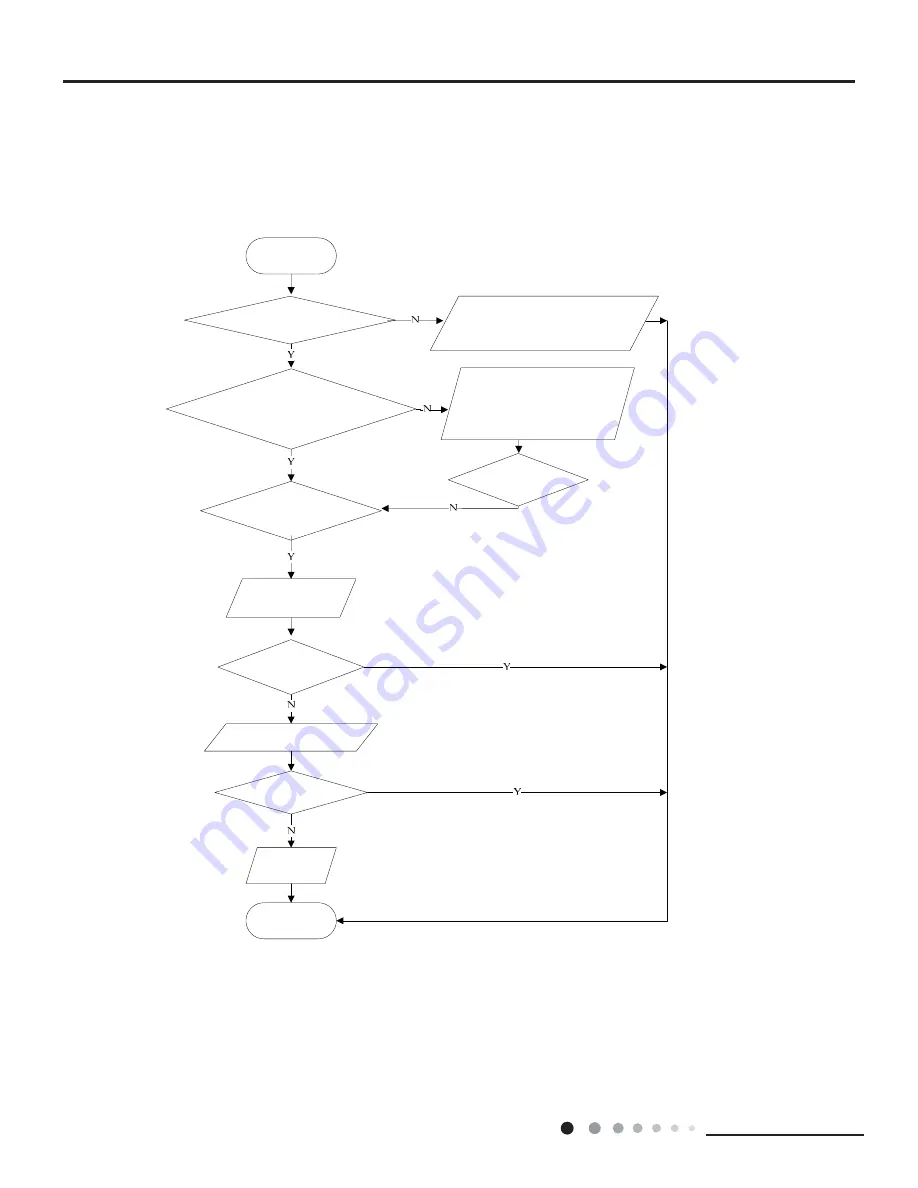
54
Installation and Maintenance
Service Manual
9.Start-up failure (LC) (AP1 below means control board of outdoor unit)
Main detection points:
ƽ
,IWKHFRPSUHVVRUZLULQJLVFRUUHFW"
ƽ
,IWKHVWRSWLPHRIFRPSUHVVRULVVXI¿FLHQW"
ƽ
,IWKHFRPSUHVVRULVGDPDJHG"
ƽ
,IWKHUHIULJHUDQWFKDUJLQJDPRXQWLVWRRPXFK"
If the stop time of compressor
is more than 3min?
The stop time is not sufficient and
the high and low pressure of system
is not balanced , please start the unit
after 3min
If the compressor wire
COMP(UVW) is well connected and
connection sequence is correct?
Check the connection situation
of outdoor mainboard AP1 and
compressor COMP, and the
connect it according to wiring
diagram
If the refrigerant charging
amount is too much?
Does the unit
start up normally?
Charge the refrigerant
according to service
manual
Does the unit
start up normally?
Replace outdoor
mainboard AP1
Is the malfunction
eliminated?
Replace the
compressor
End
Turn on the unit
Summary of Contents for GWH18RC-K3DNA2C
Page 66: ...63 Installation and Maintenance Service Manual 2 Models GWH18RC K3DNA8C I GWH18RC K3DNA6C I...
Page 74: ...71 Installation and Maintenance Service Manual 10 2 Outdoor Unit 1 Model GWH18RC K3DNA3C O...
Page 76: ...73 Installation and Maintenance Service Manual 2 Model GWH18RC K3DNA8C O...
Page 78: ...75 Installation and Maintenance Service Manual 3 Model GWH24RD K3DNA3C O...
Page 80: ...77 Installation and Maintenance Service Manual 4 Model GWH24RD K3DNA8C O...