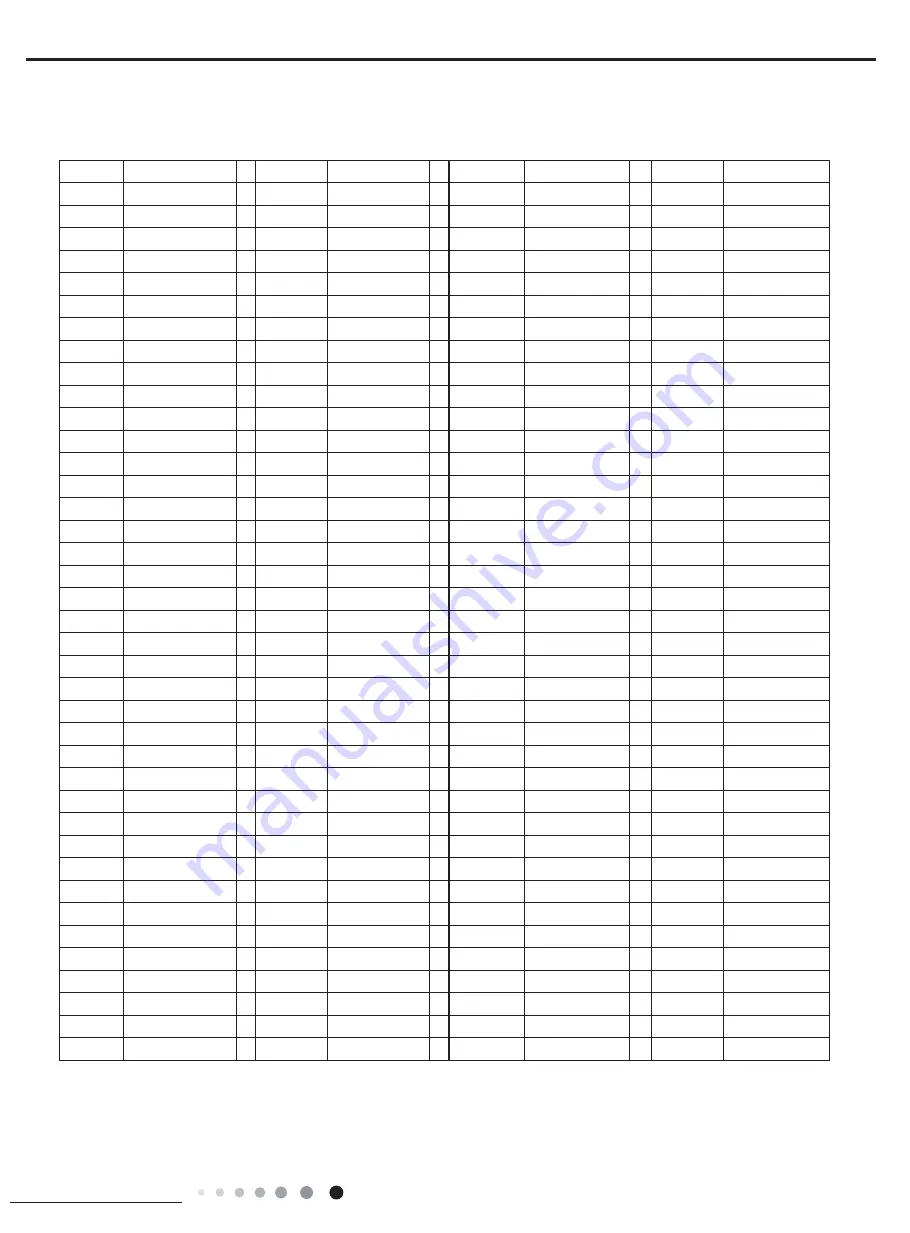
79
Installation and Maintenance
Service Manual
Appendix 4: List of Resistance for Temperature Sensor
Resistance Table of Ambient Temperature Sensor for Indoor and Outdoor Units(15K)
Temp(
o
C)
Resistance(kΩ)
Temp(
o
C)
Resistance(kΩ)
Temp(
o
C)
Resistance(kΩ)
Temp(
o
C)
Resistance(kΩ)
-19
138.1
20
18.75
59
3.848
98
1.071
-18
128.6
21
17.93
60
3.711
99
1.039
-17
121.6
22
17.14
61
3.579
100
1.009
-16
115
23
16.39
62
3.454
101
0.98
-15
108.7
24
15.68
63
3.333
102
0.952
-14
102.9
25
15
64
3.217
103
0.925
-13
97.4
26
14.36
65
3.105
104
0.898
-12
92.22
27
13.74
66
2.998
105
0.873
-11
87.35
28
13.16
67
2.896
106
0.848
-10
82.75
29
12.6
68
2.797
107
0.825
-9
78.43
30
12.07
69
2.702
108
0.802
-8
74.35
31
11.57
70
2.611
109
0.779
-7
70.5
32
11.09
71
2.523
110
0.758
-6
66.88
33
10.63
72
2.439
111
0.737
-5
63.46
34
10.2
73
2.358
112
0.717
-4
60.23
35
9.779
74
2.28
113
0.697
-3
57.18
36
9.382
75
2.206
114
0.678
-2
54.31
37
9.003
76
2.133
115
0.66
-1
51.59
38
8.642
77
2.064
116
0.642
0
49.02
39
8.297
78
1.997
117
0.625
1
46.6
40
7.967
79
1.933
118
0.608
2
44.31
41
7.653
80
1.871
119
0.592
3
42.14
42
7.352
81
1.811
120
0.577
4
40.09
43
7.065
82
1.754
121
0.561
5
38.15
44
6.791
83
1.699
122
0.547
6
36.32
45
6.529
84
1.645
123
0.532
7
34.58
46
6.278
85
1.594
124
0.519
8
32.94
47
6.038
86
1.544
125
0.505
9
31.38
48
5.809
87
1.497
126
0.492
10
29.9
49
5.589
88
1.451
127
0.48
11
28.51
50
5.379
89
1.408
128
0.467
12
27.18
51
5.197
90
1.363
129
0.456
13
25.92
52
4.986
91
1.322
130
0.444
14
24.73
53
4.802
92
1.282
131
0.433
15
23.6
54
4.625
93
1.244
132
0.422
16
22.53
55
4.456
94
1.207
133
0.412
17
21.51
56
4.294
95
1.171
134
0.401
18
20.54
57
4.139
96
1.136
135
0.391
19
19.63
58
3.99
97
1.103
136
0.382