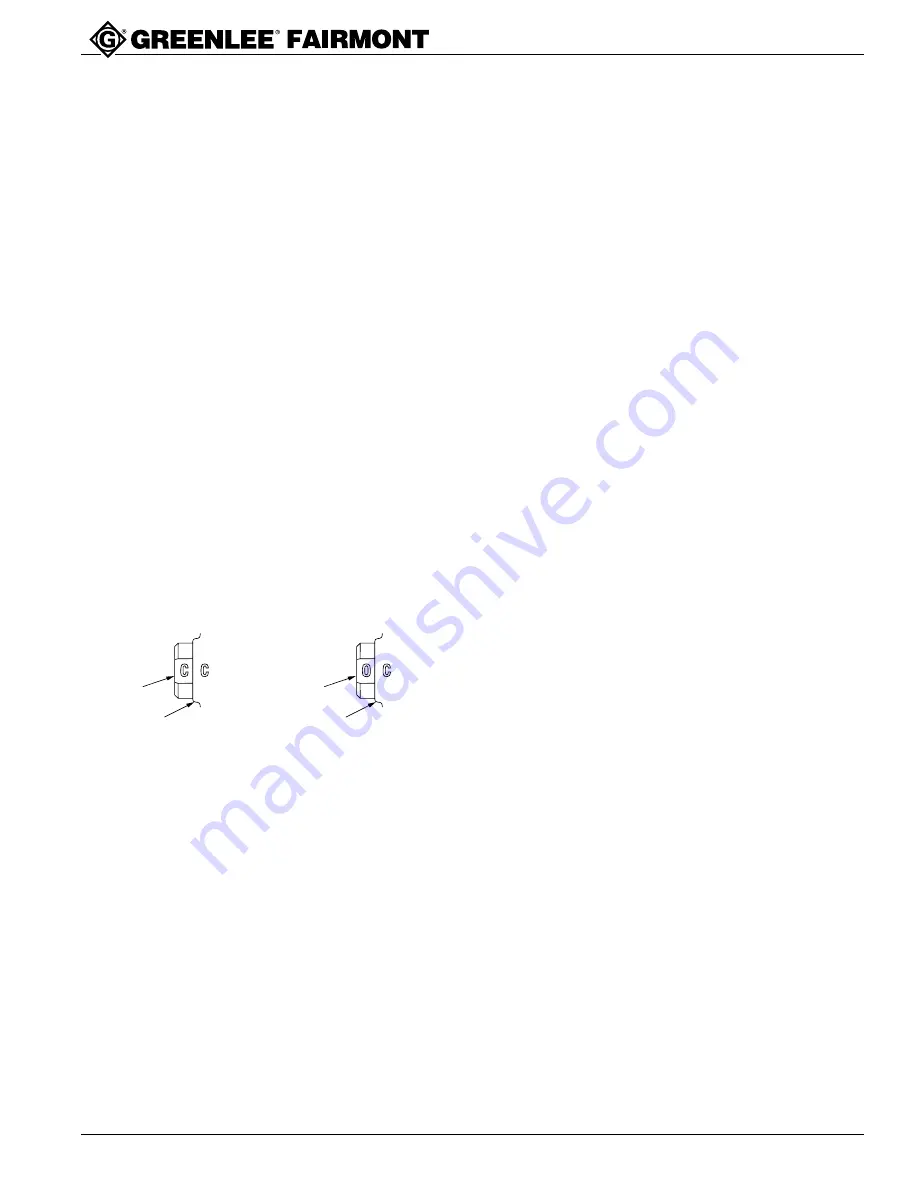
11
H6200B / 42247 Chain Saw
Greenlee Textron / Subsidiary of Textron Inc.
4455 Boeing Dr., Rockford, IL 61109-2988 815/397-7070
Figure 4
Setting the Super Spool™ Position
Operation (cont’d)
Setting the Super Spool™ Position
(See Figure 4)
The H6200B Chain Saw is equipped with the Greenlee
Fairmont patented Super Spool™ to allow the tool to be
used with either an Open-Center or Closed-Center
hydraulic power system.
Closed-Center Hydraulic System
1.
Stop the power source.
2.
Turn the Super Spool™ (1) so that the letter “C”,
stamped in the flat of the spool, is aligned with the
letter “C”, stamped in the right side of the tool
handle (2).
Open-Center Hydraulic System
1.
Stop the power source.
2.
Turn the Super Spool™ (1) so that the letter “O”,
stamped in the flat of the spool, is aligned with the
letter “C”, stamped in the right side of the tool
handle (2).
6.
Check the automatic chain oiler. The chain will give
off a fine spray of oil at the guide bar nose if the
oiler is working properly.
7.
New saw chains require break-in before cutting any
wood. See New Saw Chain Break-in (page 15).
Operation (See Figures 1 and 2)
1.
Grasp the auxiliary handle (13) with your left hand
and the trigger handle (12) with your right hand.
Note: Left-handed operators must follow these hand
placement instructions also.
2.
Position the saw in the area to make the desired cut.
3.
To start the saw, move the trigger safety latch (10)
forward and depress (squeeze) trigger (9).
4.
Feed the rotating saw chain into the wood using a
steady, constant pressure. DO NOT TWIST THE
GUIDE BAR IN THE SAW CUT. DO NOT BUMP,
JAM OR FORCE GUIDE BAR NOSE INTO THE
WOOD.
5.
Feed the saw chain through the wood as fast as
possible without slowing the chain in the cut.
6.
To stop the saw, release the trigger (9).
7.
AFTER THE SAW CHAIN HAS STOPPED ROTAT–
ING, lay the saw on a flat surface or hang up the
saw.
8.
When the chain saw is not in use, stop the power
source to reduce heat and wear on the tool com-
ponents.
Important
1.
Check the automatic oiler setting frequently. Insuffi-
cient lubrication can ruin the saw chain and/or guide
bar.
2.
Check the saw chain tension frequently, especially
when the saw is initially put into service.
3.
Check the fluid level of the power source reservoir
frequently. Fluid level will drop due to the automatic
oiler.
Pre-Operation (See Figures 1 and 2)
1.
Stop the power source. Disconnect tool from power
source.
2.
Inspect the saw chain. Chain must be properly
sharpened and have no worn or damaged compo-
nents. AN IMPROPERLY SHARPENED, DULL,
WORN AND/OR DAMAGED CHAIN INCREASES
THE RISK OF KICKBACK.
3.
Check the saw chain tension. See Saw Chain
Tension (page 15).
4.
Connect the hydraulic hoses from the power source
to the tool. Start the power source.
5.
It is recommended that the power source be al-
lowed to run (idle) for a few minutes to warm the
hydraulic reservoir fluid. Actuating the saw intermit-
tently will reduce the time required to warm the fluid
to an efficient operating temperature.
CLOSED - CENTER
OPEN - CENTER
1
2
1
2