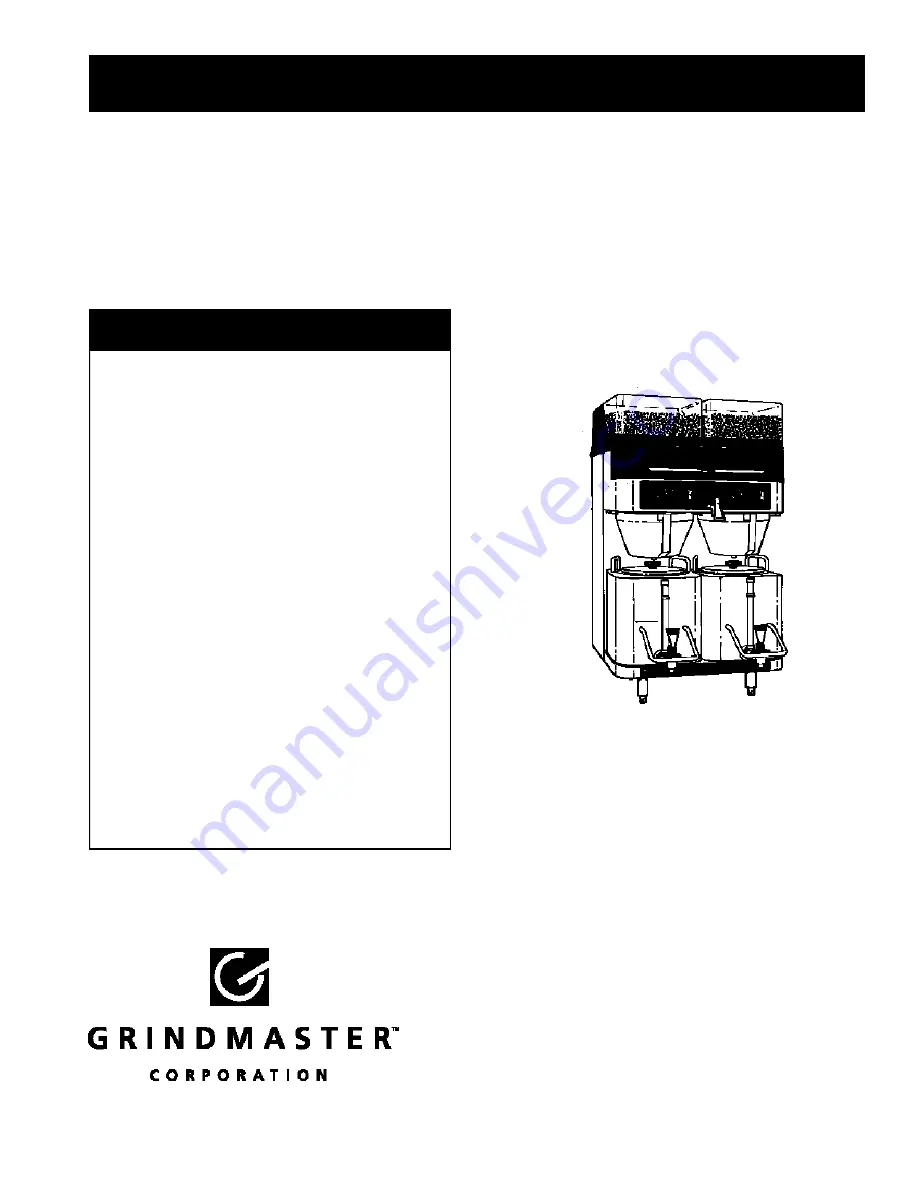
Grindmaster Corporation
4003 Collins Lane
Louisville, KY 40245
(502) 425-4776 (800) 695-4500
(800) 568-5715 (Technical Service Only)
FAX (502) 425-4664
www.grindmaster.com
1103 Form #AM-352-04
Part # A090-094
ECN # 1091
Rev. Rel.
© Grindmaster Corporation, 1998
PRINTED IN THE USA
American Metal Ware
®
Brewers
Operation and Instruction Manual
for
Model: P400GNB-E
Prior authorization must be obtained
from Grindmaster Corporation
for all warranty claims.
Model P400GNB-E
TABLE OF CONTENTS
Warning Labels ........................................2
Start Up Procedures .............................3-6
Operation ..............................................6-7
Adjustments ..........................................7-9
Care and Cleaning............................10-12
Service ..............................................12-13
Troubleshooting ................................14-18
Installation Rough-In Drawings ..............19
Exploded Views ................................20-25
Wiring Diagrams ...............................26-27