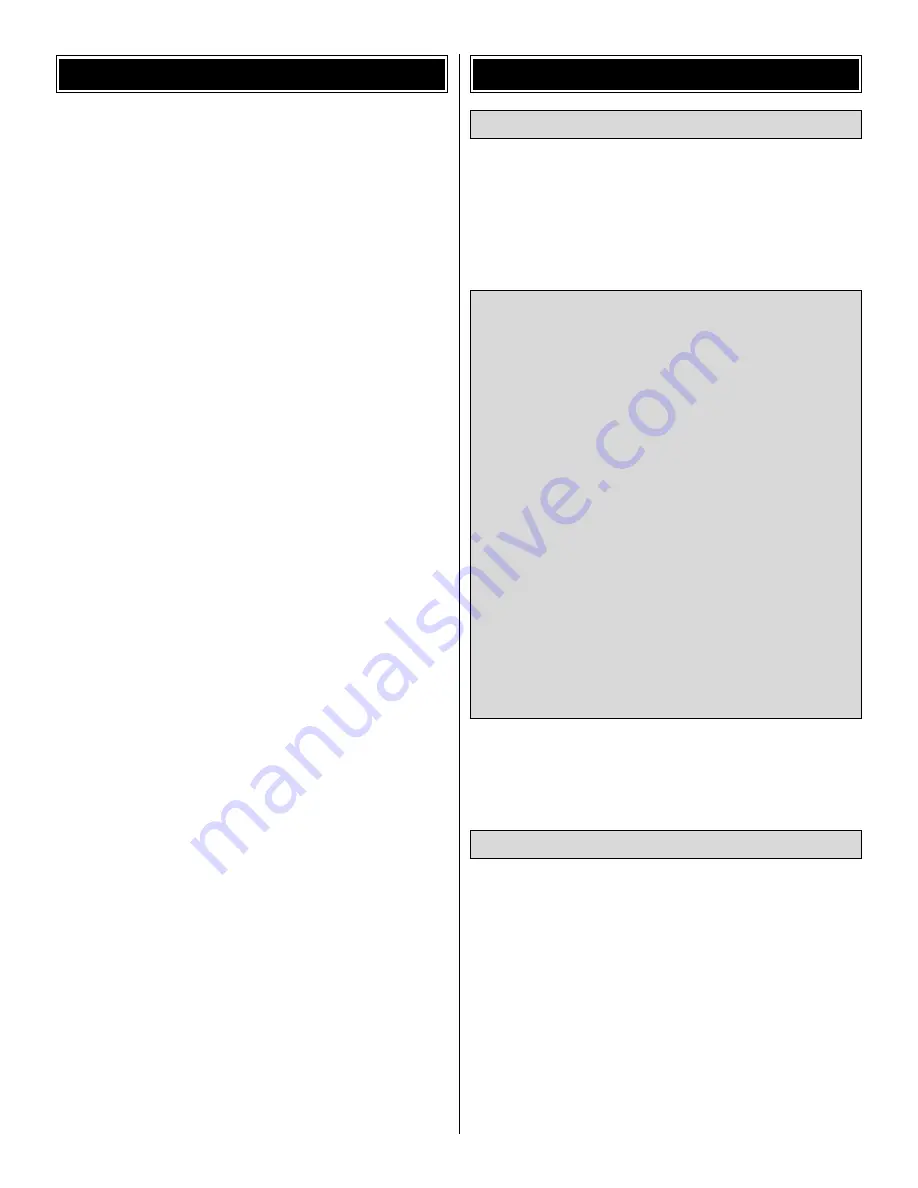
❏
1. Fuelproof all areas exposed to fuel or exhaust residue
such as the cowl mounting blocks, wing saddle area, etc.
❏
2. Check the C.G. according to the measurements
provided in the manual.
❏
3. Be certain the battery and receiver are securely
mounted in the fuse. Simply stuffing them into place
with foam rubber is not sufficient.
❏
4. Extend your receiver antenna and make sure it is in
the antenna tube.
❏
5. Balance your model laterally.
❏
6. Use thread-locking compound to secure critical
fasteners such as the set screws that hold the wheel
axles to the struts, screws that hold the carburetor arm
(if applicable), screw-lock pushrod connectors, etc.
❏
7. Add a drop of oil to the wheel axles.
❏
8. Make sure all hinges are securely glued in place.
❏
9. Reinforce holes for wood screws with thin CA where
appropriate (servo mounting screws, cowl mounting
screws, etc.).
❏
10. Confirm that all controls operate in the correct direction
and the throws are set up according to the manual.
❏
11. Make sure there are silicone retainers on all the
clevises and that all servo arms are secured to the
servos with the screws included with your radio.
❏
12. Secure connections between servo wires and
Y-connectors or servo extensions, and the connection
between your battery pack and the on/off switch with
vinyl tape, heat-shrink tubing or special clips suitable
for that purpose.
❏
13. Make sure any servo extension cords you may have
used do not interfere with other systems (servo arms,
pushrods, etc.).
❏
14. Secure the pressure tap (if used) to the muffler with
high temp RTV silicone, thread-locking compound or
J.B. Weld.
❏
15. Make sure the fuel lines are connected and not kinked.
❏
16. Balance your propeller (and spare propellers).
❏
17. Tighten the propeller nut and spinner.
❏
18. Place your name, address, AMA number and telephone
number on or inside your model.
❏
19. Cycle your receiver battery pack (if necessary) and
make sure it is fully charged.
❏
20. If you wish to photograph your model, do so before
your first flight.
❏
21. Range check your radio when you get to the flying field.
❏
22. Make sure all wing attachment bolts and screws are
securely tightened.
A fully cowled engine may run at a higher temperature than
an un-cowled engine. For this reason, the fuel mixture
should be richened so the engine runs at about 200 RPM
below peak speed. By running the engine slightly rich, you
will help prevent dead-stick landings caused by overheating.
Before you get ready to take off, see how the model handles
on the ground by doing a few practice runs at low speeds
on the runway. Hold “up” elevator to keep the tailwheel on
the ground. If necessary, adjust the tailwheel so the model
will roll straight down the runway. If you need to calm your
nerves before the maiden flight, shut the engine down and
bring the model back into the pits. Top off the fuel, then
check all fasteners and control linkages for peace of mind.
Remember to take off into the wind. When you’re ready,
point the model straight down the runway, hold a bit of up
elevator to keep the tail on the ground to maintain tailwheel
steering, and then gradually advance the throttle. As the
model gains speed, decrease up elevator, allowing the tail to
Takeoff
CAUTION (THIS APPLIES TO ALL R/C AIRPLANES): If,
while flying, you notice an alarming or unusual sound such
as a low-pitched “buzz,” this may indicate control surface
flutter. Flutter occurs when a control surface (such as an
aileron or elevator) or a flying surface (such as a wing or
stab) rapidly vibrates up and down (thus causing the noise).
In extreme cases, if not detected immediately, flutter can
actually cause the control surface to detach or the flying
surface to fail, thus causing loss of control followed by an
impending crash. The best thing to do when flutter is
detected is to slow the model immediately by reducing
power, then land as soon as safely possible. Identify which
surface fluttered (so the problem may be resolved) by
checking all the servo grommets for deterioration or signs of
vibration. Make certain all pushrod linkages are secure and
free of play. If it fluttered once, under similar circumstances
it will probably flutter again unless the problem is fixed.
Some things which can cause flutter are; Excessive hinge
gap; Not mounting control horns solidly; Poor fit of clevis pin
in horn; Side-play of wire pushrods caused by large bends;
Excessive free play in servo gears; Insecure servo
mounting; and one of the most prevalent causes of flutter;
Flying an over-powered model at excessive speeds.
Fuel Mixture Adjustments
FLYING
CHECK LIST
34