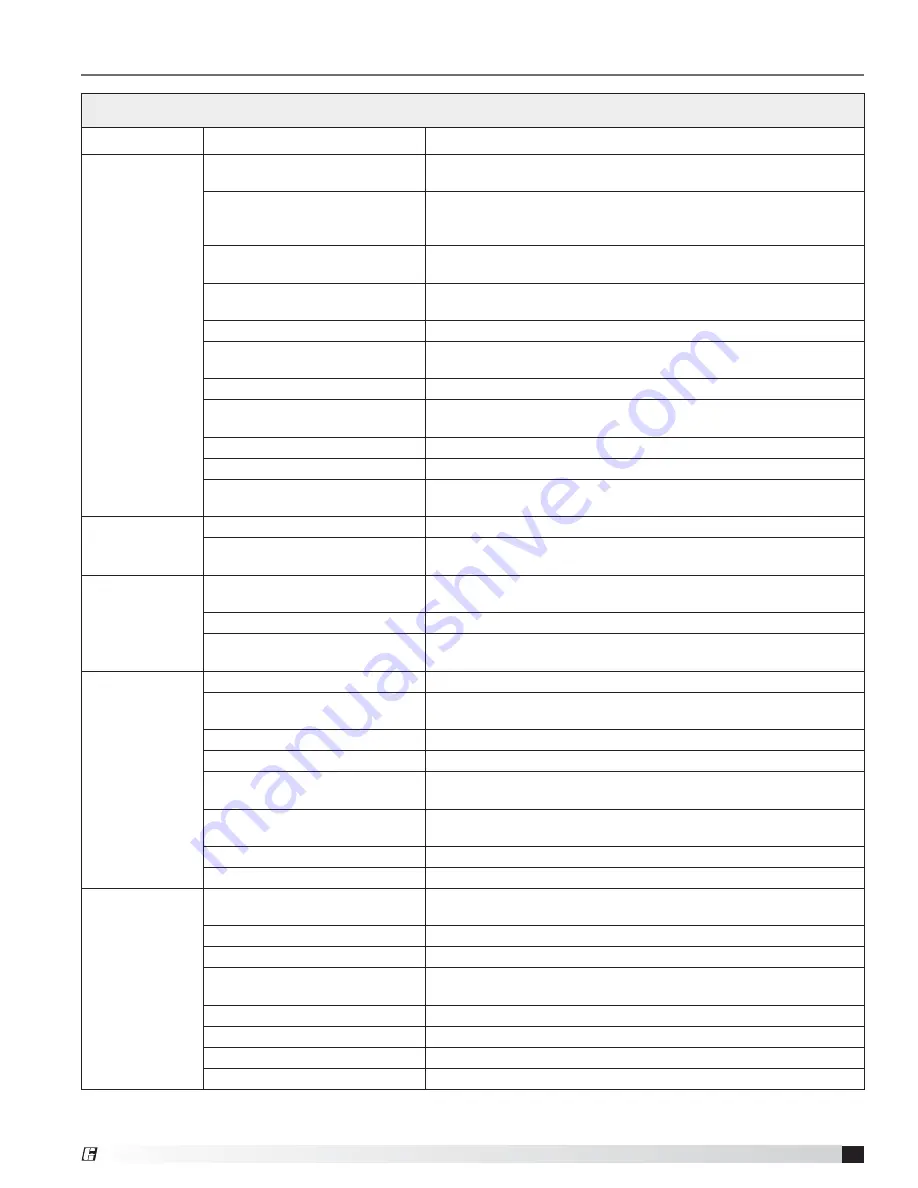
9
Downblast Centrifugal Roof Exhaust Fans
WARNING: Before taking any corrective action, make certain unit is not capable of operation during repairs.
PROBLEM
CAUSE
CORRECTIVE ACTION
Excessive noise
or vibration
Wheel rubbing inlet
Adjust wheel and/or inlet cone. Tighten wheel hub or bearing
collars on shaft.
V-belt drive
Tighten pulleys on motor/fan shaft. Adjust belt tension. Align
pulleys properly, see page 6, Figure 9-10. Replace worn belts or
pulleys.
Bearings
Replace defective bearing(s). Lubricate bearings. Tighten collars
and fasteners.
Wheel unbalance
Clean all dirt off wheel. Check wheel balance, rebalance in place if
necessary.
Belts too tight or too loose
Adjust tension, see page 7, Figure 12a-b.
Wheel improperly aligned and
rubbing
Center wheel on inlet, see page 6, Figure 7.
Loose drive or motor pulleys
Align and tighten. See “Pre-Starting Checks”, see page 6.
Foreign objects in wheel or
housing
Remove objects, check for damage or unbalance.
Fan base not securely anchored
Secure properly.
Motor hood loose and rattling
Tighten screws securing motor hood.
Defective or loose motor
bearings
Replace motor with same frame size, RPM-HP.
High horsepower
Fan
Check rotation of wheel, see page 6, Figure 8. Reduce fan speed.
Duct system
Resize ductwork. Check proper operation of face and bypass
dampers. Check filters and access doors.
Fan does
not operate
Electrical supply
Check fuses/circuit breakers. Check for switches off. Check for
correct supply voltage.
Drive
Check for broken belts. Tighten loose pulleys.
Motor
Assure motor is correct horsepower and not tripping overload
protector.
Motor overloads
or overheats
Lubrication
Check for excessive or insufficient grease in the bearing.
Mechanical
Replace damaged bearing. Relieve excessive belt tension. Align
bearings. Check for bent shaft.
Belt slippage
Adjust tension or replace bad belts, see page 6-7.
Over/Under line voltage
Contact power company.
Incorrect wheel rotation
Check motor wiring (page 4) verify motor is wired for correct
rotation.
Wheel RPM too high
Check drives or slow down fan by opening variable pitch pulley on
motor shaft.
Undersized motor
Check motor ratings with catalog speed and air capacity chart.
Motor wired incorrectly
Check motor wiring to wiring diagram located on fan motor.
Reduced airflow
System resistance too high
Check system: Proper operation of backdraft or control dampers,
obstruction in ductwork, clean dirty filters.
Unit running backwards
Correct as shown on page 6, Figure 8.
Excessive dirt buildup on wheels
Clean wheel.
Improper wheel alignment
Center wheel on inlets, see Pre-Starting checks on page 6,
Figure 7.
Dampers closed
Inspect and repair.
Blocked duct/clogged filter
Clean or replace.
Belt slippage
Replace and adjust tension.
Speed too slow
Check for correct drives.
Troubleshooting
®