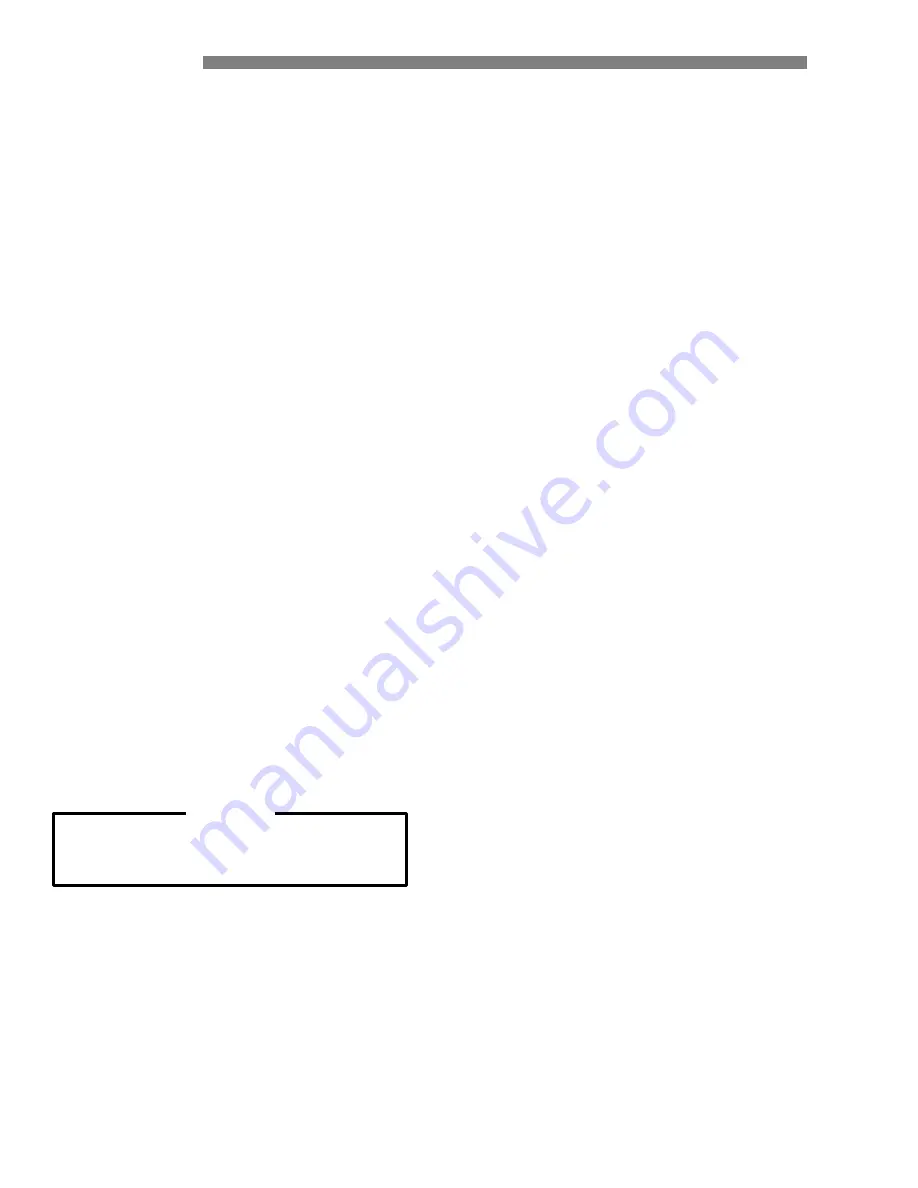
16
308–532
PUMP SERVICE
Servicing the Valves
1. Remove the hex valve plug.
2. Examine the o–ring under the plug for cuts or
distortion and replace if worn. Lubricate new o–ring
before installing.
3. Grasp valve retainer by tab at the top with pliers
and remove from valve chamber
. V alve parts
usually separate during removal.
Note:
A special tool will be needed to remove the
seat from the manifold. A reverse pliers or a
standard vise grip and a 1/4” x 3” bolt to fit I.D.
of seat inserted under the edge of the seat,
will pry the valve seat out easily.
4. Examine all valve parts for wear and replace with
preassembled valve assembly in service kit
containing retainer , spring, valve, valve seat,
o–ring, and back–up ring.
5. Grasp new valve assembly by tab at top with pliers,
immerse in oil and push into valve chamber . Be
certain valve assembly is square in valve chamber.
6. Apply Loctite 242 to valve plug, thread into manifold
port and torque per chart.
Note
:
Corrosion Resistant models require the coil
spring installed in the Valve Plug.
Servicing the Pumping Section
Disassembly:
1. Remove the four (4) hex nuts or two (2) bolts from
the manifold (varies with model).
2. Rotate crankshaft by hand to start separation of
manifold from crankcase. Support the underside of
the manifold and tap lightly with a mallet to remove
the manifold assembly.
CAUTION
Keep manifold properly aligned with ceramic
plungers when removing to avoid damage to
either plungers or seals.
3. Remove oil pan and slide out seal retainer with
wicks.
4. Using a wrench, loosen the plunger retainer. Grasp
ceramic plunger and push toward crankcase until
plunger retainer pops out.
5. Remove plunger retainer with copper gasket,
back–up Ring and o–ring.
6. Remove plunger from plunger rod.
Reassembly:
1. Carefully examine each ceramic plunger for
scoring or cracks, replace if worn and slip onto
plunger rod.
Note:
Ceramic plunger can only be installed one
direction (front to back). Do not force onto
rod.
2. Examine plunger retainer and stud and replace if
worn.
Note:
Thread stud into plunger retainer.
3. Examine o–ring, back–up ring and gasket on
plunger retainer and replace if worn or cut.
Lubricate o–ring for ease of installation and to avoid
damaging o–rings.
Note:
First install gasket, then back–up ring and
o–ring.
4. Thread plunger retainer and stud assembly into
plunger rod. Exercise caution not to over torque.
5. Saturate new oil wick by soaking in oil, place in seal
retainer and slip retainer over ceramic plunger.
6. Replace oil pan.
7. Turn shaft by hand to line up plungers so end
plungers are parallel.
8. Carefully slip manifold onto plungers, keeping
manifold level, and tap with mallet to bring manifold
flush with crankcase.
9. Replace washers and nuts or bolts and torque per
chart.
Servicing the Seals and V–Packings
Disassembly:
1. Remove the manifold as described.
2. With crankcase side of manifold facing up, unscrew
the seal case from the manifold using a special key
wrench.
3. Remove o–ring from seal case.
4. Remove snap ring and low pressure seal from the
seal case. Seals are generally removed easily
without any tools.
5.
High Pressure Seal Models:
The high pressure
seal is generally easily removed from the manifold
without any tools. If extremely worn a reverse pliers
may be used.
6.
V–Packing Models:
The female adapter , two
v–packings and male adapter are easily removed
from manifold without tools. If extremely worn a
reverse pliers may be used.