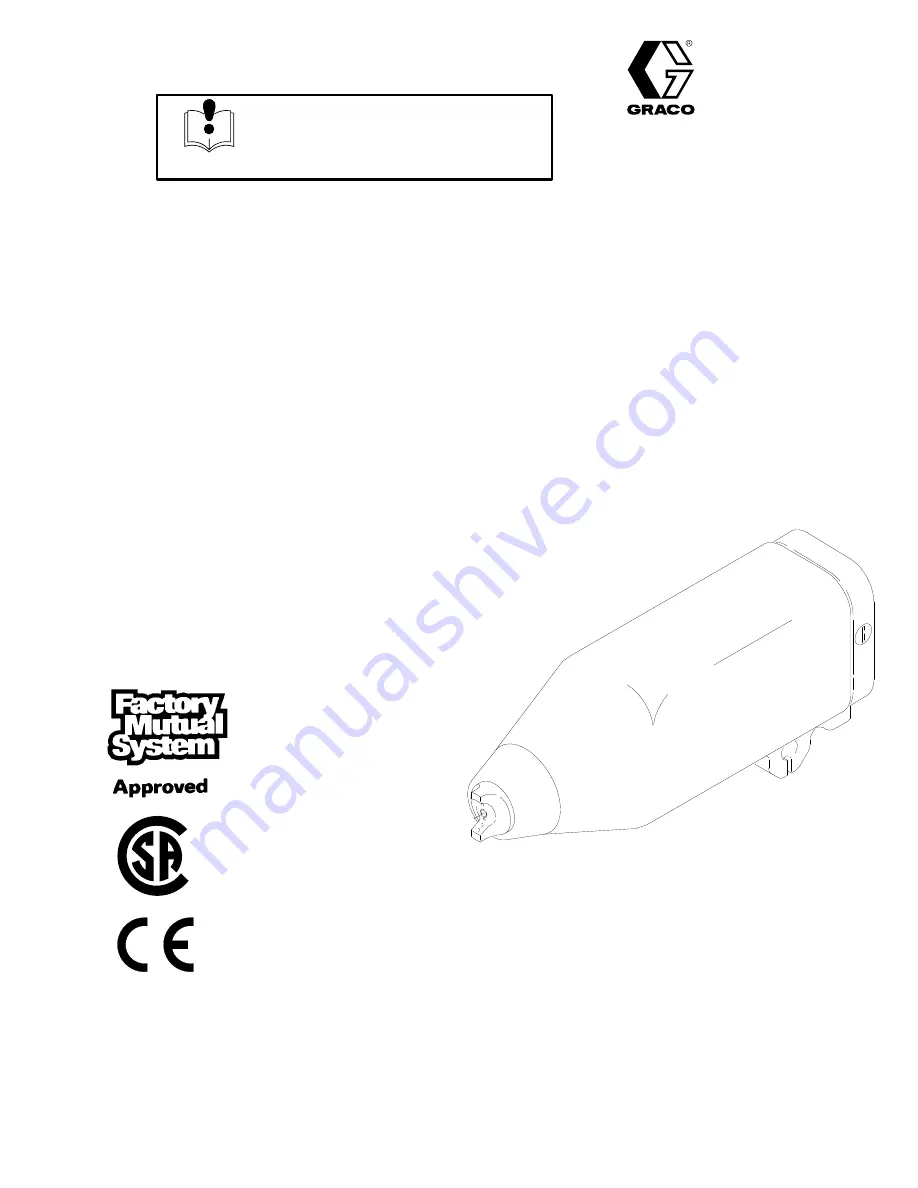
INSTRUCTIONS–PARTS LIST
308–385
Rev. C
Supersedes A
and PCN B
AUTOMATIC ELECTROSTATIC
Model PRO 5500sc
Air Spray Gun
100 psi (7 bar) Maximum Working Pressure
For use with Class
, Group D paint spray materials
U.S. PATENT NO. 4,290,091; 4,219,865; 4,497,447; 4,462,061; 4,660,774;
5,063,350; 5,073,709; 5,080,289; 5,093,625; 5,289,977
Patented 1986, 1987 Canada
Brevete 1986, 1987
U.K. PATENT NO. 2,147,158; 2,142,559B; 2,140,327–B
Other Foreign Patents Pending
Part No. 236–683, Series A
Complete Standard PRO 5500sc Spray Gun: includes
spray gun, shroud, manifold, and mounting bracket
Part No. 236–684, Series A
Complete PRO 5500sc Recirculating Spray Gun: same
as part no. 236–683 spray gun only with part no.
236–851 recirculation kit installed
GRACO INC. P.O. BOX 1441 MINNEAPOLIS, MN 55440–1441
COPYRIGHT 1994 GRACO INC.
This manual contains important
warnings and information.
READ AND RETAIN FOR REFERENCE
INSTRUCTIONS