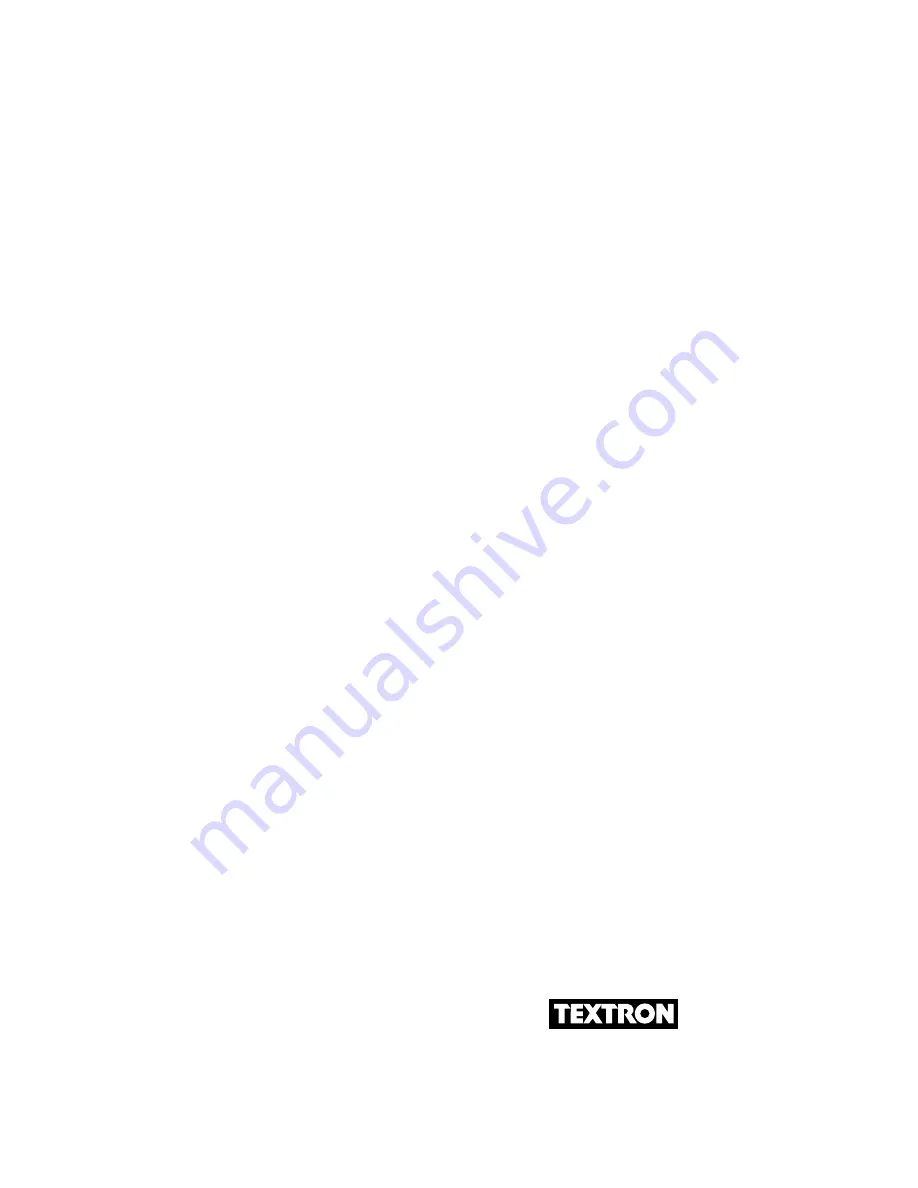
Printed in U.S.A.
Greenlee Textron / Subsidiary of Textron Inc.
4455 Boeing Drive, Rockford, IL 61109-2988 USA
General Offices: 815/397-7070
Customer Center and Field Service: 800/435-0786
Fax (24 Hour) Customer Center: 800/451-2632 • 815/397-1865
Canada Fax (24 Hour) Customer Center: 800/524-2853
GREENLEE FAIRMONT
Appendix A (cont’d)
3. INSTALLATION
After selection of proper hose, the following factors must
be considered by the installer.
3.1 Pre-Installation Inspection - Prior to installation, a
careful examination of the hose must be performed. All
components must be checked for correct style, size, and
length. In addition, the hose must be examined for cleanli-
ness, I.D. obstructions, blisters, loose cover, or any other
visual defects.
3.2 Follow Manufacturers’ Assembly Instructions.
3.3 Minimum Bend Radius - Installation at less than
minimum bend radius may significantly reduce hose life.
Particular attention must be given to preclude sharp
bending at the hose/fitting juncture.
3.4 Twist Angle and Orientation - Hose installations must
be such that relative motion of machine components
produces bending of the hose rather than twisting.
3.5 Securement - In many applications, it may be neces-
sary to restrain, protect, or guide the hose to protect it from
damage by unnecessary flexing, pressure surges, and
contact with other mechanical components. Care must be
taken to insure such restraints do not produce additional
stress or wear points.
3.6 Proper Condition of Ports - Proper physical installation
of the hose requires a correctly installed port connection
while insuring that no twist or torque is put into the hose.
3.7 Avoid External Damage - Proper installation is not
complete without insuring tensile loads, side loads, kinking,
flattening, potential abrasion, thread damage, or damage
to sealing surfaces are corrected or eliminated.
3.8 System Check Out - After completing the installation,
all air entrapment must be eliminated and the system
pressurized to the maximum system pressure and checked
for proper function and freedom from leaks.
Note: Avoid potential hazardous area while testing.
4. MAINTENANCE
Even with proper selection and installation, hose life
may be significantly reduced without a continuing mainte-
nance program. Frequency should be determined by the
severity of the application and risk potential.
A maintenance program should include the following as a
minimum.
4.1 Hose Storage - Hose products in storage can be
affected adversely by temperature, humidity, ozone,
sunlight, oils, solvents, corrosive liquids and fumes,
insects, rodents and radioactive material. Storage areas
should be relatively cool and dark, and free of dust, dirt,
dampness and mildew.
4.2 Visual Inspection - Any of the following conditions
requires replacement of the hose:
(a) Leaks at fitting or in hose. (Leaking fluid is a fire
hazard).
(b) Damaged, cut or abraded cover. (Any reinforcement
exposed).
(c)
Kinked, crushed, flattened or twisted hose.
(d) Hard, stiff, heat cracked or charred hose.
(e) Blistered, soft degraded or loose cover.
(f)
Cracked, damaged, or badly corroded fittings.
(g) Fitting Slippage on hose.
4.3 Visual Inspection - The following items must be
tightened, repaired, or replaced as required:
(a) Leaking port conditions.
(b) Clamps, guards, shields.
(c)
Remove excessive dirt buildup.
(d) System fluid level, fluid type, and any air entrapment.
4.4 Functional Test - Operate the system at maximum
operating pressure and check for possible malfunctions
and freedom from leaks.
Note: Avoid potential hazardous areas while testing.
4.5 Replacement Intervals - Specific replacement inter-
vals must be considered based on previous service life,
government or industry recommendations, or when
failures could result in unacceptable down time, damage,
or injury risk.
*Reprinted with permission
©
1990 from the Society of
Automotive Engineers, Inc. Handbook.