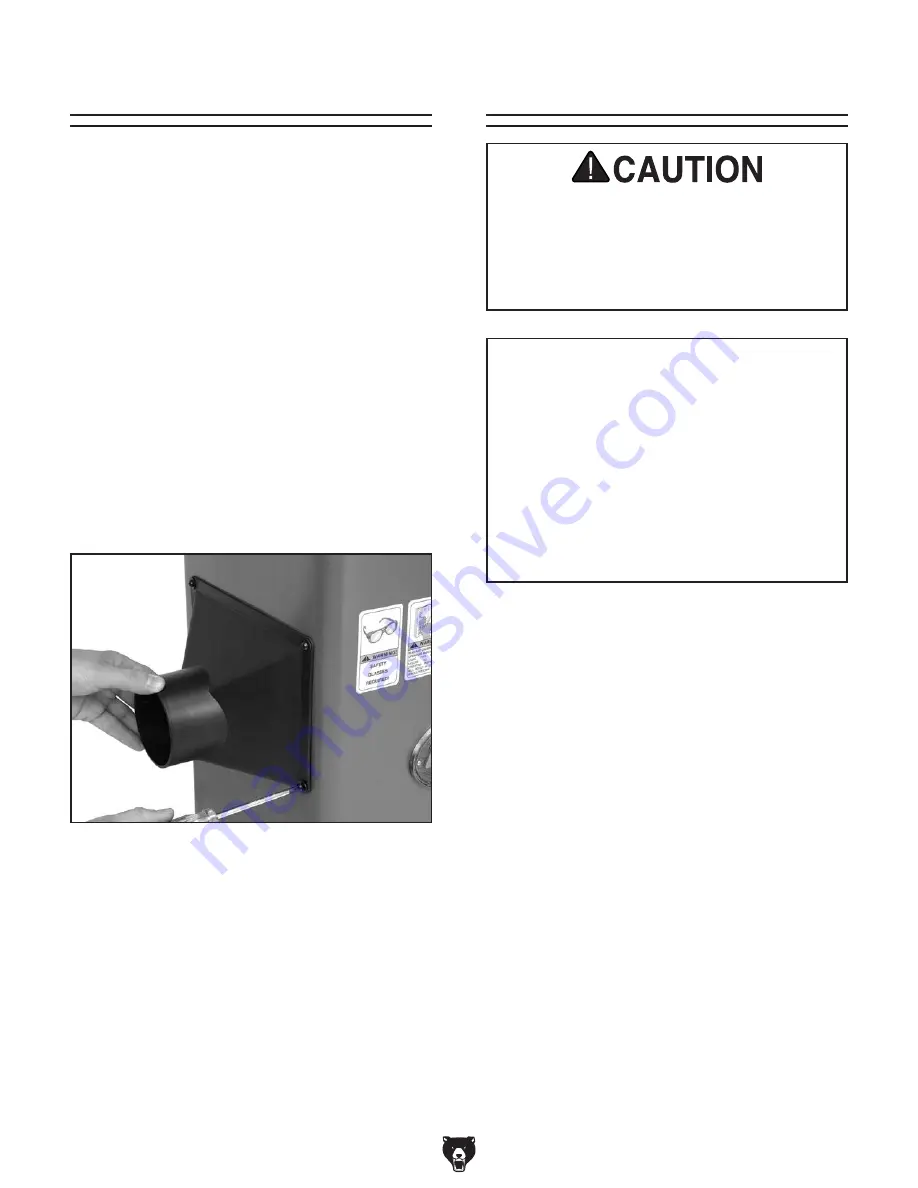
-24-
Model G0452/P/Z (Mfg. Since 08/12)
Figure 25. Dust port installation.
Components and Hardware Needed:
Qty
Dust Port ........................................................... 1
Phillips Head Screws M5-.8 x 15 ....................... 4
Flat Washers 5mm ............................................ 4
Tools Needed:
Qty
Phillips Head Screwdriver .................................. 1
To install the dust port:
Note: If you choose to not use a dust collection
system, don't install the dust port. Chips will build
up inside the cabinet and clog.
1. Place the dust port over the dust vent in the
side of the cabinet.
2. Use the M5-.8 x 15 Phillips head screws and
flat washers to secure the dust port to the
cabinet (see
Figure 25).
3. Attach to dust collection system.
Dust Port
Dust Collection
To connect a dust collection hose:
1. Fit the 4" dust hose over the dust port, as
shown in
Figure 25, and secure in place with
a hose clamp.
2. Tug the hose to make sure it does not come
off.
Note: A tight fit is necessary for proper
performance.
This machine creates a lot of wood chips/
dust during operation. Breathing airborne
dust on a regular basis can result in perma-
nent respiratory illness. Reduce your risk
by wearing a respirator and capturing the
dust with a dust collection system.
Recommended CFM at Dust Port: 400 CFM
Do not confuse this CFM recommendation with
the rating of the dust collector. To determine the
CFM at the dust port, you must consider these
variables: (1) CFM rating of the dust collector,
(2) hose type and length between the dust col-
lector and the machine, (3) number of branches
or wyes, and (4) amount of other open lines
throughout the system. Explaining how to cal-
culate these variables is beyond the scope of
this manual. Consult an expert or purchase a
good dust collection "how-to" book.
Summary of Contents for G0452
Page 64: ......