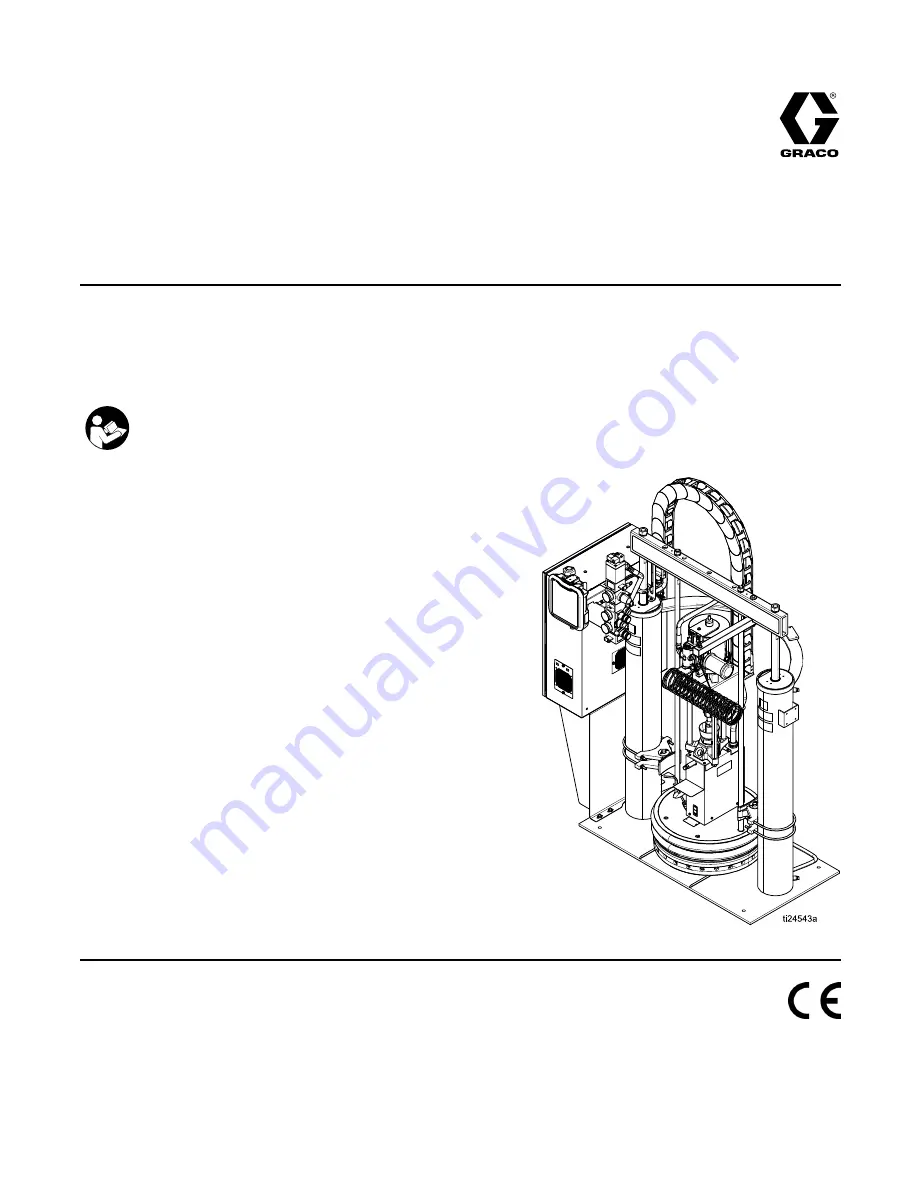
Instructions-Parts
Therm-O-Flow® 200
334130A
EN
For applying hot melt sealant and adhesive materials from 200 Liter (55 Gallon) drums. For professional
use only.
Not approved for use in European explosive atmosphere locations.
Important Safety Instructions
Read all warnings and instructions in this manual and in related
manuals. Save these instructions.
Maximum Operating Temperature 400°F
(204 °C)
See page 6 for model information.
See Technical Specifications, page 107,
for maximum working pressures.
PROVEN QUALITY. LEADING TECHNOLOGY.
Summary of Contents for 334130A
Page 10: ...Component Identification Electrical Control Enclosure Figure 3 Electrical Enclosure 10 334130A...
Page 57: ...Repair Figure 35 Inside of Electrical Control Enclosure 334130A 57...
Page 65: ...Parts Parts Therm O Flow 200 Supply Unit 334130A 65...
Page 68: ...Parts Electrical Module 68 334130A...
Page 69: ...Parts 334130A 69...