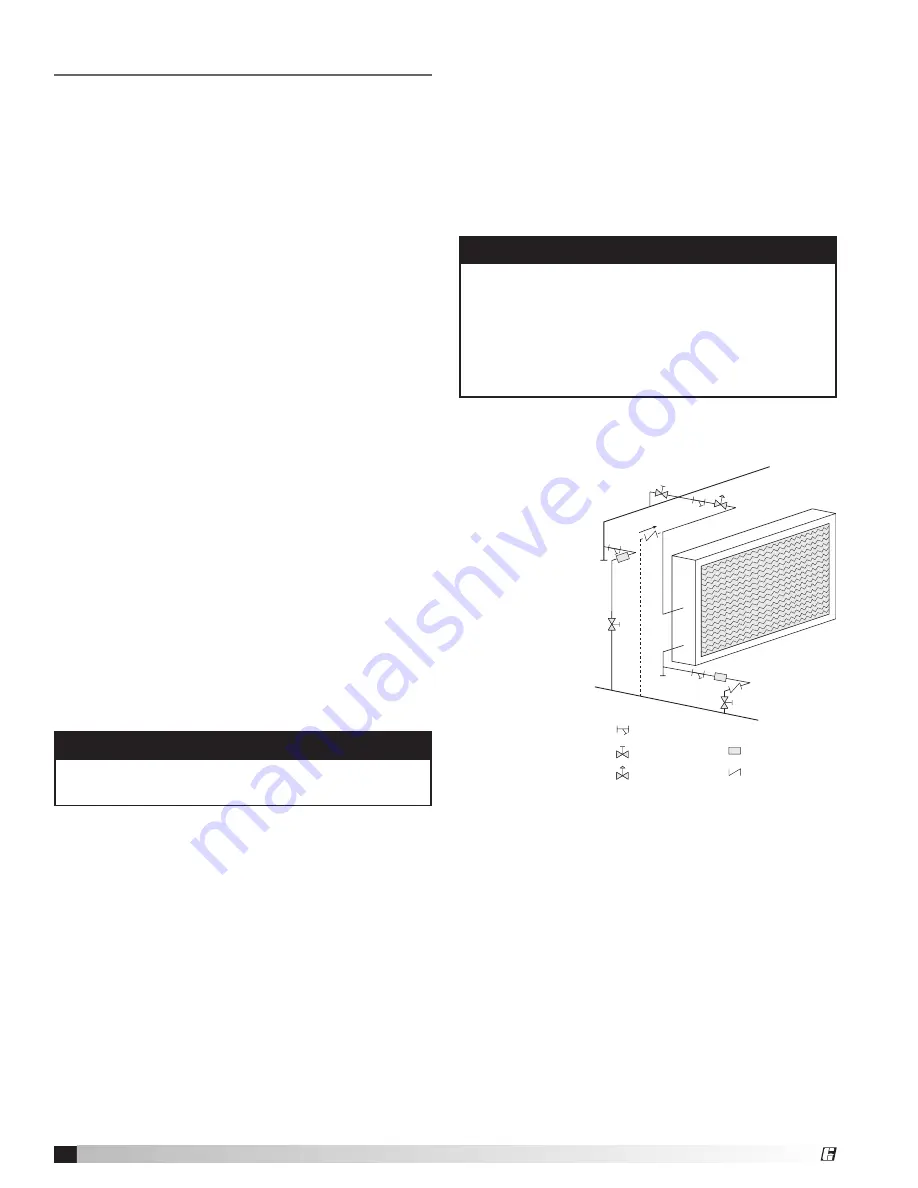
12
Model MSCF Modular Small Cabinet Fan
®
Hot Water and Chilled Water
1. Piping should be in accordance with accepted
industry standards. Pipework should be supported
independently of the coils. Water pipes are copper
with sweat connections. USE WET TOWEL TO
AVOID BURNING COIL CONNECTION GROMMETS.
When installing coupling, do not apply undue
stress to the connection extending through the
unit. Use a back-up pipe wrench to avoid breaking
the weld between coil connection and header.
2. Connect the water supply to the bottom
connection on the air-leaving side and the water
return to the top connection on the air-entering
side. The extra bottom connection can be used for
an auxiliary manual drain connection, and the extra
top connection may be used for an automatic air
vent, or the extra connections can be capped. To
ensure proper venting, an external air vent in the
piping is recommended. Connecting the supply
and/or return in any other manner will result in very
poor performance. CAP UNUSED CONNECTIONS.
3. The air vent at the uppermost point should be
temporarily opened during system start-up to
release all of the air from the coil. To maintain heat
transfer capacity, periodically vent any air in coil.
Vent to be located behind connections side access
door.
4. Water coils are not normally recommended for
use with entering air temperatures below 40°F.
No control system can be depended on to be
100% safe against freeze-up with water coils.
Glycol solutions or brines are the only safe media
for operation of water coils with low entering air
conditions.
5. Pipe sizes for the system must be selected on the
basis of the head (pressure) available from the
circulation pump. Piping should be in accordance
with accepted industry standards.
6. For chilled water coils, the condensate drain
pipe should be sized adequately to ensure the
condensate drains properly. See Drain Pan Traps
section and related drawing.
Direct Expansion (DX) Coils
1. Piping should be in accordance with accepted
industry standards. Pipework should be supported
independently of the coils. Undue stress should not
be applied at the connection to coil headers.
2. The condensate drain pipe should be sized
adequately to ensure the condensate drains
properly. See Drain Pan Traps and related drawing.
Start-Up of Coil Module
WARNING
Continuous water circulation through the coil at all
times is highly recommended.
WARNING
Standard unit insulation of 1.5 lbs. density has an
insulation R-value of 3.7.
For applications where the unit discharge
temperatures are below 55°F and the unit is installed
in a warm, humid environment, additional insulation
may need to be applied to the exterior of the unit to
prevent condensation.
3. When connecting suction and liquid connections,
make sure the coil is free from all foreign material.
Make sure all joints are tight and free of leakage.
4. Greenheck does not supply compressor or
condensing units, for further instruction on DX coil
installation and operation contact your compressor
and/or condenser manufacturer.
DXI coils have dual connections and should be used
with two compressors.
Steam Coils
Application Recommendations
Satisfactory operation and
service life are best
ensured when coils
are installed with
proper piping,
trap and support
arrangement.
The following
notes and
drawing are
recommended
for the coil unit
installation and
operation.
General
1. Provide
separate
supports and
hangers for the
unit and the piping.
2. Be certain that adequate piping flexibility is
provided. Stresses resulting from expansion of
closely coupled piping and coil arrangement can
cause serious damage.
3. Standard steam coils are pitched in the casings
when installed for horizontal airflow. The casing
must be level after the unit is installed for proper
condensate drainage. If condensate is not
removed, the coil will suffer from water hammering
and will have a shortened life. On vertical airflow
applications, the coils must be pitched when
installed.
4. Do not reduce pipe size at the coil return
connection. Carry return connection size through
the dirt pocket, making the reduction at the branch
leading to the trap.
Steam Coil Piping
Steam Main
Return Main
Strainer
Gate Valve
Control Valve
Modulating Two-Position
Check Valve
Vacuum Breaker
Float & Thermostat Trap