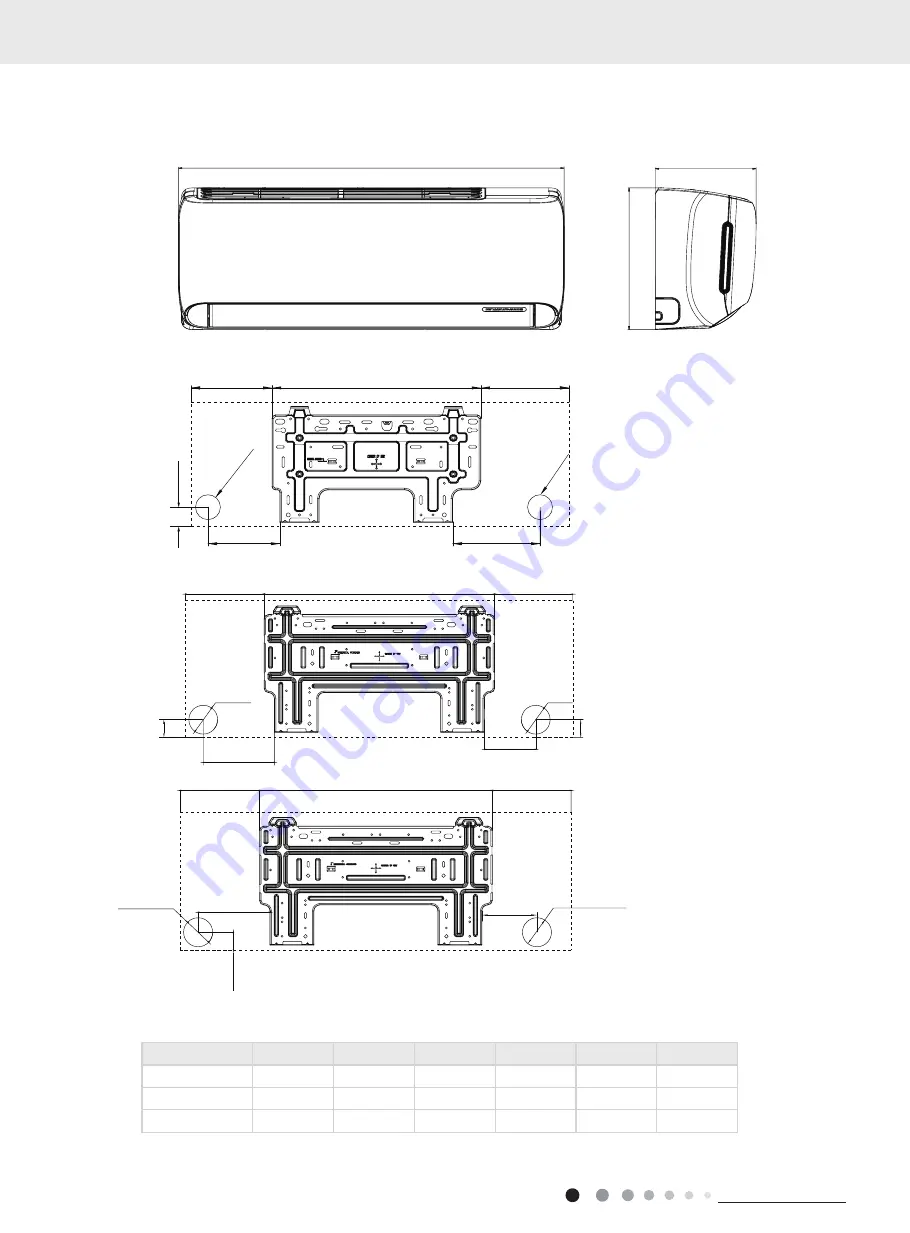
18
Technical Information
Service Manual
3. Outline Dimension Diagram
3.1 Indoor Unit
Model
W
H
D
W1
W2
W3
ATC
32 7/8
10 53/64
7 7/8
7 3/64
18 5/32
7 11/16
ATD
37 1/8
13 7/64
9 11/16
7 35/64
22 3/32
7 31/64
ATE
42 7/16
13 7/64
9 11/16
10 3/16
22 3/32
10 5/32
Unit:inch
Unit:inch
W
W1
W2
W3
ATA / ATB
D
H
6 52/64
W1
W2
W3
ATE
9 29/64
Ø2 49/64
Ø2 49/64
Ø2 49/64
8 7/64
1
11
/1
6
1
11
/1
6
1
11
/1
6
Ø2 49/64
W1
W2
W3
ATD
5 7/16
W
W1
W2
W3
ATA / ATB
D
H
6 52/64
W1
W2
W3
ATE
9 29/64
Ø2 49/64
Ø2 49/64
Ø2 49/64
8 7/64
1
11
/1
6
1
11
/1
6
1
11
/1
6
Ø2 49/64
W1
W2
W3
ATD
5 7/16
W
W1
W2
W3
ATA / ATB
D
H
6 17/64
1
11
/1
6
7 3/4
Ø21
11
/64
Ø21
11
/64
Ø2
11
/64
Ø2
11
/64
W2
W3
W1
2 61/64
2 61/64
ATC
Summary of Contents for N00600
Page 1: ...Service Manual Change for life GREE ELECTRIC APPLIANCES INC OF ZHUHAI 4LIV09 24 Models ...
Page 93: ...90 Installation and Maintenance Service Manual INTENTIONALLY BLANK ...
Page 95: ...92 Installation and Maintenance Service Manual INTENTIONALLY BLANK ...
Page 96: ...93 Installation and Maintenance Service Manual INTENTIONALLY BLANK ...