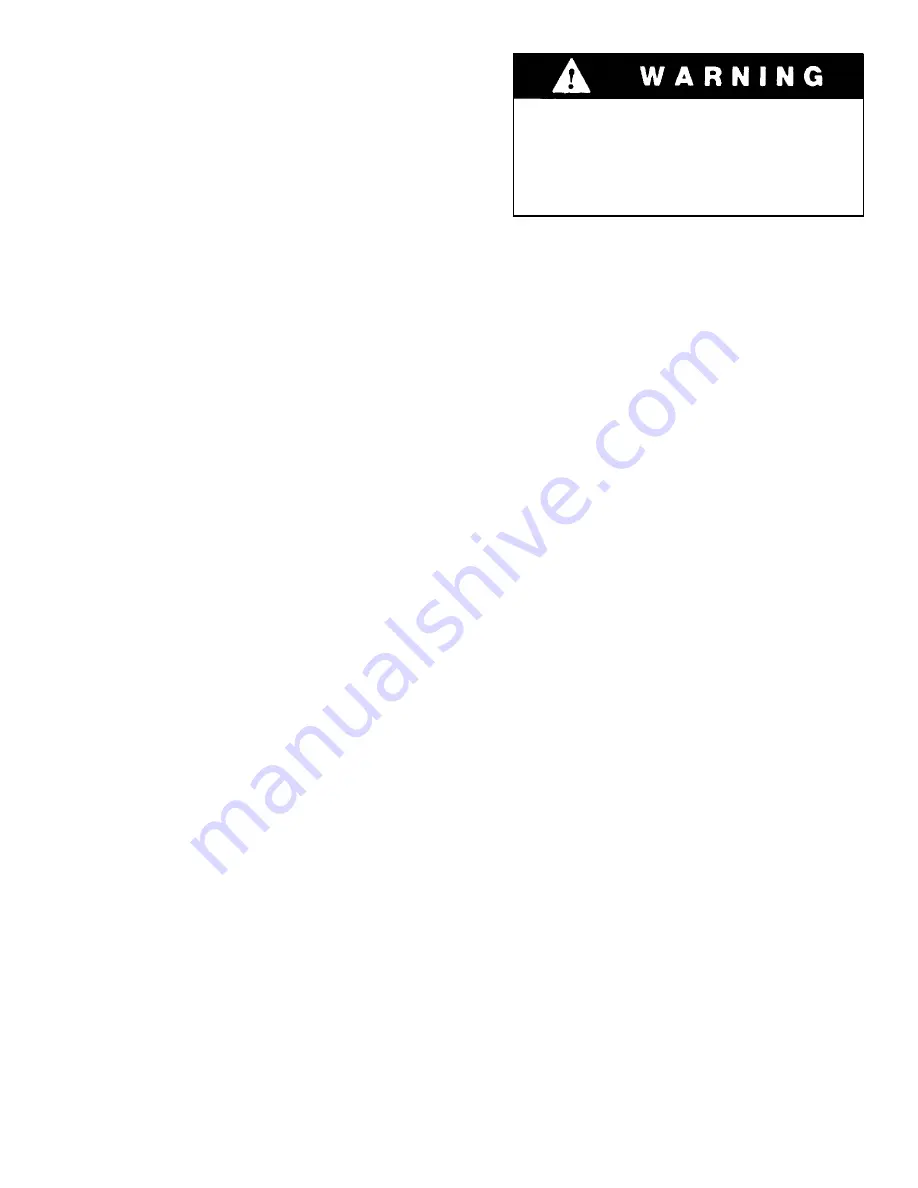
SHIFTING GEARS
Smooth, efficient gear shifting depends on coordin-
ated use of accelerator pedal, clutch pedal, range
preselection lever, deep reduction button and shift
lever. It is also important that shifting occur at the
proper time with respect to carrier power require-
ments.
For those unfamiliar with a manual transmission it
may seem that gear shifting is a complicated
procedure. A practice period with the carrier parked
and the engine turned off will help develop the
necessary coordination and confidence. There
should be little difficulty if shifting procedures are
followed step by step.
When practicing with the engine turned off there
will be areas in the shift pattern where you will be
unable to make a complete engagement. Don’t use
excessive force, just learn the pattern.
When to shift gears
Smooth, timely shifting not only increases carrier
service life, it provides greater driving safety.
In lower gears use only enough engine speed to get
the carrier rolling easily. High engine speeds under
light load conditions waste fuel and cause excessive
and unnecessary noise. Use a little more engine
speed for each successive upshift until reaching
desired cruising speed.
Unless starting from a standstill on an uphill grade, or
in off-road use, it is unnecessary to use LO-LO range.
When load conditions cause a continuing loss of
engine speed, downshift to the next lower gear.
In general, operate in a gear that will permit
acceleration.
Though it is permissible to use the braking power of
the engine when traveling downhill, take care to
avoid overspeeding the engine (exceeding governed
RPM). The governor has no control over engine
speed when the engine is being pushed by the carrier
Ioad. Select an appropriate gear ratio and use your
brakes to assist in slowing the carrier.
Use Lo Lo, or Lo gear ranges for off-road conditions
and for remote control operation. First gear may be
used only if surface is hard and level.
Double-Clutching
Gears in the main transmission are not synchronized
and double clutching procedure must be used when
shifting.
Double-clutching is a procedure for adjusting the
speed of one transmission gear shaft (driven by the
engine) to a second transmission gear shaft (con-
nected to carrier drive wheels) to prevent clashing
when gears on these shafts mesh.
This is accomplished by using the engine to increase
or decrease the speed of the engine-driven gear shaft.
Two double-clutching procedures are given, one for
upshifting and one for downshifting. Be sure to use
each at the proper time. Using the wrong procedure
will cause gears to clash.
NOTES
: The following double-clutching procedures
apply to shifts
within a gear range
(Lo thru 4th
gears and 5th thru 8th gears).
Additional steps
are
required when shifting from one range to another.
These steps will be described under Upshifting and
Downshifting headings (starting on page 24).
Although double-clutching procedures are broken
down into separate steps, the actual performance of
these steps should be rapid and smooth.
Double-Clutching for Upshift
Release accelerator pedal and depress clutch
pedal.
Move gear shift lever to neutral and release clutch
pedal.
When engine speed nears low idle, depress clutch
and shift to next higher gear. If shift timing has
been correct, gears will mesh smoothly with no
clash.
Release clutch evenly while depressing accelerator
to apply power smoothly.
Stop carrier and select appropriate gear
range before traveling a steep grade
under off-highway conditions. Attempting
up or downshifts under these conditions
can be dangerous.
W A R N I N G
1.
2.
3.
4.
2 3