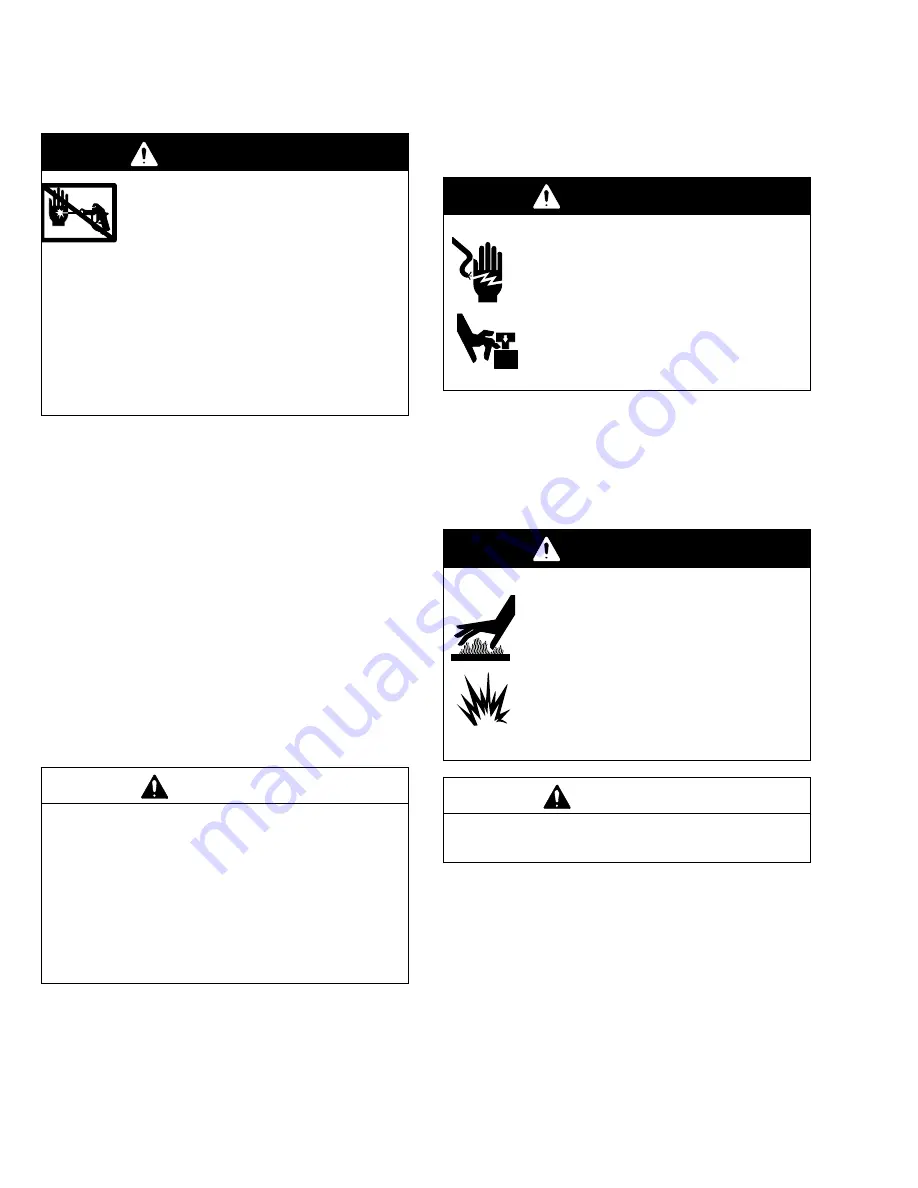
4
309711
General Repair Information
Pressure Relief Procedure
WARNING
INJECTION HAZARD
System pressure must be manually
relieved to prevent system from starting
or spraying accidentally. Fluid under high
pressure can be injected through skin and cause
serious injury. To reduce risk of injury from injec-
tion, splashing fluid, or moving parts, follow
Pres-
sure Relief Procedure
whenever you:
are instructed to relieve pressure,
stop spraying,
check or service any system equipment,
or install or clean spray tip.
1. Lock gun safety latch.
2. Turn ON/OFF switch to OFF.
3. Unplug power supply cord.
4.
Unlock gun safety latch. Hold metal part of gun
firmly to grounded metal pail. Trigger gun to relieve
pressure.
5. Lock gun safety latch.
6. Open pressure drain valve. Leave pressure drain
valve open until ready to spray again.
If suspected that spray tip or hose is completely
clogged, or that pressure has not been fully relieved
after following steps above
, VERY SLOWLY loosen tip
guard retaining nut or hose end coupling to relieve
pressure gradually, then loosen completely. Now clear
tip or hose obstruction.
CAUTION
To reduce risk of pressure control malfunction:
Use needle nose pliers to disconnect wire. Never
pull on wire, pull on connector.
Mate wire connectors properly. Center flat blade of
insulated male connector in female connector.
Route wires carefully to avoid interference with
other connections of pressure control. Do not pinch
wires between cover and control box.
1.
Keep all screws, nuts, washers, gaskets, and
electrical fittings
removed during repair proce-
dures. These parts are not normally provided with
replacement assemblies.
WARNING
ELECTRIC SHOCK HAZARD
MOVING PARTS HAZARD
To reduce risk of serious injury, including
electric shock, do not touch moving or
electrical parts with fingers or tools while
testing repair. Shut off and unplug spray-
er when inspection is complete. Install all
covers, gaskets, screws and washers
before operating sprayer.
2.
Test repair
after problem is corrected.
3.
If sprayer does not operate properly
, review
repair procedure to verify procedure was done
correctly. If necessary, see Troubleshooting Guide,
pages 5 – 9, for other possible solutions.
WARNING
HOT SURFACES HAZARD
EXPLOSION HAZARD
Motor and drive housing may be very hot
during operation and could burn skin if
touched.
Flammable materials spilled on hot, bare
motor could cause fire or explosion.
Have motor shroud in place during
operation to reduce risk of burns, fire or
explosion.
CAUTION
Do not run sprayer dry for more than 30 seconds to
avoid damaging pump packings.
4.
Install motor shroud before operation
of spray-
er and replace if damaged. Motor shroud prevents
overheating, and protects operator from possible
electrical shock by touching terminals of capacitor.
It can also reduce risk of burns, fire or explosion;
see preceding
WARNING
.