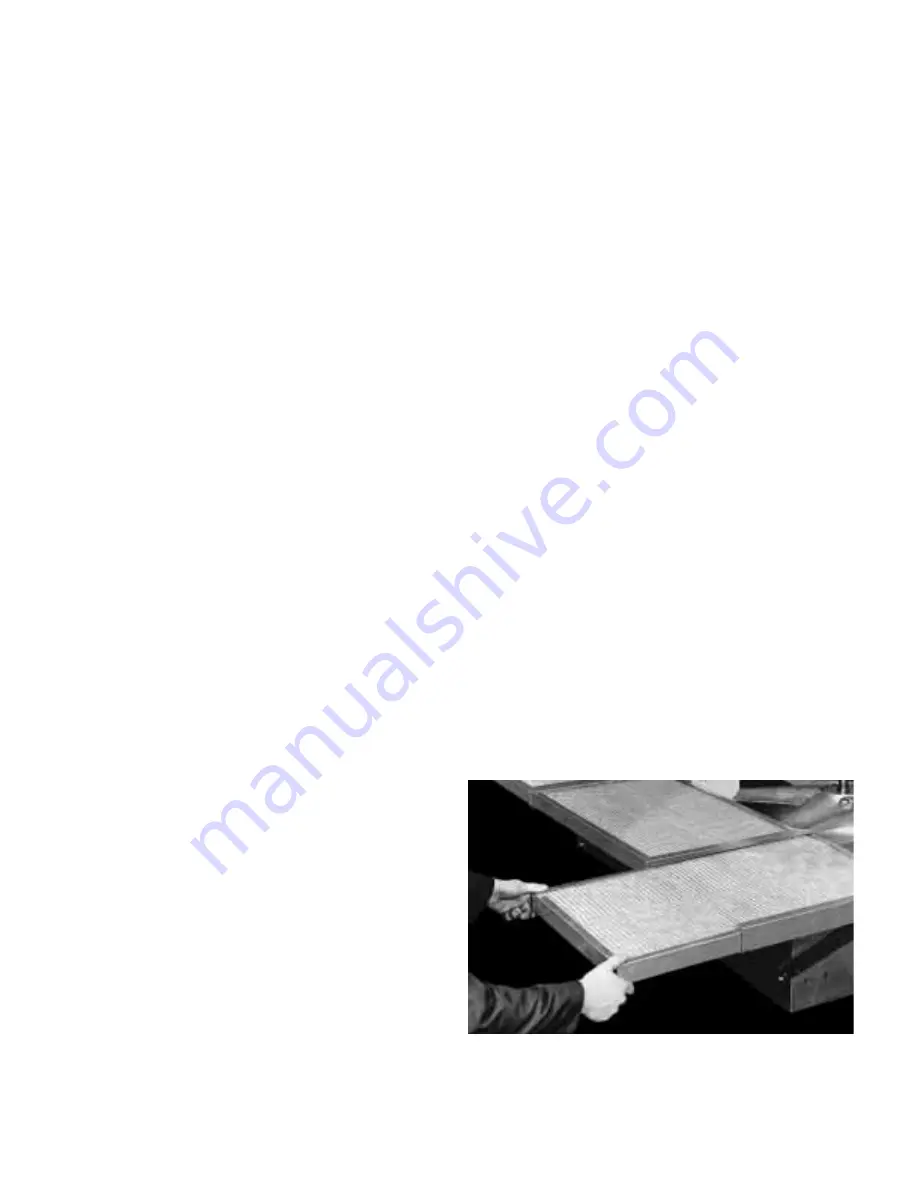
BEARINGS (For belt drive fans only)
Bearings are the most critical moving part of the fan and should be inspected at periodic intervals. Locking collars
and set screws, in addition to fasteners attaching the bearings to the bearing plate, must be checked for tightness. In a
clean environment and temperatures above 32°F./below 200° F., fan shaft bearings with grease fittings
should be lubricated semi-annually using a high quality lithium based grease. If unusual environmental conditions exist
temperatures below 32°F./above 200°F., moisture or contaminants, more frequent lubrication is required.
With the unit running, add grease very slowly with a manual grease gun until a slight bead of grease forms at
the seal. Be careful not to unseat the seal by over lubricating or using excessive pressure. Bearings without grease fittings are
lubricated for life.
FASTENERS AND SET SCREWS
Any fan vibration has a tendency to loosen mechanical fasteners. A periodic inspection should include checking all
fasteners and set screws for tightness. Particular attention should be paid to set screws attaching the propeller to the
shaft and the shaft to the bearings. Loose bearing set screws will lead to premature failure of the fan shaft.
LUBRICATION
Refer to the paragraph on bearings for bearing lubrication. Many fractional horsepower motors installed on the smaller fans are
lubricated for life and require no further attention. Motors equipped with oil holes should be oiled in accordance with the
manufacturer's instructions printed on the motor. Use a high grade SAE 20 machine oil and use caution not to over lubricate.
Motors supplied with grease fittings should be greased according to directions printed on the motor.
REMOVAL OF DUST AND DIRT
Dirt clogs cooling openings on the motor housing, contaminates bearing lubricant and collects on propeller blades
causing severe imbalance if left unchecked. The exterior surface of the motor, fan panel and entire propeller should be
thoroughly cleaned periodically. Use caution and do not allow water or solvents to enter the motor or bearings. Under no
circumstances should motors or bearings be sprayed with steam or water.
DAMPER INSPECTION AND SERVICE
If an optional tall base with damper is supplied, access to the optional dampers and actuators is provided by a removable door.
Simply release the two cam latches and slide the damper out for inspection, cleaning or service.
For fan sizes 24 through 36 supplied without a tall base, the entire unit must be lifted off the roof curb for access to the damper.
For fan sizes 42 through 72 suppled without a tall base, access to the damper is made by removing one end birdscreen or filter
and working on the damper from above.
SEE WARNING ON
PAGE 2
.
FILTER MAINTENANCE (FILTERED SUPPLY FANS)
Aluminum mesh filters should be cleaned on a regular basis
for optimum fan efficiency. The frequency of cleaning
depends upon the cleanliness of the incoming air.
To remove filters on fan sizes 24 to 30, first remove the hood
as shown in fig.1. The filters can then be pulled from the
slide-out racks (shown in photo). On fan sizes 36 to 60,
access panels on the end panels are provided which allow
the filters to be removed without removing the hood.
Filters should be washed with a mild detergent in warm
water. After the filters are dry, an adhesive spray available at
most filter distributors may be applied to increase filter
efficiency.
Sliding filter out of filter rack.