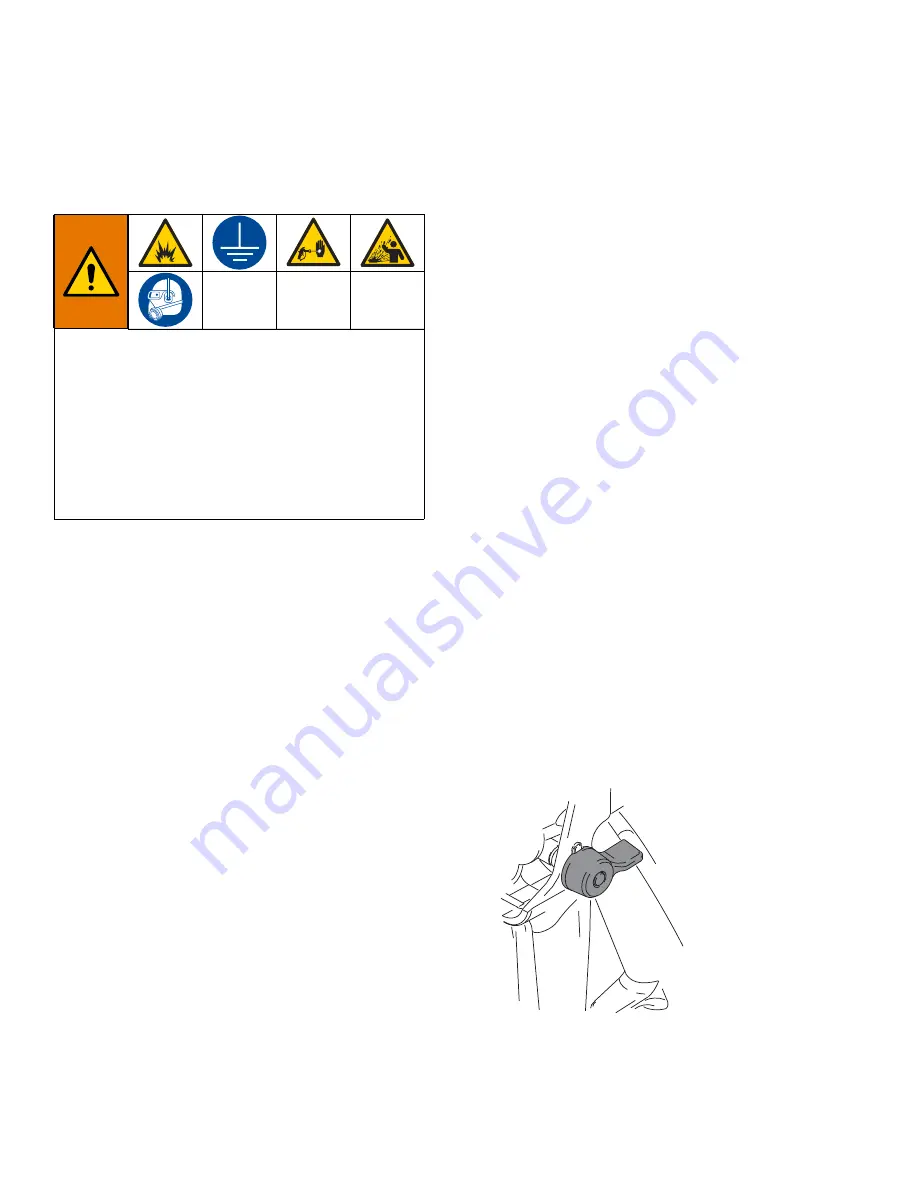
Empty and Flush Entire System (new system or end of job)
36
3A4381M
Empty and Flush Entire System
(new system or end of job)
NOTE:
•
If the system includes heaters and heated hose,
turn them off and allow to cool before flushing. Do
not turn on the heaters until the fluid lines are clear
of solvent.
•
Cover fluid containers and use the lowest possible
pressure when flushing to avoid splashing.
•
Before color change or shutdown for storage,
circulate the solvent at a higher flow rate and for a
longer time. Change the solvent when it gets dirty.
•
To only flush the fluid manifold, see
•
If the machine is inoperable, use drain plugs on the
pump inlet fittings.
Guidelines
Flush new systems if the coating materials will be
contaminated by mineral oil. Follow the
on page 38 to ensure mineral oil is removed.
Flushing will help prevent materials from settling or
gelling in the pumps, lines, and valves. Flush the system
when any of the following situations occur.
•
Anytime the system will not be used for more
than one week (depending on materials used)
•
If the materials used have fillers that will settle
•
If using materials that are moisture sensitive
•
Before servicing
•
If the machine is going into storage, replace the
flush solvent with light oil. Never leave the
equipment empty of any fluid.
Empty System Procedure
1. Follow
2. If your system is equipped with a solvent flush
3. If your system is not equipped with a solvent flush
pump, follow the
Pressure Relief Procedure
on
page 26 before servicing the system.
4. Engage the trigger lock.
To avoid fire and explosion, always ground equipment
and waste container. To avoid static sparking and
injury from splashing, always flush at the lowest
possible pressure. Hot solvent may ignite. To avoid fire
and explosion:
•
Flush equipment only in a well-ventilated area
•
Ensure main power is off and heater is cool before
flushing
•
Do not turn on heater until fluid lines are clear of
solvent
ti1949a