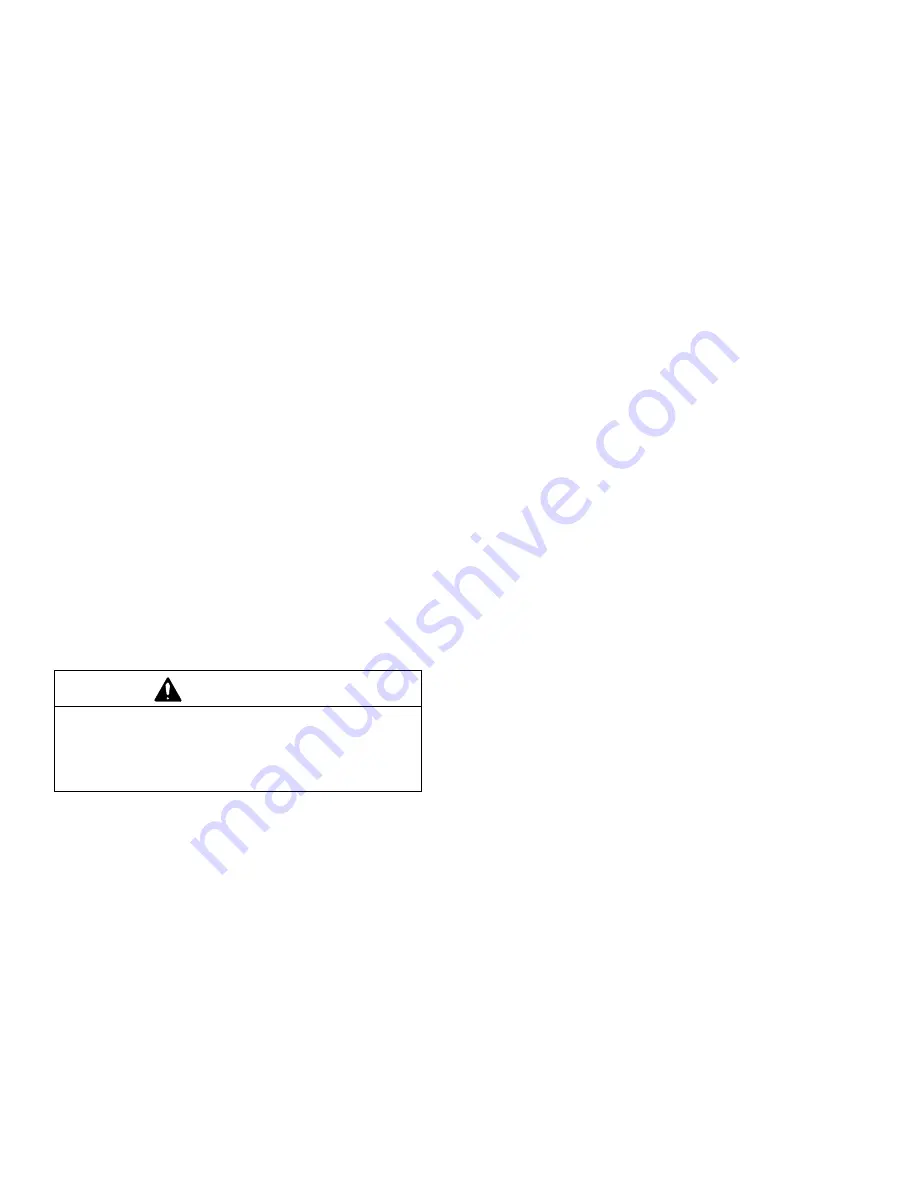
18
308354
Service
DISPLACEMENT PUMP SERVICE
Disassembly
When disassembling the pump, lay out all the removed
parts in sequence, to ease reassembly.
NOTE: Packing Repair Kits are available. For the best
results, use all the new parts in the kit. Kit parts are
marked with an asterisk, for example (3*). You can
also convert the pump to different packing materials.
Refer to page 27.
1.
Place the pump lengthwise in a large vise, with the
jaws on either the outlet housing (7) as shown in
Fig. 7 or on the cylinder (9) flats. Using the sup-
plied wrench (110), loosen, but do not remove, the
packing nut (2).
2.
Apply a pipe wrench to the flats of the intake valve
(19). Unscrew the intake valve (19) from the intake
housing (18). Be careful to catch the intake ball
(17) as you remove the intake valve, so that it
does not fall and suffer damage. Remove the seal
(8) from the intake valve. Inspect the ball and the
seat (D) of the intake valve for wear or damage.
3.
Apply a pipe wrench to the hex of the valve hous-
ing (18). The pump assembly may separate at joint
A or joint B.
CAUTION
To reduce the possibility of costly damage to the rod
(1) and cylinder (9), always use a rubber mallet to
drive the rod out of the cylinder. Never use a ham-
mer.
If the assembly separates at joint A:
a.
Unscrew the valve housing (18) from the
cylinder, using a 2–5/8 in. wrench for the
cylinder flats. Using a rubber mallet, drive the
displacement rod (1) and piston assembly out
of the outlet housing (7) and cylinder (9) until
the piston comes free. Pull the rod and piston
from the cylinder, being careful not to scratch
the parts.
b.
Using a 2–5/8 in. wrench for the cylinder flats,
unscrew the cylinder (9) from the outlet hous-
ing (7). Remove the two seals (8) from the
cylinder. Shine a light into the cylinder (9) to
inspect the inner surface for scoring or wear.
Now go to step 4.
If the assembly separates at joint B:
c.
Unscrew the cylinder (9) and valve housing
(18) from the outlet housing (7). Gently pull the
cylinder and valve housing straight out of the
outlet housing; the displacement rod (1) and
piston assembly will come out with these
parts.
d.
Place the valve housing (18) in the vise and
unscrew the cylinder (9) from the housing,
using a 2–5/8 in. wrench for the cylinder flats.
The displacement rod (1) and piston assembly
will remain in the cylinder.
e.
Using a rubber mallet, drive the displacement
rod (1) and piston assembly out of the cylinder
(9) until the piston comes free. Pull the rod and
piston from the cylinder, being careful not to
scratch the parts.
f.
Remove the two seals (8) from the cylinder.
Shine a light into the cylinder (9) to inspect the
inner surface for scoring or wear. Now go to
step 4.
4.
Place the flats of the piston seat housing (16) in a
vise, as shown in Fig. 8.
5.
Using an adjustable wrench, unscrew the piston
ball housing (10) from the piston seat housing. Be
careful to catch the piston ball (11) as you sepa-
rate the piston seat housing and ball housing, so
that it does not fall and suffer damage.
6.
Examine the displacement rod (1) for scratches or
other damage. Only if the rod needs replace-
ment, unscrew it from the piston ball housing (10),
using an adjustable wrench on the flats of the rod.
7.
Remove the glands and v-packings (P) from the
piston seat housing (16). Inspect the ball (11), and
the seat (E) and guides (F) on the housing for
wear or damage. See Fig. 9.
8.
Unscrew the packing nut (2) from the outlet hous-
ing (7). Remove the glands and v-packings (T).
See Fig. 9.
9.
Clean all parts with a compatible solvent and
inspect them for wear or damage.