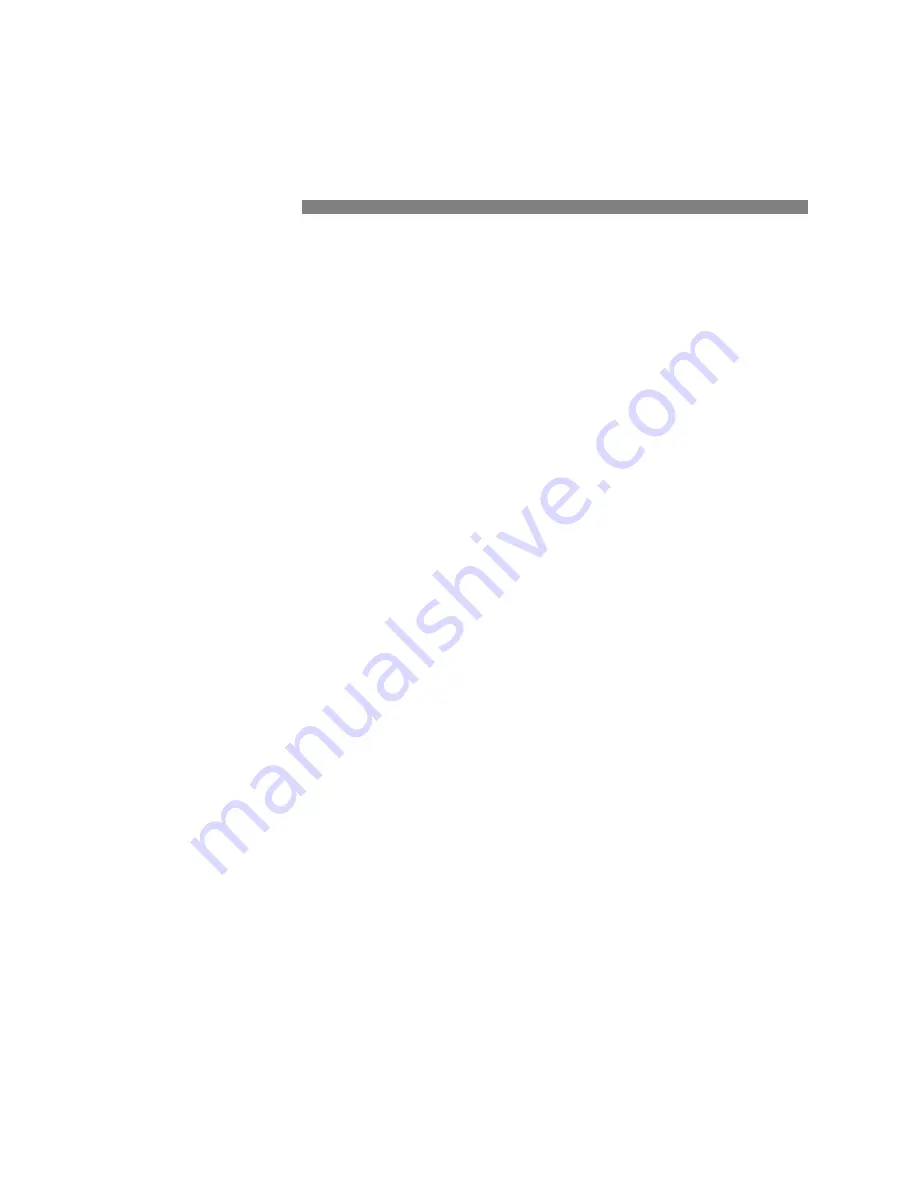
WARNING
HIGH PRESSURE SPRAY CAN CAUSE SERIOUS INJURY.
FOR PROFESSIONAL USE ONLY. OBSERVE ALL WARNINGS.
Read and understand all instruction manuals before operating equipment.
FLUID INJECTION HAZARD
General Safety
This pressure washer generates very high fluid
pressure. Spray from the gun, leaks or ruptured
components can inject fluid through your skin and into
your body and cause extremely serious bodily injury
including the need for amputation. Also, fluid injected or
splashed into the eyes or on the skin can cause serious
damage.
NEVER point the spray gun or wand at anyone or at any
part of the body.
NEVER put hand or fingers over the
spray tip.
ALWAYS follow the
Pressure Relief Procedure
,
before cleaning or servicing any part of the sprayer.
NEVER try to stop or deflect leaks with your hand or
body.
Be sure equipment safety devices are operating
properly before each use.
Medical Treatment
If any fluid appears to penetrate your skin, get
EMERGENCY MEDICAL TREATMENT AT ONCE. DO
NOT TREAT AS A SIMPLE CUT.
Tell the doctor exactly
what fluid was injected.
NOTE TO PHYSICIAN:
Injection in the skin is a
traumatic injury.
It is important to treat the injury
surgically as soon as possible.
Do not delay
treatment to research toxicity. Toxicity is a concern
with some exotic coatings injected directly into the
bloodstream. Consultation with a plastic surgeon
or reconstructive hand surgeon may be advisable.
Pressure Relief Procedure
To reduce the risk of serious bodily injury, including fluid
injection and splashing in the eyes or on the skin, always
follow this procedure whenever you stop spraying for
more than 10 minutes, when shutting down, and before
checking or repairing any part of the system.
1. Engage the trigger safety latch.
2. Turn the sprayer off.
3. Remove the ignition cable from the spark plug.
4. Shut off the water supply.
5. Disengage the trigger safety latch and trigger the
gun to relieve pressure, and then engage the trigger
safety latch again.
6. Before long–term (overnight) storage or
transporting of unit, disconnect the water supply
and turn off the fuel supply valve.
Spray Gun Safety Devices
Be sure all gun safety devices are operating properly
before each use. Do not remove or modify any part of
the gun; this can cause a malfunction and result in
serious bodily injury.
SAFETY LATCH: Whenever you stop spraying for a
moment, always set the gun safety latch in the engaged
or “safe” position, making the gun inoperative. Failure to
properly set the safety latch can result in
accidental
triggering of the gun.
SPRAY TIP SAFETY : Use extreme caution
when
cleaning or changing spray tips. If a spray tip clogs while
spraying, engage the gun safety latch immediately
.
ALWAYS follow the
Pressure Relief Procedure
and
then remove the spray tip to clean it.