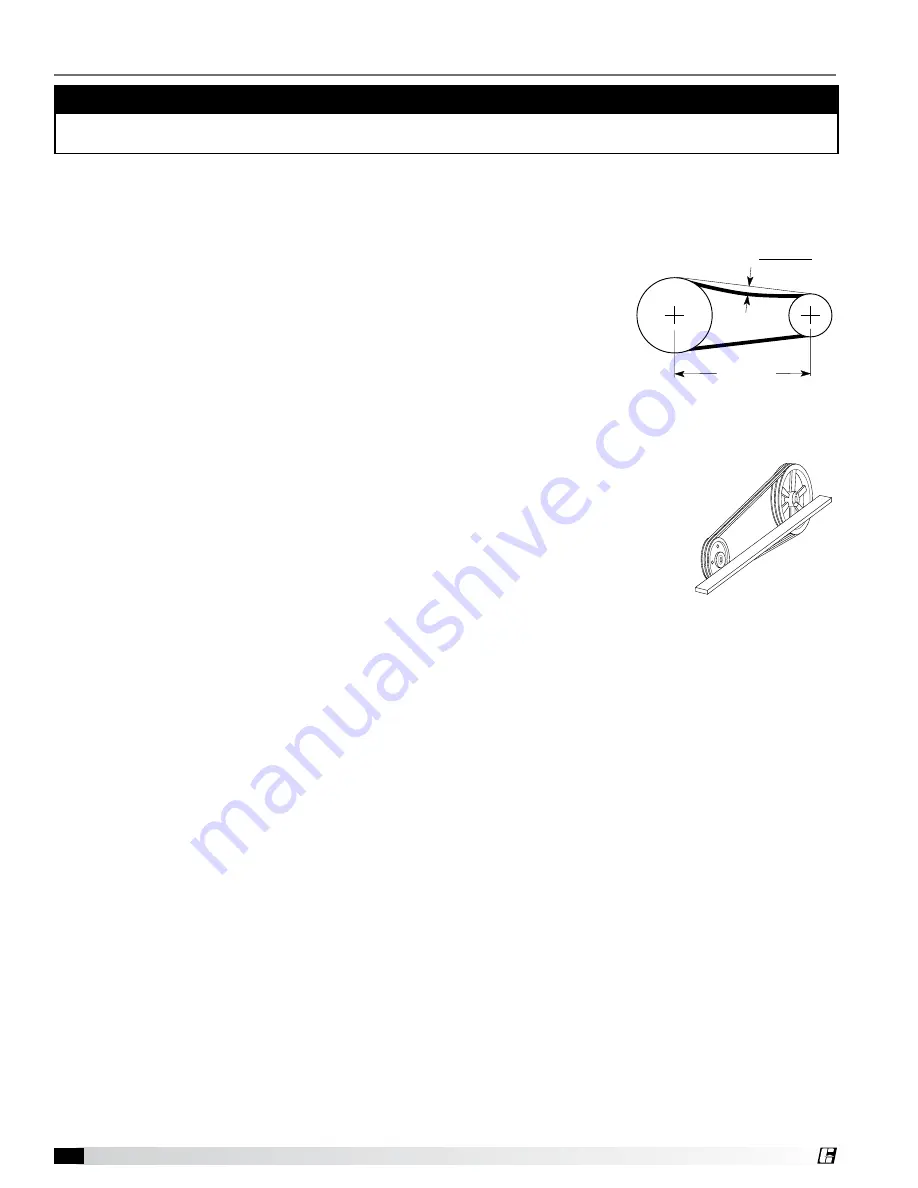
Laboratory Exhaust System
12
®
Maintenance
Once the fan has been put into operation, a periodic maintenance program should be set up to preserve the
reliability and performance of the fan. Items to be included in this program are:
• Belts
• Removal of dust and dirt
• Fasteners
• Fan shaft bearings
• Set Screws
• Vektor-HS nozzle bearings
• Motors
• Relubrication schedule
Belts
Premature belt failures are frequently caused by improper belt tension (either too
tight or too loose) or misaligned pulleys. The proper tension for operating a V-belt is
the lowest tension at which the belts will not slip at peak load conditions. For initial
tensioning, the proper belt deflection half-way between pulley centers is 1/64-inch for
each inch of belt span. For example, if the belt span is 64 inches, the belt deflection
should be one inch using moderate thumb pressure at midpoint of the drive.
Check belt tension two times during the first 24 hours of operation and periodically thereafter. To adjust belt tension,
simply loosen four fasteners (two on each side of the motor plate) and slide the motor plate away from the fan shaft
until proper belt tension is attained. On some fans, fasteners attaching the motor to the motor plate
must be loosened in order to adjust the belt.
It is very important that the drive pulleys remain in proper alignment after adjustments are made.
Misalignment of pulleys will result in premature belt wear, noise, vibration and power loss.
Fasteners and Set Screws
A periodic inspection should include checking all fasteners and set screws for tightness.
Particular attention should be paid to set screws attaching the wheel to the shaft.
Motors
Belt Drive:
Many fractional horsepower motors installed on the smaller fans are lubricated for life and require no further
attention. Motors supplied with grease fittings should be greased according to directions printed on the motor.
Direct Drive:
Motor bearings are lubed for life, with no maintenance required.
If motor or wheel needs to be serviced or replaced, use the lifting lugs to pull assembly cartridge out.
Removal of Dust and Dirt
Dirt clogs cooling openings on the motor housing, contaminates bearing lubricant, and collects on the impeller
causing severe imbalance if left unchecked. The exterior surface of the motor and impeller should be thoroughly
cleaned periodically. Use caution and do not allow water or solvents to enter the motor or bearings. Under no
circumstances should motors or bearings be sprayed with steam or water.
Fan Shaft Bearings
The bearings for Greenheck fans are carefully selected to match the maximum load and operating conditions of
the specific class, arrangement, and fan size. The instructions provided in this manual and those provided by the
bearing manufacturer will minimize any bearing problems. Bearings are the most critical moving part of the fan;
therefore, special care is required when mounting them on the unit and maintaining them. Locking collars and set
screws, in addition to fasteners attaching the bearing to the bearing plate must be checked for tightness. Greenheck
Fan Corporation recommends bearings to be relubricated quarterly at a minimum. All Vektor-H and Vektor-HS fans
use Mobil Mobilith SHC 100 synthetic grease conforming to NCGI Grade 2. Never mix greases made with different
bases as this will cause a breakdown of the grease and possible failure of the bearing. For specific information,
contact the factory representative or the fan system submittals.
• For conditions including temperatures, moisture, dirt or excessive vibration, consult the factory for a specific
lubrication interval for your application.
• Lubricant should be a high quality lithium complex synthetic grease conforming to NLGI Grade 2.
WARNING
Disconnect all electrical power to the fan and secure to the ‘OFF’ position prior to inspection or servicing. Failure to
comply with this safety precaution could result in serious injury or death.
Belt
Alignment
Deflection = Belt Span
64
Belt Span
Belt Tension