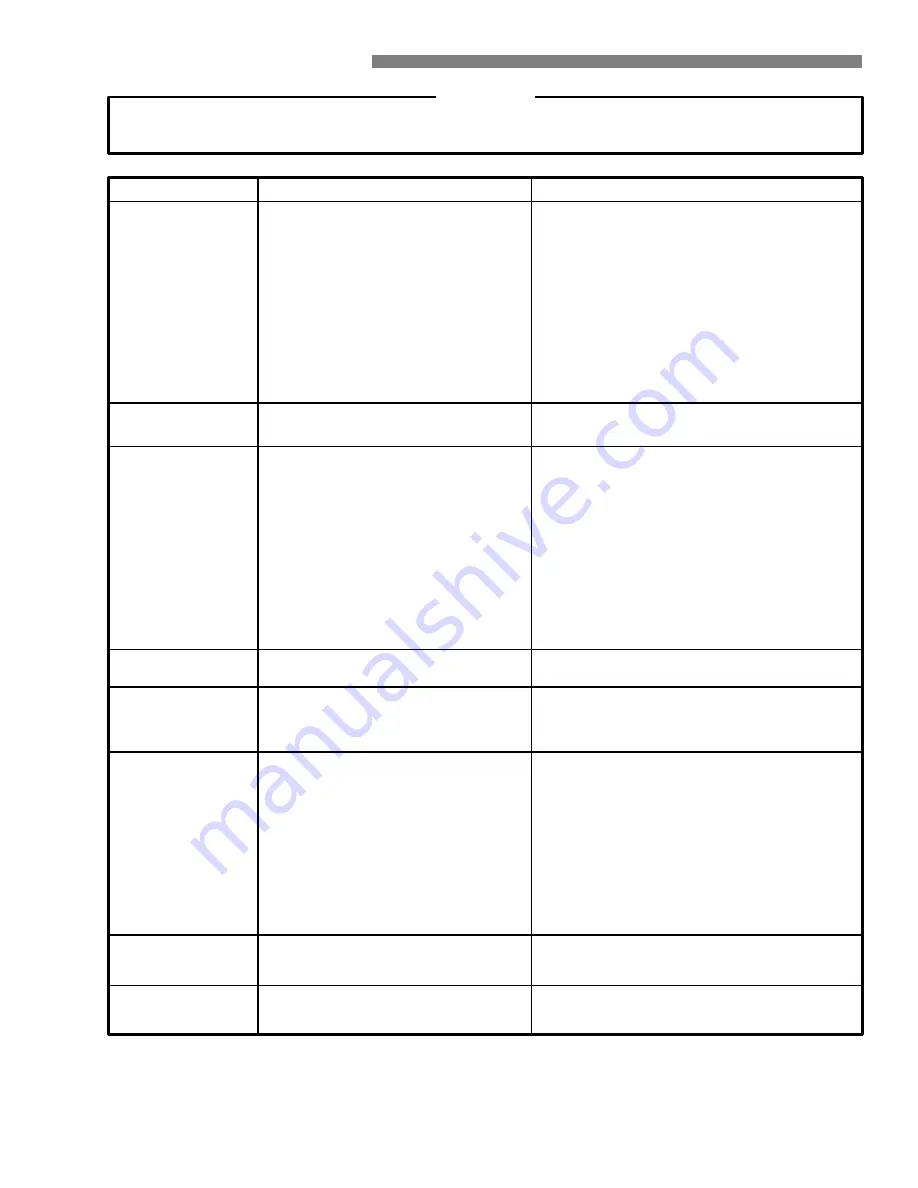
11 308-537
TROUBLESHOOTING CHART
WARNING
To reduce the risk of serious bodily injury, including fluid injection, splashing in the eyes or on the skin or injury
from moving parts, always follow the
Pressure Relief Procedure Warning
before proceeding.
PROBLEM
CAUSE
SOLUTION
Low pressure and/or
pump runs rough
Partially plugged air cleaner filter.
Spark plug dirty, wrong gap or wrong type.
Remove and clean.
Clean, adjust the gap or replace.
Replace with tip of proper size.
Clean. Check more frequently.
Check filter. Replace packings. See PUMP SERVICE.
Check water flow rate to pump.
Clean inlet and discharge valve assemblies. Check
filter.
Check garden hose, may be collapsed or kinked.
Replace worn valves.
Replace high pressure hose.
Worn or wrong size tip.
Inlet filter clogged.
Worn packings, abrasives in water or
natural wear.
Inadequate water supply.
Fouled or dirty inlet or discharge valves.
Even a small particle can cause the valve
to stick.
Restricted inlet.
Worn inlet or discharge valves.
Leaking high pressure hose.
Engine misses or
lacks power
Engine will not start or
is hard to start
Fill the tank with gasoline, open fuel shut off valve.
Check fuel line and carburetor.
Add to proper level.
Move switch to start position.
Drain fuel tank and carburetor. Use new fuel and dry
spark plug.
Open choke and crank engine several times to clear
out gas.
Remove and clean.
Clean, adjust the gap or replace.
Trigger spray gun.
No gasoline in fuel tank or carburetor.
Low oil
Start/Stop switch in Stop position.
Water in gasoline or old fuel.
Choked improperly. Flooded engine.
Dirty air cleaner filter.
Spark plug dirty, wrong gap or wrong type.
Spray gun closed.
Water leakage from
under pump manifold
Install new packings. See PUMP SERVICE.
Worn packings.
Water in pump
Humid air condensing inside crankcase.
Worn packings.
Oil seals leaking.
Change oil as specified in MAINTENANCE.
Install new packings. See PUMP SERVICE.
Install new oil seals. See PUMP SERVICE.
Frequent or premature
failure of the packings
Scored, damaged or worn plungers.
Abrasive material in the fluid being pumped.
Inlet water temperature too high.
Overpressurizing pump.
Excessive pressure due to partially plugged
or damaged tip.
Pump running too long without spraying.
Running pump dry.
Install new plungers. See PUMP SERVICE.
Install proper filtration on pump inlet plumbing.
Check water temperature; may not exceed 160
F.
Do not modify any factory–set adjustments. See
EQUIPMENT MISUSE HAZARD.
Clean or replace tip. See Installing and Changing
Spray Tips.
Never run pump more than 10 minutes without
spraying.
Do not run pump without water.
Strong surging at the
inlet and low pressure
on the discharge side
Foreign particles in the inlet or discharge
valve or worn inlet and/or discharge valves.
Clean or replace valves. See PUMP SERVICE.
Oil leakage between
the engine and the
pump
Worn oil seals and/or o-ring.
Replace oil seals and/or o-ring. See SERVICE
SECTION.