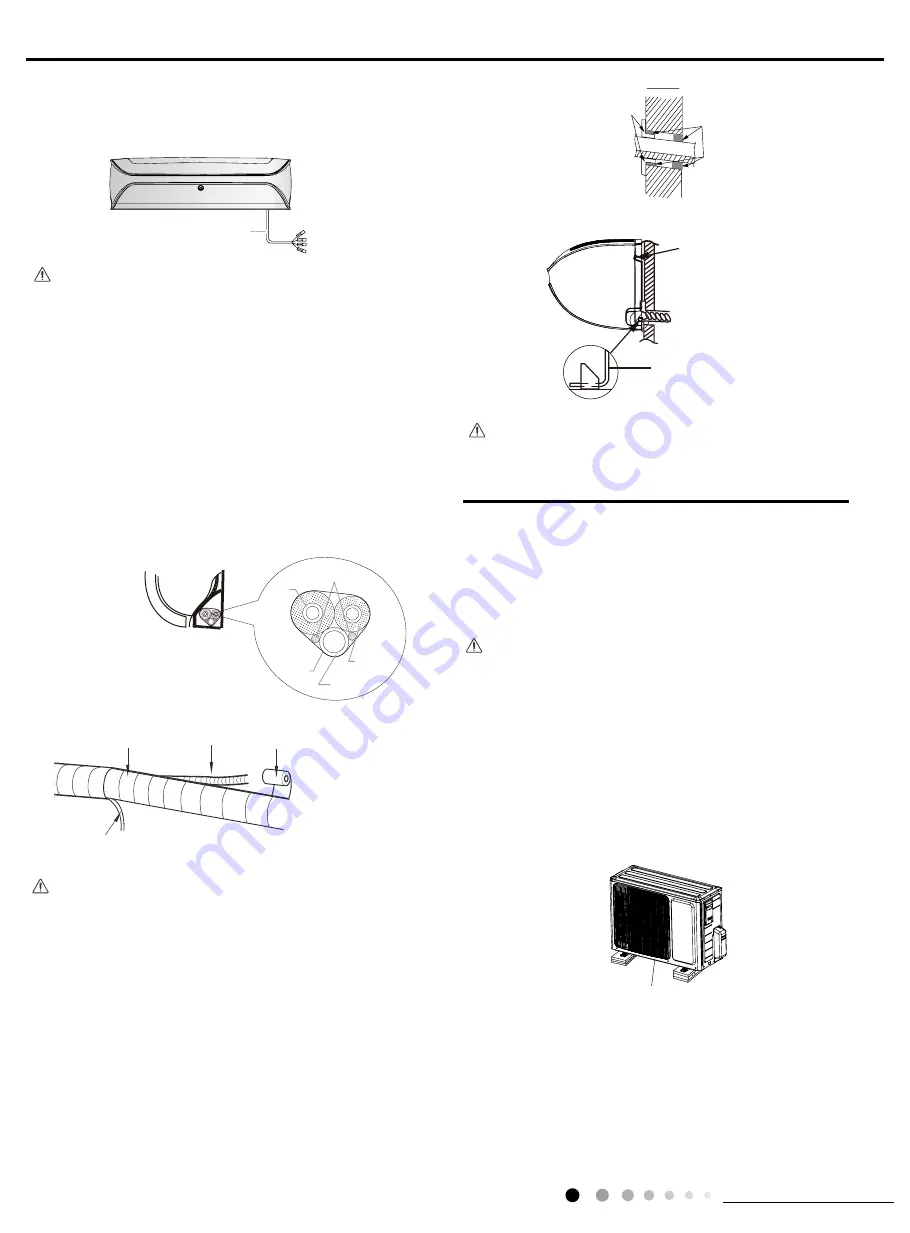
36
Installation and Maintenance
Service Manual
upper hook
lower hook of
wall-mounting frame
Indoor unit
Gas
pipe
Indoor and
outdoor power cord
Liquid
pipe
Drain hose
Band
Drain hose Band
Connection pipe
Indoor power cord
If the length of power connection wire is insufficient, please
contact the supplier for a new one. Avoid extending the wire by
yourself.
(1) The power cord and control wire can't be crossed or
winding.
(2) The drain hose should be bound at the bottom.
Do not bend the drain hose too excessively in order to prevent
blocking.
7. Connect Wire of Indoor Unit
The connection wire of indoor unit has been assembled before
ex-factory, so you only need to check if it is loose before
connecting wire.
8. Bind up Pipe
(1) Bind up the connection pipe, power cord and drain hose
with the band.(As show in Fig.12)
(2) Reserve a certain length of drain hose and power cord
for installation when binding them. When binding to a certain
degree, separate the indoor power and then separate the drain
hose.(As show in Fig.13)
(3) Bind them evenly.
(4) The liquid pipe and gas pipe should be bound separately at
the end.
9. Hang the Indoor Unit
(1) Put the bound pipes in the wall pipe and then make them
pass through the wall hole.
(2) Hang the indoor unit on the wall-mounting frame.
(3) Stuff the gap between pipes and wall hole with sealing gum.
(4) Fix the wall pipe.(As show in Fig.14)
(5) Check if the indoor unit is installed firmly and closed to the
wall.(As show in Fig.15)
Note:
Note:
Note:
Indoor
Outdoor
Wall pipe
Sealing gum
Fig.12
Fig.13
Fig.14
Fig.15
Fig.16
connection cable
Fig.11
(1) Take sufficient protective measures when installing the
outdoor unit.
(2) Make sure the support can withstand at least four times the
unit weight.
(3) The outdoor unit should be installed at least 3cm above the
floor in order to install drain joint.(As show in Fig.16)
(4) For the unit with cooling capacity of 2300W~5000W, 6
expansion screws are needed; for the unit with cooling capacity
of 6000W~8000W, 8 expansion screws are needed; for the
unit with cooling capacity of 10000W~16000W, 10 expansion
screws are needed.
Note:
8.6 Installation of Outdoor unit
1. Fix the Support of Outdoor Unit(Select it according to
the actual installation situation)
(1) Select installation location according to the house structure.
(2) Fix the support of outdoor unit on the selected location with
expansion screws.
2. Install Drain Joint(Only for Cooling and Heating Unit)
(1) Connect the outdoor drain joint into the hole on the chassis.
(2) Connect the drain hose into the drain vent.(As show in
Fig.17)
At least 3cm above the floor