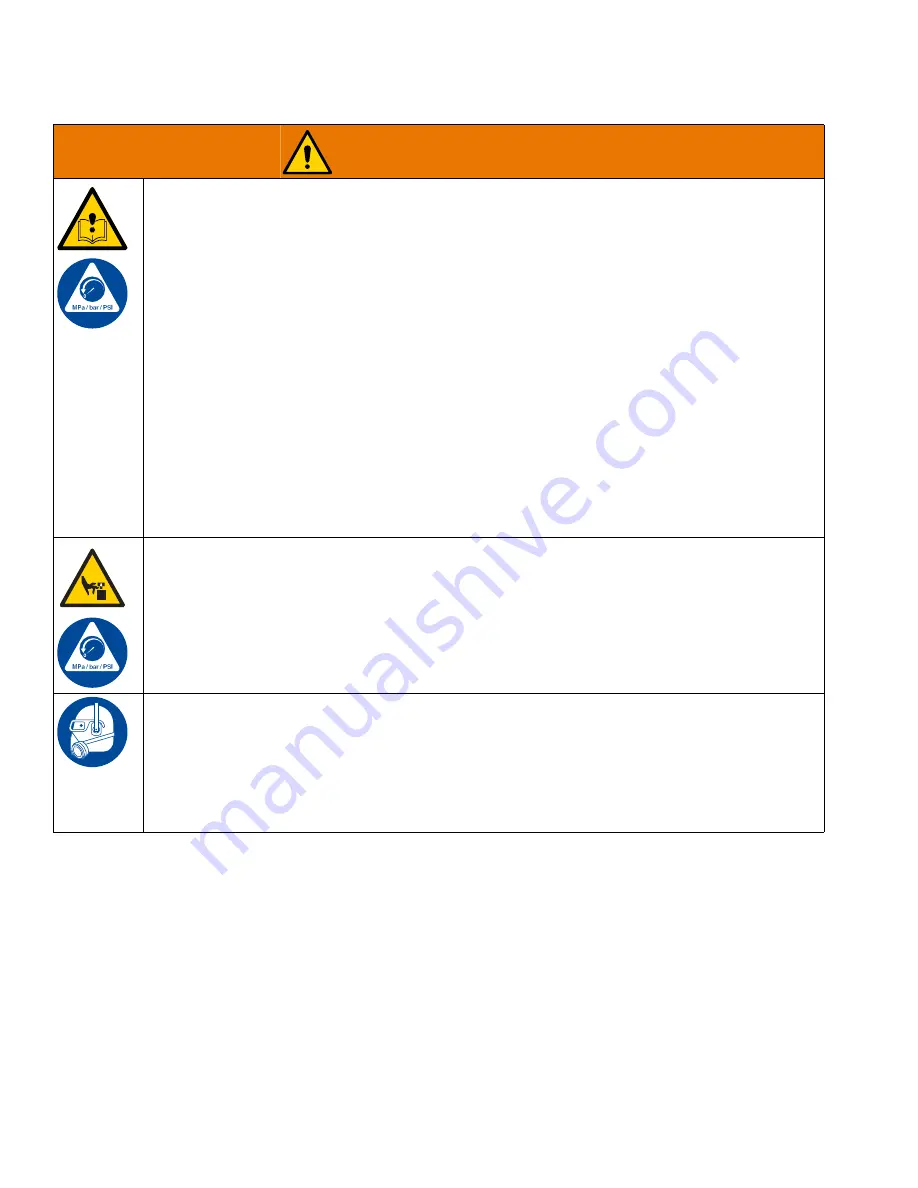
Warnings
6
3A7939A
EQUIPMENT MISUSE HAZARD
Misuse can cause death or serious injury.
•
Do not operate or spray near children. Keep children away from equipment at all times.
•
Do not operate the unit when fatigued or under the influence of drugs or alcohol.
•
Do not exceed the maximum working pressure or temperature rating of the lowest rated system
component. See
in all equipment manuals.
•
Use disinfectants that are compatible with equipment wetted parts. See
in all equipment manuals. Read disinfectant manufacturer’s warnings. For complete information
about your disinfectant, request Safety Data Sheets (SDSs) from distributor or retailer.
•
Do not leave the work area while equipment is energized or under pressure.
•
Turn off all equipment and follow the
when equipment is not in use.
•
Check equipment daily. Repair or replace worn or damaged parts immediately with genuine
manufacturer’s replacement parts only.
•
Do not alter or modify equipment. Alterations or modifications may void agency approvals and
create safety hazards.
•
Make sure all equipment is rated and approved for the environment in which you are using it.
•
Use equipment only for its intended purpose. Call your distributor for information.
•
Route hoses and cables away from traffic areas, sharp edges, moving parts, and hot surfaces.
•
Do not kink or over bend hoses or use hoses to pull equipment.
•
Comply with all applicable safety regulations.
MOVING PARTS HAZARD
Moving parts can pinch, cut or amputate fingers and other body parts.
•
Keep clear of moving parts.
•
Do not operate equipment with protective guards or covers removed.
•
Equipment can start without warning. Before checking, moving, or servicing equipment, follow the
and disconnect all power sources.
PERSONAL PROTECTIVE EQUIPMENT
Wear appropriate protective equipment when in the work area to help prevent serious injury,
including eye injury, burns, hearing loss, and inhalation of disinfectant chemical mists and vapors.
Protective equipment includes but is not limited to:
• Protective eye-wear, and hearing protection.
• Appropriate respirators, protective clothing, and gloves.
• All protective equipment specified by the disinfectant manufacturer.
WARNING