector - 29dB
T20446—Classic Earplugs, 200-pair - 31dB
Protect yourself comfortably with a pair of cush-
ioned earmuffs. Especially important if you or
employees operate for hours at a time.
Figure 45. Hearing protection.
H4978
T20446
H4979
G2857—Thickness Gauge
Measure thicknesses and diameters quickly with
this handy gauge. Wonderful for thickness plan-
ers, wood lathes, and other shop measurements.
Measures from 1⁄16" to 2" in 1⁄32" increments.
Made in the U.S.A.
Figure 44. G2857 Thickness Gauge.
Figure 43. T26979 3-in-1 Workpiece Support
Stand.
T26979—3-in-1 Workpiece Support Stand
This 3-in-1 Workpiece Support Stand features a
rotating head with steel roller topped with 8 roll-
ing balls. The heavy-duty steel frame has four
outrigger legs for stability and an adjustable foot
for uneven floors. Height adjusts from 27 1⁄2" to
43" and supports up to 250 lbs. It even folds up
for easy storage!
Figure 46. H7978 Fractional Digital Caliper.
H7978—Fractional Digital Caliper
Large LCD readout converts to decimal inch,
fractional inch, and millimeters with the push of
a button. Measure internal, external dimensions,
depth, steps and differential measurements.
Features thumb roll and stainless steel construc-
tion. Range: 0–6", 0–150mm. Resolution: 0.0005",
0.01mm,
1
⁄
128
".
order online at
www.grizzly.com
or call
1-800-523-4777
Summary of Contents for G0453W
Page 76: ......