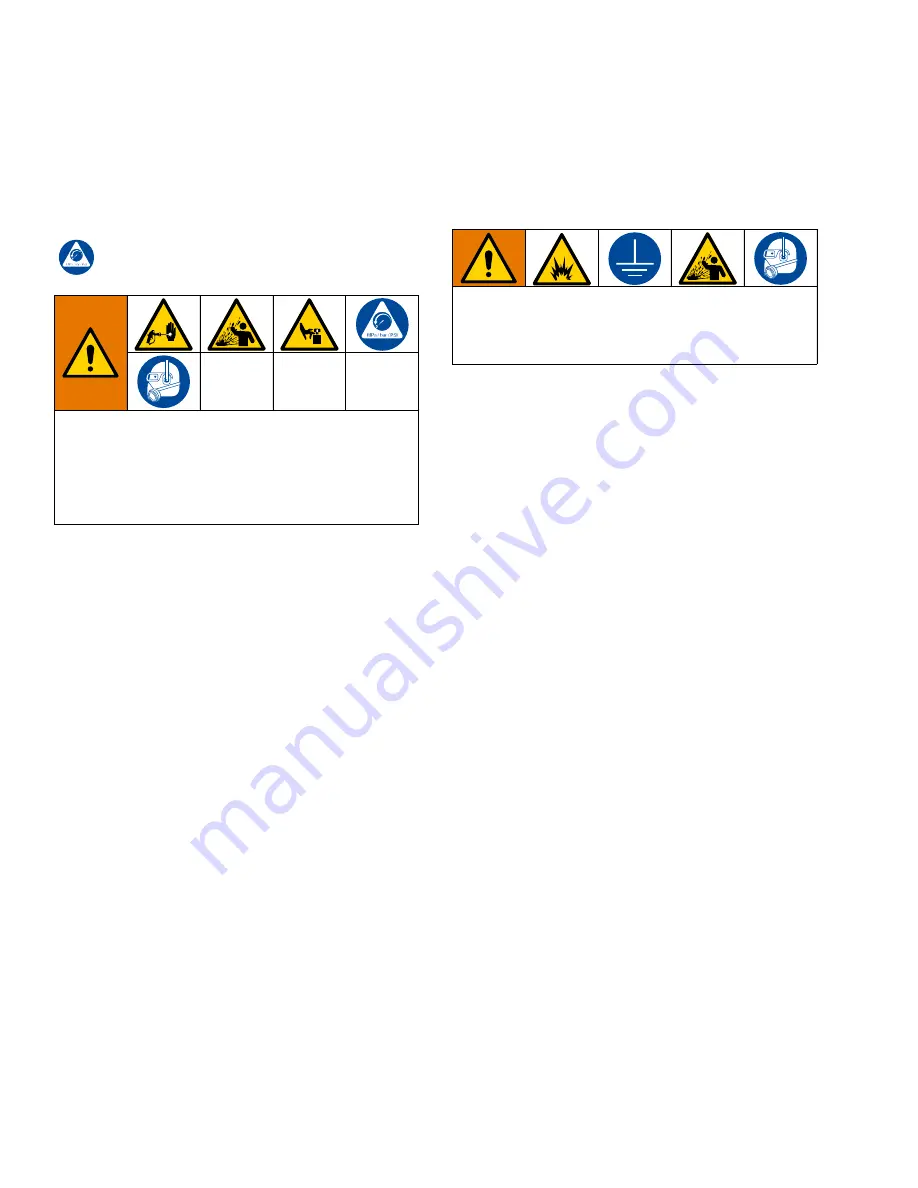
Operation
8
308360D
Operation
Pressure Relief Procedure
Follow the Pressure Relief Procedure whenever
you see this symbol.
1. Engage trigger lock.
2. Shut off the air supply to the pump.
3. Close the bleed-type master air valve.
4. Disengage the trigger lock.
5. Hold a metal part of the gun firmly to a grounded
metal pail. Trigger the gun to relieve pressure.
6. Engage the trigger lock.
7. Open all fluid drain valves in the system, having a
waste container ready to catch drainage. Leave
drain valve(s) open until you are ready to spray
again.
8. If you suspect the spray tip or hose is clogged or
that pressure has not been fully relieved:
a. VERY SLOWLY loosen the tip guard retaining
nut or the hose end coupling to relieve pressure
gradually.
b. Loosen the nut or the coupling completely.
c. Clear the obstruction in the hose or tip.
Flush the Equipment
•
Flush before fluid can dry in the equipment, at the
end of the day, before storing, and before repairing
equipment.
•
Flush at the lowest pressure possible. Check
connectors for leaks and tighten as necessary.
•
Flush with a fluid that is compatible with the fluid
being dispensed and the equipment wetted parts.
1. Perform
Pressure Relief Procedure
2. Remove spray tip from the gun.
3. Hold a metal part of the gun firmly to a grounded
metal pail.
4. Start the pump.
5. Trigger the gun until clean solvent dispenses.
6. Perform
Pressure Relief Procedure
This equipment stays pressurized until pressure is
manually relieved. To help prevent serious injury from
pressurized fluid, such as skin injection, splashing
fluid and moving parts, follow the Pressure Relief
Procedure when you stop spraying and before
cleaning, checking, or servicing the equipment.
To avoid fire and explosion, always ground equipment
and waste container. To avoid static sparking and
injury from splashing, always flush at the lowest
possible pressure.