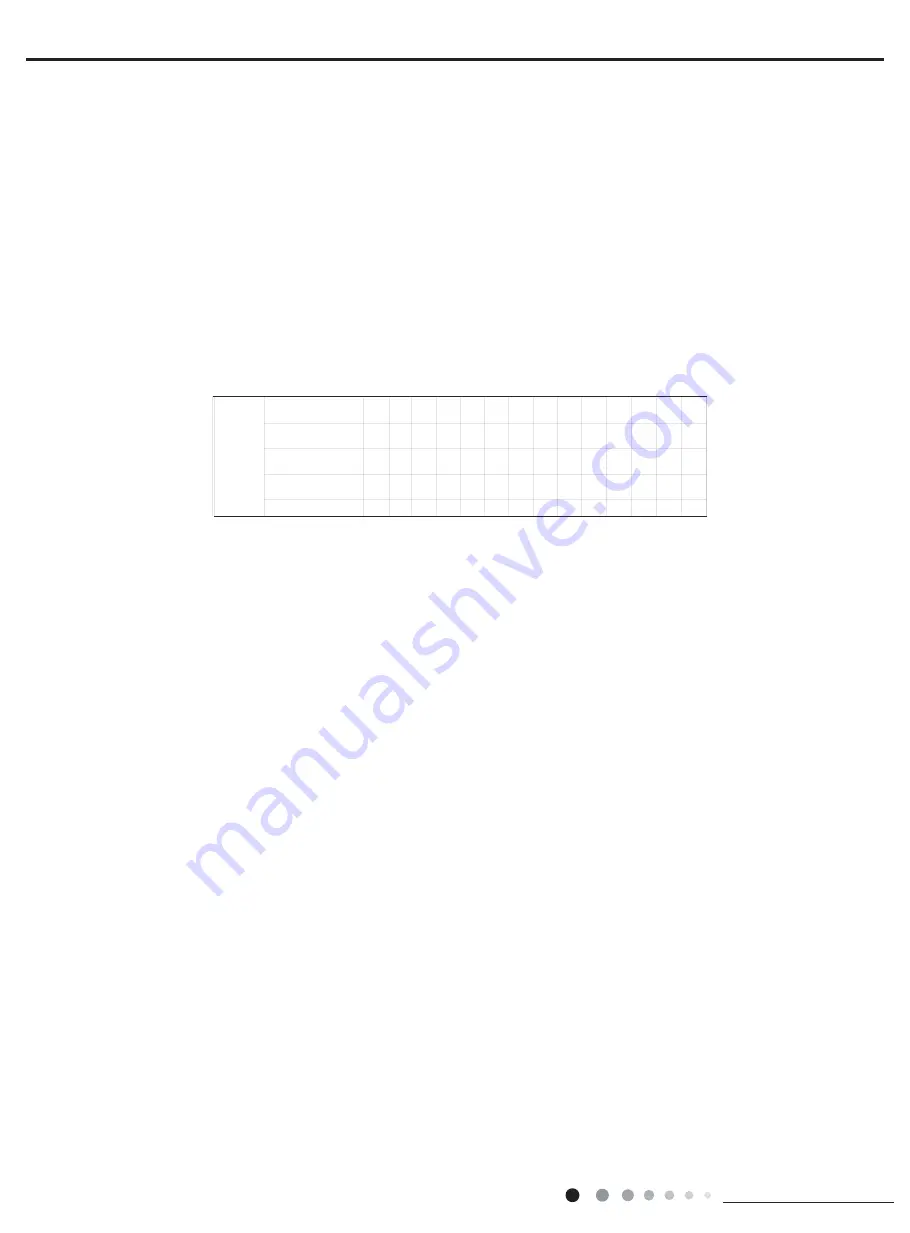
30
Installation and Maintenance
Service Manual
Safety Operation of Flammable Refrigerant
Qualification requirement for installation and maintenance man
●All the work men who are engaging in the refrigeration system should bear the valid certification awarded by the
authoritative organization and the qualification for dealing with the refrigeration system recognized by this industry. If it needs
other technician to maintain and repair the appliance, they should be supervised by the person who bears the qualification for
using the flammable refrigerant.
●It can only be repaired by the method suggested by the equipments manufacturer.
Installation notes
●The air conditioner is not allowed to use in a room that has running fire (such as fire source,working coal gas ware,
operating heater).
●It is not allowed to drill hole or burn the connection pipe.
●The air conditioner must be installed in a room that is larger than the minimum room area.
The minimum room area is shown on the nameplate or following table a.
●Leak test is a must after installation.
table a - Minimum room area(m
2
)
Maintenance notes
●Check whether the maintenance area or the room area meet the requirement of the nameplate.
— Its only allowed to be operated in the rooms that meet the requirement of the nameplate.
●Check whether the maintenance area is well-ventilated.
— The continuous ventilation status should be kept during the operation process.
●Check whether there is fire source or potential fire source in the maintenance area.
— The naked flame is prohibited in the maintenance area; and the “no smoking” warning board should be hanged.
●Check whether the appliance mark is in good condition.
— Replace the vague or damaged warning mark.
Welding
●If you should cut or weld the refrigerant system pipes in the process of maintaining, please follow the steps as below:
a. Shut down the unit and cut power supply
b. Eliminate the refrigerant
c. Vacuuming
d. Clean it with N
2
gas
e. Cutting or welding
f. Carry back to the service spot for welding
●Make sure that there isnt any naked flame near the outlet of the vacuum pump and its well-ventilated.
●The refrigerant should be recycled into the specialized storage tank.
Filling the refrigerant
●Use the refrigerant filling appliances specialized for R32. Make sure that different kinds of refrigerant wont contaminate with
each other.
●The refrigerant tank should be kept upright at the time of filling refrigerant.
●Stick the label on the system after filling is finished (or havent finished).
●Dont overfilling.
●After filling is finished, please do the leakage detection before test running; another time of leak detection should be done
when its removed.
Safety instructions for transportation and storage
●Please use the flammable gas detector to check before unload and open the container.
●No fire source and smoking.
●According to the local rules and laws.
Charge amount (kg) ≤1.2 1.3 1.4 1.5 1.6 1.7 1.8 1.9 2 2.1 2.2 2.3 2.4 2.5
4
4
4
4 14.5 16.8 19.3 22 24.8 27.8 31 34.3 37.8 41.5 45.4 49.4 53.6
5.2 6.1
7 7.9 8.9 10 11.2 12.4 13.6 15 16.3 17.8 19.3
4.2 4.6
5 5.5
6
4
4
4
4
4
floor location
wall mounted
window mounted
ceiling mounted
Minimum
room
2
area( m )
4
4
4
4
4
4
4
4
4
4
4
4
4
4
4
4