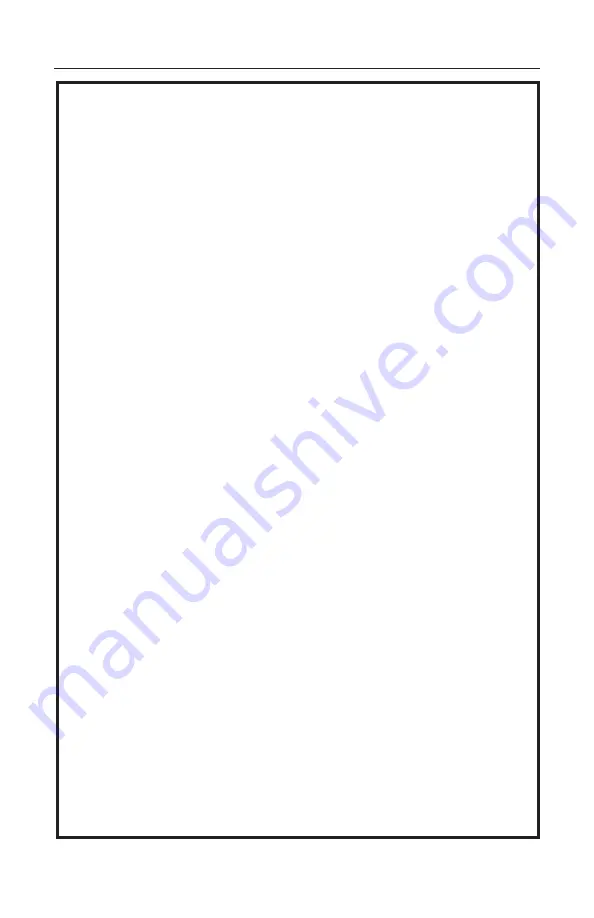
18
PNEUMATIC TOOL/COMPRESSOR WARRANTY
Pneumatic nailers, staplers & compressors marketed under the GRIP
RITE TM brand are warranted to be free from defects in workmanship &
materials (except rubber o-rings, bumpers, seals, driver blades, dipsticks,
& air filters) for a period of one year from the date of original purchase.
This warranty will not apply when:·
The original receipt (or copy of the original receipt), showing the origi-
•
nal purchase date, is not provided with tools/compressors sent in for
warranty repair·
The tool/compressor has been misused, abused or improperly main-
•
tained
Alterations have been made to the original tool/compressor·
•
Repairs have been attempted/made to the original tool/compressor
•
by any entity other than a proprietary GRIP-RITE® service/waranty
center or authorized service/warranty center
Non-GRIP-RITE TOOLS
•
TM
/ GRIP-RITE COMPRESSORS
TM
/parts
have been used
The tool has suffered any physical damage due to the use of
•
non- GRIP-RITE ® approved fasteners*·
Repairs are required due to normal wear & tear·
•
The tool/compressor has been inadequately packaged leading to
•
damage in-transit to the service/warranty center
*Approved fasteners include the following brands GRIP-RITE
FAS’NERS
TM
, FAS’NERS UNLIMITED
TM
IN NO EVENT SHALL PRIMESOURCE® BE LIABLE FOR ANY INDI-
RECT, ACCIDENTAL OR CONSEQUENTAL DAMAGE FROM THE SALE
OR USE OF THESE PRODUCTS. THIS DISCLAIMER APPLIES BOTH
DURING & AFTER THE TERM OF WARRANTY.
THIS IS OUR WARRANTY & IS EXPRESSLY IN LIEU OF ALL OTHER
WARRANTIES, EXPRESS OR IMPLIED, INCLUDING THE WARRAN-
TIES OF MERCHANTABILTY AND FITNESS FOR A PARTICULAR PUR-
POSE (EXCEPT AS MAY BE OTHERWISE PROVIDED BY LAW).
THIS LIMITED WARRANTY GIVES YOU SPECIFIC LEGAL RIGHTS,
AND YOU MAY ALSO HAVE OTHER RIGHTS, WHICH VARY, FROM
STATE TO STATE.
WARRANTY