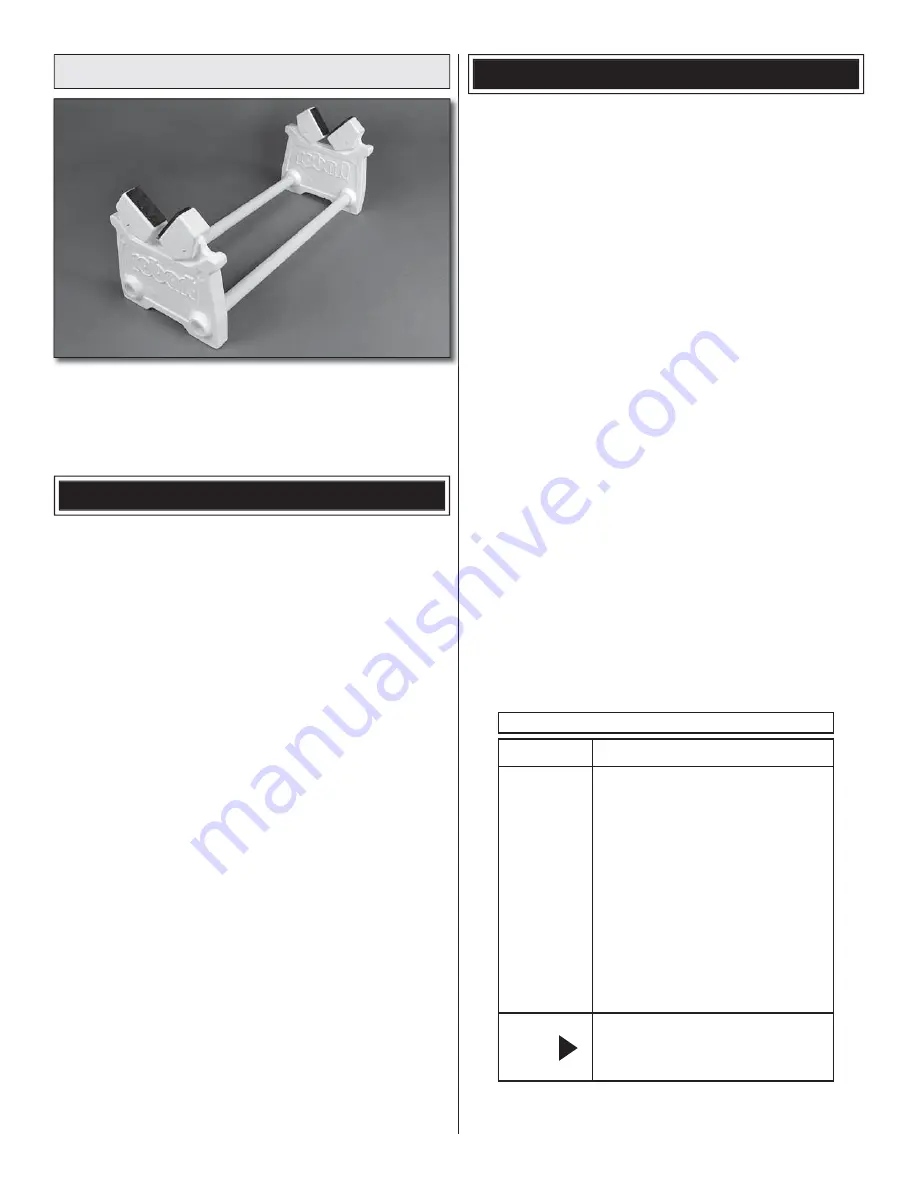
5
Building Stand
A building stand or cradle comes in handy during the build.
We use the Robart Super Stand II (ROBP1402) for all our
projects in R&D, and it can be seen in pictures throughout
this manual.
IMPORTANT BUILDING NOTES
• When you see the term
test fit
in the instructions, it means
that you should first position the part on the assembly
without using any glue
, and then slightly modify or
custom
fit
the part as necessary for the best fit.
•
Whenever the term
glue
is written you should rely upon
your experience to decide what type of glue to use. When
a specific type of adhesive works best for that step, the
instructions will make a recommendation.
•
Whenever just
epoxy
is specified you may use
either
30-minute (or 45-minute) epoxy
or
6-minute epoxy. When
30-minute epoxy is specified it is
highly
recommended that
you use only 30-minute (or 45-minute) epoxy, because you
will need the working time and/or the additional strength.
•
Photos
and
sketches
are placed
before
the step they refer
to. Frequently you can study photos in following steps to get
another view of the same parts.
•
The stabilizer and wing incidences and engine thrust
angles have been factory-built into this model. However,
some technically-minded modelers may wish to check these
measurements anyway. To view this information visit the web
site at
greatplanes.com
and click on “Technical Data.” Due
to manufacturing tolerances which will have little or no effect
on the way your model will fly, please expect slight deviations
between your model and the published values.
ORDERING REPLACEMENT PARTS
Replacement parts for the Christen Eagle are available using
the order numbers in the Replacement Parts List that follows.
The fastest, most economical service can be provided by
your hobby dealer or mail-order company.
To locate a hobby dealer, visit the Great Planes web site
at
greatplanes.com
. Choose “Where to Buy” at the
bottom of the menu on the left side of the page. Follow the
instructions provided on the page to locate a U.S., Canadian
or International dealer.
Parts may also be ordered directly from Hobby Services
by calling (217) 398-0007, or fax at (217) 398-7721, but full
retail prices and shipping and handling charges will apply.
Illinois and Nevada residents will also be charged sales tax.
If ordering via fax, include a Visa
®
or MasterCard
®
number
and expiration date for payment.
Mail parts orders and payments by personal check to:
Hobby Services
3002 N. Apollo Drive, Suite 1
Champaign, IL 61822
Be certain to specify the order number exactly as listed in
the
Replacement Parts List
. Payment by credit card or
personal check only; no C.O.D.
If additional assistance is required for any reason, contact
Product Support by telephone at (217) 398-8970, or by
e-mail at
.
Order No.
Description
NOTE
REPLACEMENT PARTS LIST
Full-size plans are not available.
You can download a copy of this
manual at www.greatplanes.com.
GPMA4160
GPMA4161
GPMA4162
GPMA4163
GPMA4164
GPMA4165
GPMA4166
GPMA4167
GPMA4168
GPMA4169
GPMA4170
GPMA4171
GPMA4172
Fuselage
Top Wing
Bottom Wing
Tail Set
Hatch
Cowl
Cabanes
Struts
Wheel Pants
Landing Gear
Decals
Spinner
Landing Gear Fairings
Summary of Contents for Christen Eagle .46
Page 36: ......