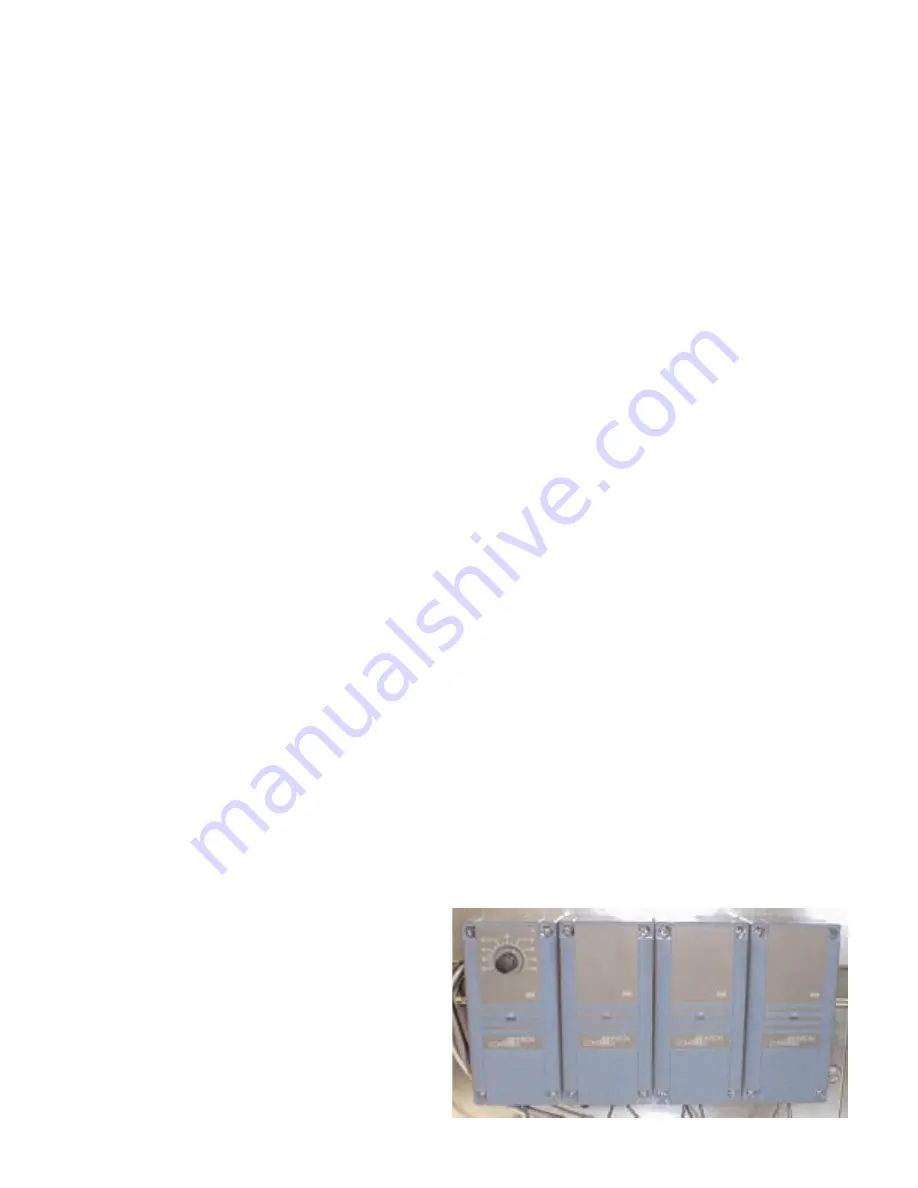
15
Sequence of Operation
Control Center
1. Turn the fan switch to the “on” position (If summer/off/winter switch is used, turn to “winter” position).
2. Damper actuator is energized (Optional).
3. Supply Starter is energized. Supply fan runs. If an exhaust fan is included, it must run before the supply fan.
4. Turn the heater switch “on” (if using a separate switch from fan).
• If an off delay timer is included (1 to 120 minutes), the fan will continue to run after the switch is turned off.
• If freeze protection is included, a timer (1 to 5 minutes) and a discharge temperature sensor are included. The
unit must heat up to the discharge sensor’s setting before the timer runs out or the supply fan will shut down.
Heater
5. Open all manual gas valves.
6. High temperature limit is normally closed (automatic reset).
7. Optional inlet air sensor contact is closed (normally open).
8. If the temp control system senses that the discharge temperature is below the set point of the temperature
selector, the system will energize the ignition control.
Note: If the discharge is above the set point, the heater will not run.
9. When the ignition control is energized, sparking will start at the pilot. At the same time the first operator (pilot
gas) of the gas valve allows gas to flow to the pilot burner. In a few seconds the pilot should be established
and proven. This will stop the sparking and open the second operator (main gas) of the gas valve, allowing gas
to flow to the main burner.
Natural Gas
- If the pilot is not established and proven after 70 seconds, the ignition controller will pause for 5
minutes with the gas valve closed and no spark and restart the ignition sequence again. After going through
this trial/wait sequence 3 times, the control will wait an additional 1 hour and repeat the process again (if
necessary).
LP Gas
- If the pilot is not established and proven after 70 seconds, the ignition control will lockout. The pilot
gas valve will close and sparking will stop. The system will not attempt to light until the power to the heater is
turned off and back on.
10A. Elect Mod: The maxitrol system will then modulate the main burner gas from 100% down to 40% as needed.
If the burner remains on low fire for an short amount of time, the heater will be shut off and restarted as
necessary.
10B. Staged: The stage control will energize the stages as necessary to maintain the discharge setting or satisfy
the room thermostat. For example a 3 stage discharge control with two furnaces will fire the first furnace at
50% (stage 1) when there is a call for heat. If the discharge setting is not satisfied, the first furnace will then fire
at 100% (stage 2). If still not satisfied, the second furnace will also fire at 100% (stage 3). When the discharge
temperature approaches the set point, the stages de-energize in reverse order. The first stage will stay on until
the discharge temperature is reached.
Settings for Staged Discharge Temperature Controls
The furnace stage controls are located in the
control center. For units with room thermostats
these controls are not included. They are modular
controls that plug into each other. The discharge
temperature setting is located on the control
furthest left. The stage differential settings are
preset at the factory and should not need
adjustment. See the literature provided with the
controls for further information.
Typical 4-Stage Discharge Temperature Control