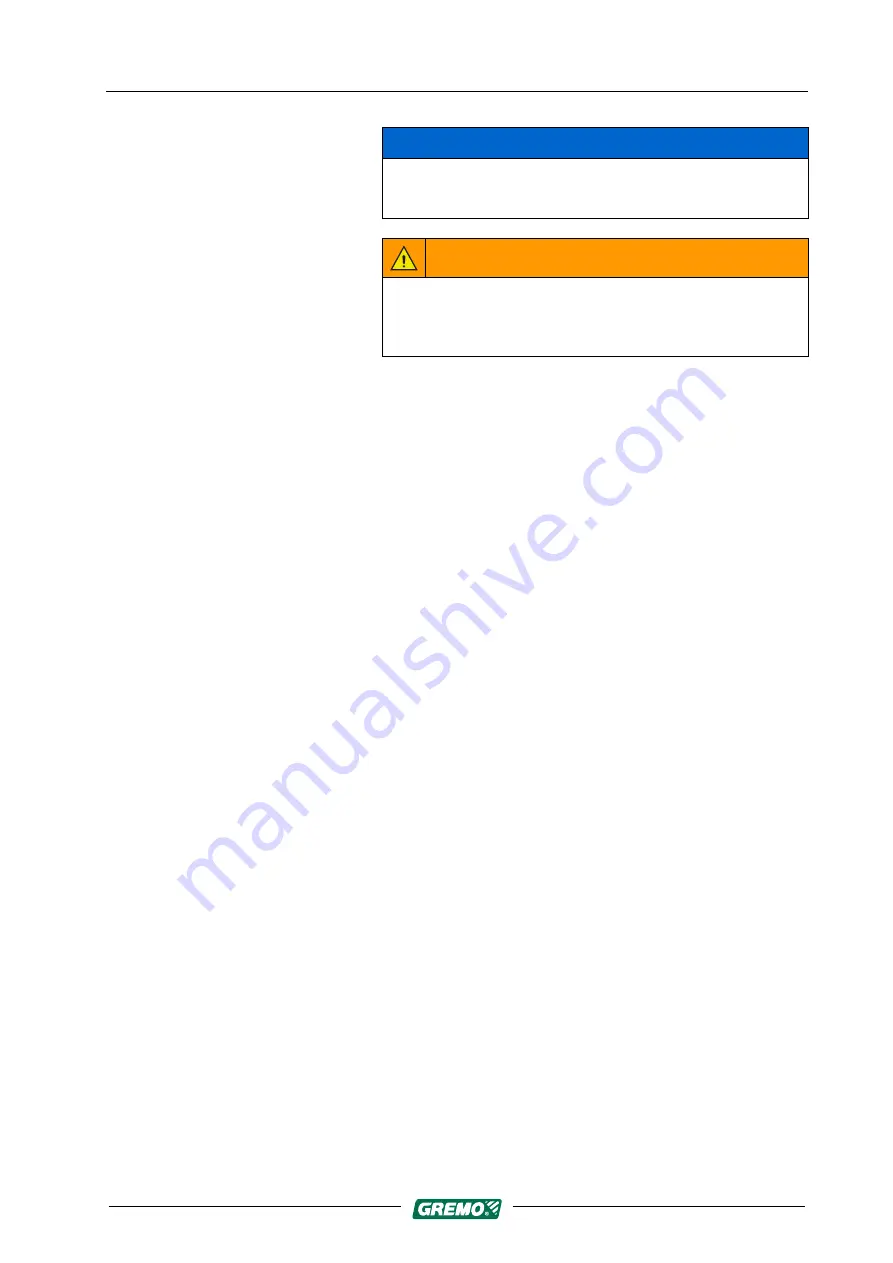
Gremo1050F4 Instruction manual
NOTICE
Never use tyre chains or tracks on tarmac roads. You
could be liable for any surface damage that occurs.
WARNING
The cab is not intended for passenger transport, which is
why it lacks a seat and seat belt for passengers. There is
a risk of fatal accident for passengers!
138