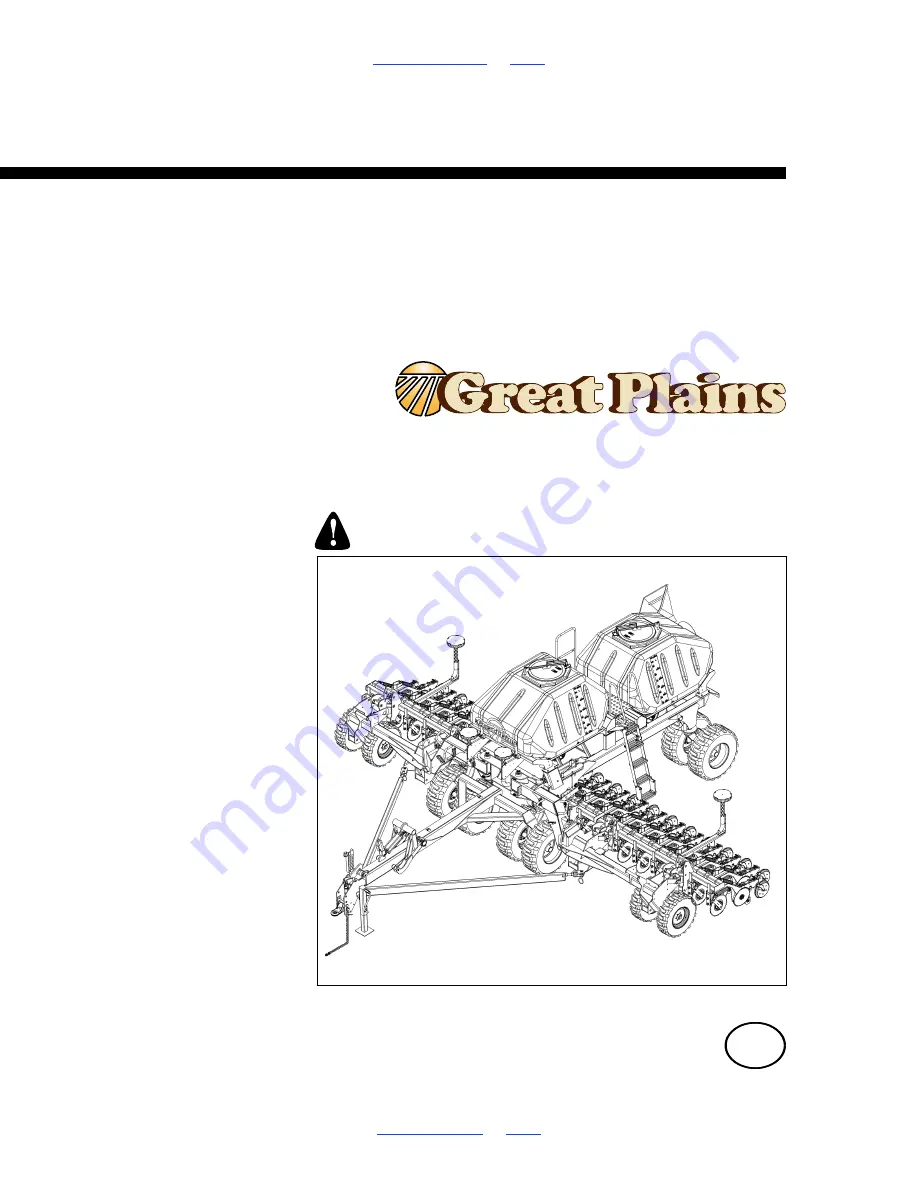
Manufacturing, Inc.
www.greatplainsmfg.com
© Copyright 2019
Printed 02/26/2019
166-207M
EN
ORIGINAL INSTRUCTIONS
Operator Manual
NTA907HD and NTA3007HD
9m/30ft No-Till Heavy Duty Air Drill
Read the operator manual entirely. When you see this symbol, the subsequent
instructions and warnings are serious - follow without exception. Your life and
the lives of others depend on it!
Illustrations may show optional equipment not supplied with standard unit.
29423
Summary of Contents for NTA3007HD
Page 2: ...Great Plains 166 207M 02 26 2019 Table of Contents Index ii 166 207M Table of Contents Index ...
Page 4: ...2SF24 and 2SF30 ...
Page 177: ...Table of Contents Index Table of Contents Index ...
Page 178: ...Great Plains Mfg 1525 E North St P O Box 5060 Salina KS 67402 Table of Contents Index ...